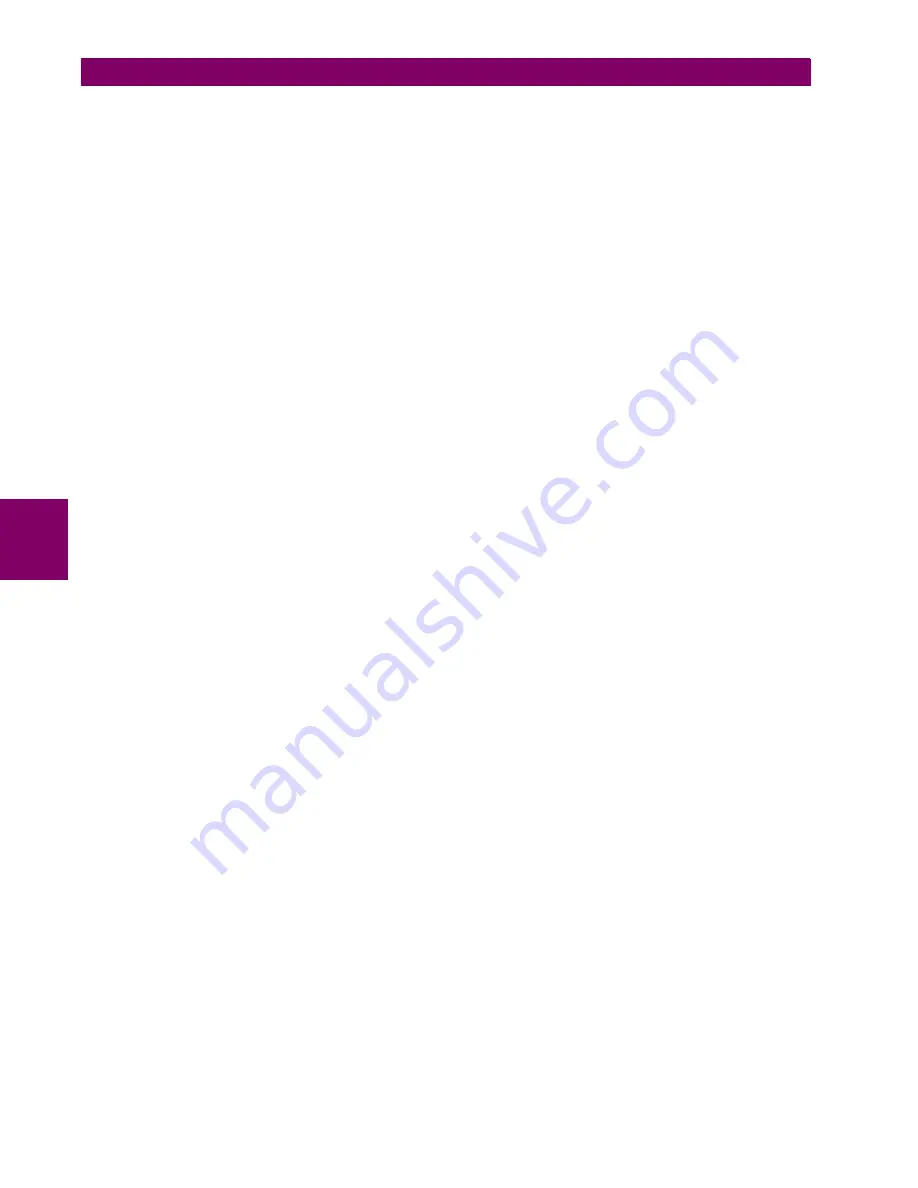
5-110
G30 Generator Protection System
GE Multilin
5.4 SYSTEM SETUP
5 SETTINGS
5
The unit for calculation of the differential and restraint currents and base for the differential restraint settings is the CT pri-
mary associated with the reference winding. In this example, the unit CT is 1500:5 on winding 2.
Magnitude compensation factors (
M
) are the scaling values by which each winding current is multiplied to refer it to the ref-
erence winding. The G30 calculates magnitude compensation factors for each winding as follows:
(EQ 5.11)
In our example, the magnitude compensation factors are calculated as follows:
(EQ 5.12)
(EQ 5.13)
The maximum allowed magnitude compensation factor (and hence the maximum allowed CT ratio mismatch) is 32.
f) PHASE AND ZERO SEQUENCE COMPENSATION
Power transformers may be connected to provide phase shift, such as the common
Δ
-Y connection with its 30° phase shift.
Historically, CT connections were arranged to compensate for this phase error so that the relaying could operate correctly.
In our example, the transformer has the
Δ
-Y connection. Traditionally, CTs on the Wye connected transformer winding
(winding 2) would be connected in a delta arrangement, which compensates for the phase angle lag introduced in the Delta
connected winding (winding 1), so that line currents from both windings can be compared at the relay. The Delta connection
of CTs, however, inherently has the effect of removing the zero sequence components of the phase currents. If there were
a grounding bank on the Delta winding of the power transformer within the zone of protection, a ground fault would result in
differential (zero sequence) current and false trips. In such a case, it would be necessary to insert a zero sequence current
trap with the Wye connected CTs on the Delta winding of the transformer.
In general, zero sequence removal is necessary if zero sequence can flow into and out of one transformer winding but not
the other winding. Transformer windings that are grounded inside the zone of protection allow zero sequence current flow
in that winding, and therefore it is from these windings that zero sequence removal is necessary.
The G30 performs this phase angle compensation and zero sequence removal automatically, based on the settings
entered for the transformer. All CTs are connected Wye (polarity markings pointing away from the transformer). All currents
are phase and zero sequence compensated internally before the calculation of differential and restraint quantities.
The phase reference winding (
w
f
) is the winding which will have a phase shift of 0° applied to it. The phase reference wind-
ing is chosen to be the delta or zigzag (non-wye) winding with the lowest winding index, if one exists. For a transformer that
has no delta or zigzag windings, the first winding is chosen.
The phase compensation angle (
Φ
comp
), the angle by which a winding current is shifted to refer it to the phase reference
winding, is calculated by the T60 for each winding as follows:
Φ
comp
[
w
] = |
Φ
[
w
f
] –
Φ
[
w
] | where Rotation = “ABC”
Φ
comp
[
w
] = |
Φ
[
w
] –
Φ
[
w
f
] | where Rotation = “ACB”
In our example, the phase reference winding would be winding 1, the first delta winding (i.e.
w
f
= 1). The phase compensa-
tion angle for each winding would then be calculated as follows (assuming Rotation = “ABC”):
Φ
comp
[1] = 0° – 0° = 0°
Φ
comp
[2] = 0° – (–30°) = 30° = 330° lag
The following table shows the linear combination of phases of a transformer winding that achieves the phase shift and zero
sequence removal for typical values of
Φ
comp
:
where:
I
A
[
w
] = uncompensated winding ‘
w
’ phase A current
I
A
p
[
w
] = phase and zero sequence compensated winding ‘
w
’ phase A current
M w
[ ]
I
primary
w
[ ]
V
nom
w
[ ]
×
I
primary
w
ref
[
]
V
nom
w
ref
[
]
×
----------------------------------------------------------------------
, where
w
1 2
,
=
=
M
1
[ ]
I
primary
1
[ ]
V
nom
1
[ ]
×
I
primary
2
[ ]
V
nom
2
[ ]
×
--------------------------------------------------------
500 A 220 kV
×
1500 A 69 kV
×
-----------------------------------------
1.0628
=
=
=
M
2
[ ]
I
primary
2
[ ]
V
nom
2
[ ]
×
I
primary
2
[ ]
V
nom
2
[ ]
×
--------------------------------------------------------
1500 A 69 kV
×
1500 A 69 kV
×
-----------------------------------------
1.0000
=
=
=
Содержание G30
Страница 10: ...x G30 Generator Protection System GE Multilin TABLE OF CONTENTS ...
Страница 30: ...1 20 G30 Generator Protection System GE Multilin 1 5 USING THE RELAY 1 GETTING STARTED 1 ...
Страница 414: ...5 274 G30 Generator Protection System GE Multilin 5 10 TESTING 5 SETTINGS 5 ...
Страница 456: ...8 2 G30 Generator Protection System GE Multilin 8 1 DIRECTIONAL PRINCIPLE 8 THEORY OF OPERATION 8 ...
Страница 470: ...9 14 G30 Generator Protection System GE Multilin 9 1 SETTING EXAMPLE 9 APPLICATION OF SETTINGS 9 ...
Страница 484: ...11 12 G30 Generator Protection System GE Multilin 11 6 DISPOSAL 11 MAINTENANCE 11 ...
Страница 512: ...A 28 G30 Generator Protection System GE Multilin A 1 PARAMETER LISTS APPENDIX A A ...
Страница 620: ...B 108 G30 Generator Protection System GE Multilin B 4 MEMORY MAPPING APPENDIX B B ...
Страница 666: ...E 10 G30 Generator Protection System GE Multilin E 1 IEC 60870 5 104 APPENDIX E E ...
Страница 678: ...F 12 G30 Generator Protection System GE Multilin F 2 DNP POINT LISTS APPENDIX F F ...
Страница 687: ...GE Multilin G30 Generator Protection System H 7 APPENDIX H H 2 ABBREVIATIONS H Z Impedance Zone ...