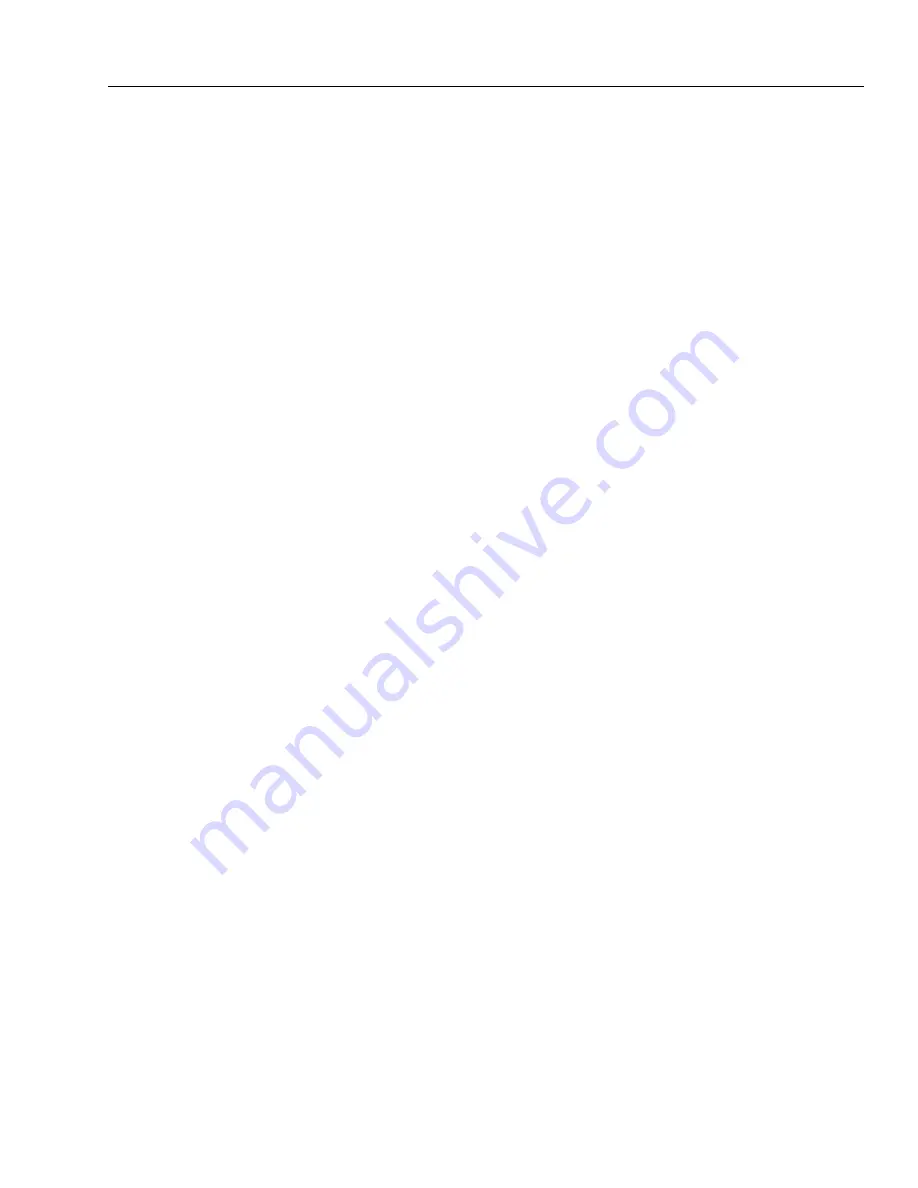
SECTION
4
- BOO
M
& PLATFOR
M
3121160
4-47
4.15 DRIVE CARD SETUP PROCEDURES
Lift, Swing, and Drive Cards
1.
Center the input potentiometers. Power up the card, but
do not start the engine. Place the common lead of a
voltmeter on pin #6 and place the other lead on pin #8.
Rotate the potentiometer, leaving the joystick in the
center position, until the voltmeter reads 2.5 volts.
Secure the set screw on the potentiometer. When the
potentiometer is centered and the joystick is in the cen-
ter position, LED #3 should not be illuminated.
2.
Install test harness JLG P/N 4922012.
3.
Set the minimum and maximum currents. The input
potentiometer must be centered before continuing with
this procedure. Power up the card, but do not start the
engine. Place the current meter in series with the “A”
output. Turn P3 counter clockwise until the adjustment
potentiometer starts to click. This will set to maximum
current to its lowest value. Move the joystick until LED
#3 illuminates and hold the stick in this position. Adjust
P4 until the meter equals the current setting range
given in Table 4-2, Ramp Current Setting Range. Rotat-
ing the adjustment potentiometer clockwise will
increase the current. This will set the minimum current
setting for the “A” output. To set the maximum current
for the “A” output, hold the joystick in its maximum posi-
tion. Turn P3 clockwise until the meter reading equals
the setting in Table 4-2, Ramp Current Setting Range.
Follow the same procedure for the “B” output. Use P8 for
the minimum current adjustment and P7 for the maxi-
mum current adjustment.
4.
Set the ramp up and the ramp down times. Step 2 must
be performed before continuing with procedure. Power
up the card, but do not start the engine. Place the cur-
rent meter in series with the “A” output. Move the joy-
stick from the center position to the extreme position.
Watch the meter for the time it takes the output to go to
from 0 current to maximum current. This is the ramp up
time. Adjust P1 until this time matches the time given
inTable 4-3, Ramp time Setting. Rotating the adjustment
potentiometer clockwise will increase the ramp time. To
set the ramp down time, hold the joystick in the extreme
position. Release the joystick and watch the meter for
the time it takes the output to go from the maximum
current setting to 0 current. Adjust P2 until this time
matches the time in Table 4-3, Ramp time Setting. Rotat-
ing the adjustment potentiometer clockwise will
increase the ramp time. Follow the same procedure for
the “B” output. Use P5 for the ramp up adjustment and
P6 for the ramp down adjustment.
Flow Control Card
1.
Set the input potentiometer. Power up the card, but do
not start the engine. Place the common lead of a volt-
meter on pin #15 and place the other lead on pin #8.
Rotate the potentiometer and verify the input to the
card is 3.8 volts when the input potentiometer is in its
minimum position. Rotate the input potentiometer to
its maximum position and verify the input to the card is
0 volts.
2.
Set the minimum and maximum current settings. The
input potentiometer must function properly before con-
tinuing with this procedure. Turn P3 counter clockwise
until the adjustment pot starts clicking. Place a current
meter in series with the “A” output. Rotate the input
potentiometer to its minimum setting and operate the
telescope function. Adjust P4 until the meter reading
matches the setting in Table 4-2, Ramp Current Setting
Range. This sets the minimum current setting for the
card. Rotate the input potentiometer to its extreme
position and operate the telescope function. Turn P3
clockwise until the meter reading matches the setting in
Table 4-2, Ramp Current Setting Range. This sets the
maximum current for the card.
3.
Set the ramp up and the down times. Step 2 must be
completed before continuing with this procedure.
Power up the card, but do not start the engine. Place the
current meter in series with the "A" output. Turn the
input potentiometer to its extreme position and operate
the telescope function. watch the meter for the time it
takes the output to go from 0 current to maximum cur-
rent. This is ramp up time. Adjust P1 until this time
matches the time in Table 4-3, Ramp time Setting. Rotat-
ing the adjustment potentiometer clockwise will
increase ramp time. To set the ramp down time, hold the
telescope function switch and watch the time it takes
the output to go from the maximum current down to 0
current. This is the ramp down time. Adjust P2 until this
time matches the setting time in Table 4-3, Ramp time
Setting. Rotating the adjustment potentiometer clock-
wise will increase the ramp time.
Содержание 740AJ
Страница 1: ...Service and Maintenance Manual Model 740AJ Prior to S N 0300185827 P N 3121160 October 24 2017 AS NZS...
Страница 2: ......
Страница 51: ...SECTION 2 GENERAL 3121160 2 11 Figure 2 2 Engine Operating Temperature Specifications Ford 4150548 E...
Страница 55: ...SECTION 3 CHASSIS TURNTABLE 3121160 3 3 This page left blank intentionally...
Страница 56: ...SECTION 3 CHASSIS TURNTABLE 3 4 3121160 1 Figure 3 2 Axle and Steering Installation Sheet 1 of 2 0258286 C...
Страница 100: ...SECTION 3 CHASSIS TURNTABLE 3 48 3121160 Figure 3 37 Swing Bearing Tolerance Boom Placement Sheet 1 of 2...
Страница 101: ...SECTION 3 CHASSIS TURNTABLE 3121160 3 49 Figure 3 38 Swing Bearing Tolerance Boom Placement Sheet 2 of 2...
Страница 116: ...SECTION 3 CHASSIS TURNTABLE 3 64 3121160 Figure 3 44 Swing Hub Prior to SN 0300074383...
Страница 124: ...SECTION 3 CHASSIS TURNTABLE 3 72 3121160 Figure 3 45 Swing Drive Hub Fairfield SN 0300074383 through 0300134352...
Страница 180: ...SECTION 3 CHASSIS TURNTABLE 3 128 3121160 1 Figure 3 66 Auxiliary Pump Location 1 AuxiliaryPump 2 HydraulicTank...
Страница 203: ...SECTION 3 CHASSIS TURNTABLE 3121160 3 151 Figure 3 77 EFI Component Location...
Страница 206: ...SECTION 3 CHASSIS TURNTABLE 3 154 3121160 Figure 3 78 ECM EPM Identification ECM EPM...
Страница 213: ...SECTION 3 CHASSIS TURNTABLE 3121160 3 161 Megajector Regulator LockoffSolenoid Figure 3 80 LPG System Components Mixer...
Страница 219: ...SECTION 3 CHASSIS TURNTABLE 3121160 3 167 Figure 3 81 Check Out and Initial Start Up Procedures...
Страница 224: ...SECTION 3 CHASSIS TURNTABLE 3 172 3121160 Figure 3 83 Deutz EMR 2 Troubleshooting Flow Chart...
Страница 225: ...SECTION 3 CHASSIS TURNTABLE 3121160 3 173 Figure 3 84 Deutz EMR 2 Vehicle Side Connection Diagram...
Страница 226: ...SECTION 3 CHASSIS TURNTABLE 3 174 3121160 Figure 3 85 Deutz EMR 2 Engine Side Connection Diagram Sheet 1 of 2...
Страница 227: ...SECTION 3 CHASSIS TURNTABLE 3121160 3 175 Figure 3 86 Deutz EMR 2 Engine Side Connection Diagram Sheet 2 of 2...
Страница 228: ...SECTION 3 CHASSIS TURNTABLE 3 176 3121160 Figure 3 87 EMR 2 Engine Plug Pin Identification...
Страница 229: ...SECTION 3 CHASSIS TURNTABLE 3121160 3 177 Figure 3 88 EMR 2 Vehicle Plug Pin Identification...
Страница 230: ...SECTION 3 CHASSIS TURNTABLE 3 178 3121160 Figure 3 89 EMR2 Fault Codes Sheet 1 of 5...
Страница 231: ...SECTION 3 CHASSIS TURNTABLE 3121160 3 179 Figure 3 90 EMR2 Fault Codes Sheet 2 of 5...
Страница 232: ...SECTION 3 CHASSIS TURNTABLE 3 180 3121160 Figure 3 91 EMR2 Fault Codes Sheet 3 of 5...
Страница 233: ...SECTION 3 CHASSIS TURNTABLE 3121160 3 181 Figure 3 92 EMR2 Fault Codes Sheet 4 of 5...
Страница 234: ...SECTION 3 CHASSIS TURNTABLE 3 182 3121160 Figure 3 93 EMR2 Fault Codes Sheet 5 of 5...
Страница 303: ...SECTION 4 BOOM PLATFORM 3121160 4 31 Figure 4 20 Rotator Assembly HELAC...
Страница 335: ...SECTION 4 BOOM PLATFORM 3121160 4 63 THIS SENSOR ON NON ADE MACHINES ONLY Figure 4 27 UMS Sensor Location...
Страница 336: ...SECTION 4 BOOM PLATFORM 4 64 3121160 Figure 4 28 UMS Module Location ADE MACHINES NON ADE MACHINES...
Страница 425: ...SECTION 5 BASIC HYDRAULIC INFORMATION AND SCHEMATICS 3121160 5 81 Figure 5 131 Variable Displacement Pump Rexroth...
Страница 443: ...SECTION 5 BASIC HYDRAULIC INFORMATION AND SCHEMATICS 3121160 5 99 Figure 5 146 Fault Logic Troubleshooting...
Страница 444: ...SECTION 5 BASIC HYDRAULIC INFORMATION AND SCHEMATICS 5 100 3121160 Figure 5 147 Fault Logic Troubleshooting...
Страница 445: ...SECTION 5 BASIC HYDRAULIC INFORMATION AND SCHEMATICS 3121160 5 101 Figure 5 148 Fault Logic Troubleshooting...
Страница 460: ...SECTION 5 BASIC HYDRAULIC INFORMATION AND SCHEMATICS 5 116 3121160 NOTES...
Страница 467: ...SECTION 6 JLG CONTROL SYSTEM 3121160 6 7 Figure 6 2 ADE Block Diagram...
Страница 471: ...SECTION 6 JLG CONTROL SYSTEM 3121160 6 11 Figure 6 6 Analyzer Flow Chart Prior to Version 5 X Software Sheet 4 of 4...
Страница 473: ...SECTION 6 JLG CONTROL SYSTEM 3121160 6 13 Figure 6 8 Analyzer Flow Chart Version 5 X Software Sheet 2 of 4...
Страница 534: ...SECTION 6 JLG CONTROL SYSTEM 6 74 3121160 NOTES...
Страница 545: ...SECTION 7 BASIC ELECTRICAL INFORMATION SCHEMATICS 3121160 7 11 Figure 7 15 Connector Installation...
Страница 580: ...SECTION 7 BASIC ELECTRICAL INFORMATION SCHEMATICS 7 46 3121160 NOTES...
Страница 581: ......