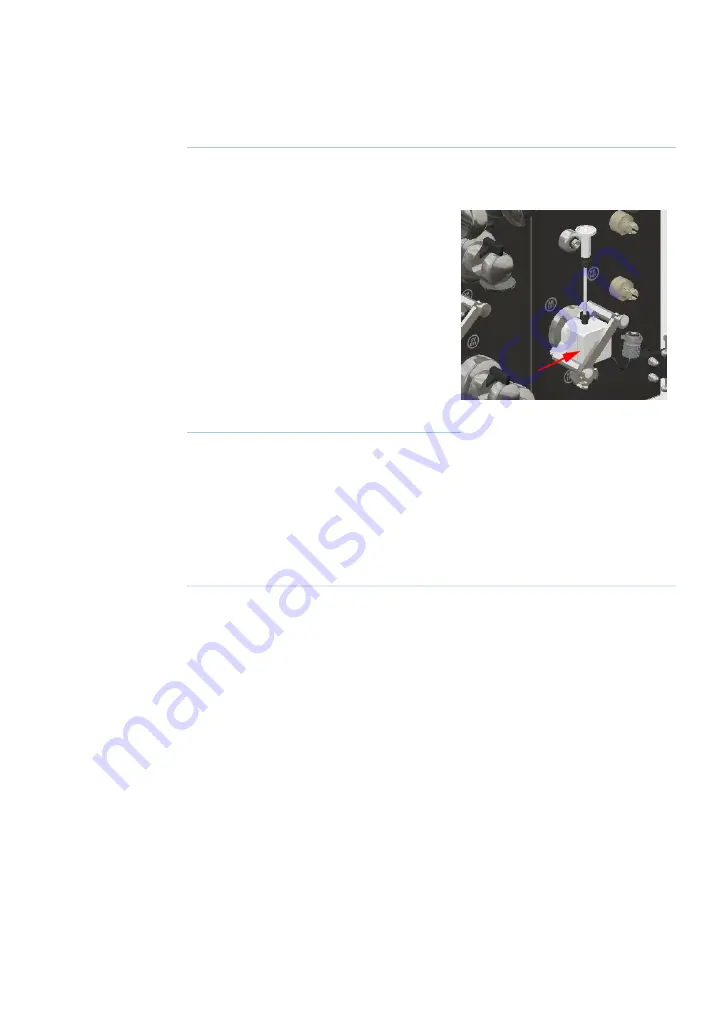
Action
Step
Release the pressure and verify that the pressure reading is 0.00 ± 0.01 bar
at atmospheric pressure.
5
Remove the calibration cell and verify
that the reading now is -0.20 bar or
less (if it is not, contact GE
Healthcare).
6
PT-111 is now calibrated. Repeat the
procedure for pressure sensors PT-
112 and PT-113.
Note that PT-112 differs in the
mounting of the calibration cell — an
extra block must be inserted (arrow
in figure) to compensate for the larger
distance.
7
Calibrating conductivity sensor
Calibration of the conductivity sensor is normally not necessary in UNICORN
because a standard setting of the cell constant is used.
Note:
The procedure for calibrating the conductivity sensor is shown in the following steps:
Action
Step
Prepare a calibration solution of 1.00 M NaCl, 58.44 g/1000 ml. Let the solu-
tion reach room temperature. This is important for exact measurements.
1
Set temperature compensation factor (CompFactor) to zero. The CompFactor
instruction is found under Monitors in the Settings dialog box.
2
Fill the cell completely with the calibration solution by pumping at least 15 ml
through the cell using a syringe.
3
ÄKTA ready Operating Instructions 28960345 AD
189
12 Maintenance
12.2 Yearly maintenance