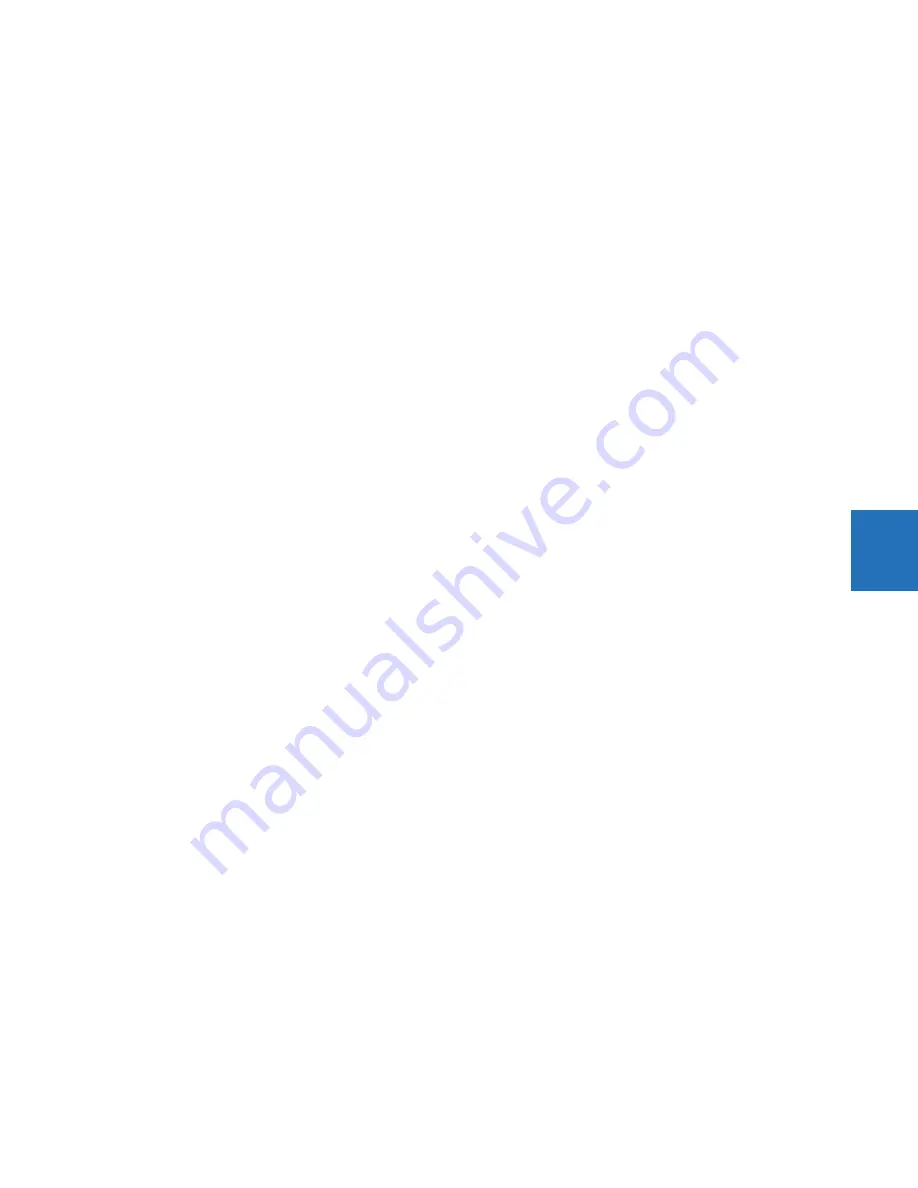
CHAPTER 5: SETTINGS
INPUTS/OUTPUTS
L60 LINE PHASE COMPARISON SYSTEM – INSTRUCTION MANUAL
5-317
5
The L60 latching output contacts are mechanically bi-stable and controlled by two separate (open and close) coils. As such
they retain their position even if the relay is not powered up. The relay recognizes all latching output contact cards and
populates the setting menu accordingly. On power up, the relay reads positions of the latching contacts from the hardware
before executing any other functions of the relay (such as protection and control features or FlexLogic).
The latching output modules, either as a part of the relay or as individual modules, are shipped from the factory with all
latching contacts opened. It is highly recommended to double-check the programming and positions of the latching
contacts when replacing a module.
Since the relay asserts the output contact and reads back its position, it is possible to incorporate self-monitoring
capabilities for the latching outputs. If any latching outputs exhibits a discrepancy, the LATCHING OUTPUT ERROR self-test
error is declared. The error is signaled by the
LATCHING OUT ERROR
FlexLogic operand, event, and target message.
OUTPUT H1a OPERATE
— This setting specifies a FlexLogic operand to operate the ‘close coil’ of the contact. The relay seals-
in this input to safely close the contact. Once the contact is closed and the
RESET
input is logic 0 (off), any activity of the
OPERATE
input, such as subsequent chattering, does not have any effect. With both the
OPERATE
and
RESET
inputs active
(logic 1), the response of the latching contact is specified by the
OUTPUT H1a TYPE
setting.
OUTPUT H1a RESET
— This setting specifies a FlexLogic operand to operate the ‘trip coil’ of the contact. The relay seals-in
this input to safely open the contact. Once the contact is opened and the
OPERATE
input is logic 0 (off), any activity of the
RESET
input, such as subsequent chattering, does not have any effect. With both the
OPERATE
and
RESET
inputs active (logic
1), the response of the latching contact is specified by the
OUTPUT H1a TYPE
setting.
OUTPUT H1a TYPE
— This setting specifies the contact response under conflicting control inputs; that is, when both the
OPERATE
and
RESET
signals are applied. With both control inputs applied simultaneously, the contact closes if set to
“Operate-dominant” and opens if set to “Reset-dominant.”
Application example 1
A latching output contact H1a is to be controlled from two user-programmable pushbuttons (buttons number 1 and 2). The
following settings are applied.
Program the Latching Outputs by making the following changes in the
SETTINGS
INPUTS/OUTPUTS
CONTACT
OUTPUTS
CONTACT OUTPUT H1a
menu (assuming an H4L module):
OUTPUT H1a OPERATE
: “
PUSHBUTTON 1 ON
”
OUTPUT H1a RESET
: “
PUSHBUTTON 2 ON
”
Program the pushbuttons by making the following changes in the
PRODUCT SETUP
USER-PROGRAMMABLE PUSHBUTTONS
USER PUSHBUTTON 1
and
USER PUSHBUTTON 2
menus:
PUSHBUTTON 1 FUNCTION
: “Self-reset”
PUSHBTN 1 DROP-OUT TIME
: “0.00 s”
PUSHBUTTON 2 FUNCTION
: “Self-reset”
PUSHBTN 2 DROP-OUT TIME
: “0.00 s”
Application example 2
A relay, having two latching contacts H1a and H1c, is to be programmed. The H1a contact is to be a Type-a contact, while
the H1c contact is to be a Type-b contact (Type-a means closed after exercising the operate input; Type-b means closed
after exercising the reset input). The relay is to be controlled from virtual outputs: VO1 to operate and VO2 to reset.
Program the Latching Outputs by making the following changes in the
SETTINGS
INPUTS/OUTPUTS
CONTACT
OUTPUTS
CONTACT OUTPUT H1a
and
CONTACT OUTPUT H1c
menus (assuming an H4L module):
OUTPUT H1a OPERATE
: “
VO1
”
OUTPUT H1a RESET
: “
VO2
”
OUTPUT H1c OPERATE
: “
VO2
”
OUTPUT H1c RESET
: “
VO1
”
Since the two physical contacts in this example are mechanically separated and have individual control inputs, they do not
operate at exactly the same time. A discrepancy in the range of a fraction of a maximum operating time can occur.
Therefore, a pair of contacts programmed to be a multi-contact relay do not guarantee any specific sequence of operation
(such as make before break). If required, the sequence of operation must be programmed explicitly by delaying some of the
control inputs as shown in the next application example.
Содержание L60
Страница 130: ...4 30 L60 LINE PHASE COMPARISON SYSTEM INSTRUCTION MANUAL LOGIC DIAGRAMS CHAPTER 4 INTERFACES 4 ...
Страница 464: ...5 334 L60 LINE PHASE COMPARISON SYSTEM INSTRUCTION MANUAL TESTING CHAPTER 5 SETTINGS 5 ...
Страница 498: ...7 10 L60 LINE PHASE COMPARISON SYSTEM INSTRUCTION MANUAL TARGETS MENU CHAPTER 7 COMMANDS AND TARGETS 7 ...
Страница 570: ...10 14 L60 LINE PHASE COMPARISON SYSTEM INSTRUCTION MANUAL DISPOSAL CHAPTER 10 MAINTENANCE 10 ...
Страница 582: ...A 12 L60 LINE PHASE COMPARISON SYSTEM INSTRUCTION MANUAL FLEXANALOG ITEMS APPENDIX A FLEXANALOG OPERANDS A ...
Страница 588: ...C 4 L60 LINE PHASE COMPARISON SYSTEM INSTRUCTION MANUAL REVISION HISTORY APPENDIX C MISCELLANEOUS C ...
Страница 592: ...iv L60 LINE PHASE COMPARISON SYSTEM INSTRUCTION MANUAL ABBREVIATIONS ...