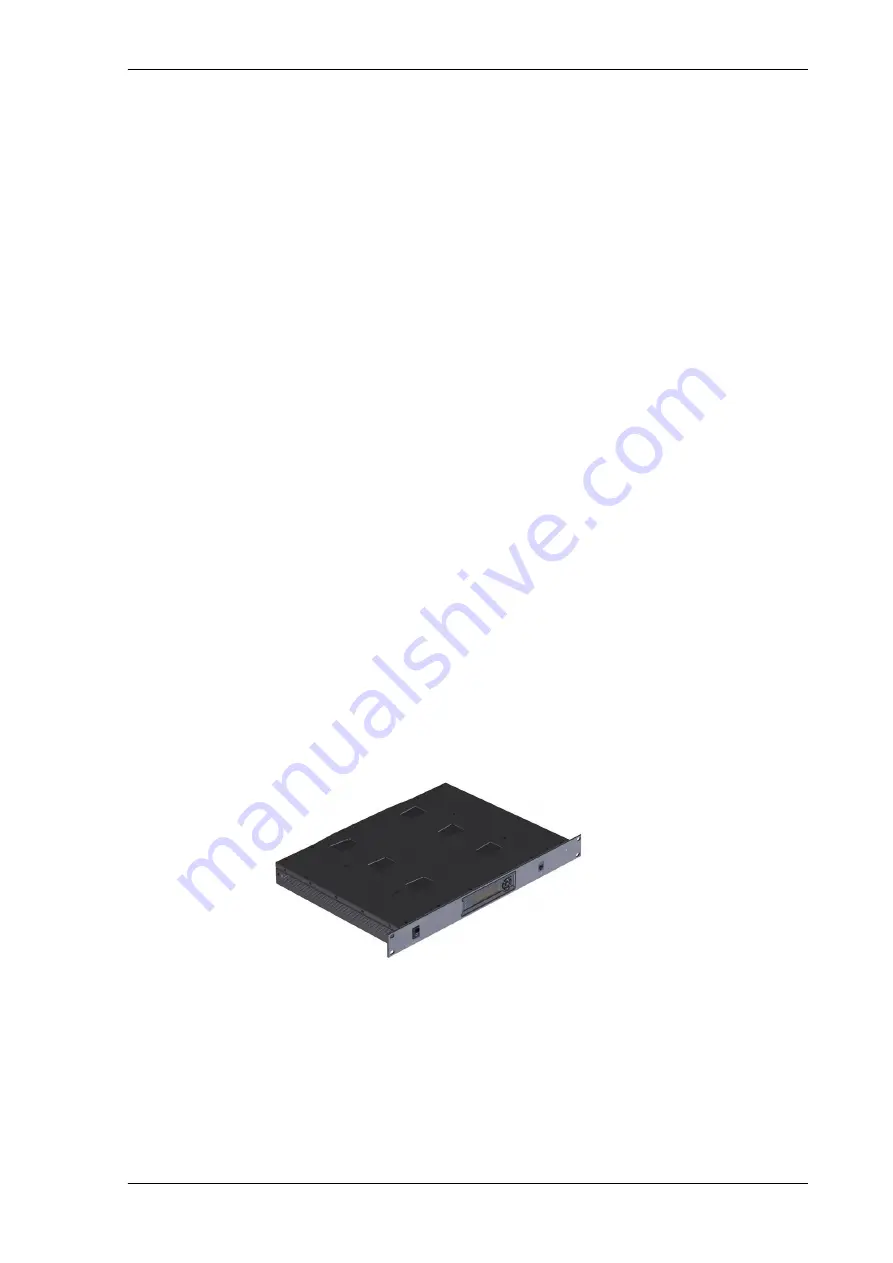
FV-110GX system
1-5
20.Feed horn.
Four lifting brackets (included in the delivery) and reuse of packing material help getting
the ADU safely into place. Satellite profile parameters are entered in the built-in web
server of the ACU, using a PC.
The system configuration is saved in two modules, there is no loss of data at repair. The
large service hatch of the radome gives easy access to the ADU on site. The service
switch in the ADU stops the DC Motor Driver modules and turns the BUC off. The
service tools for replacing modules are placed on a tool holder inside the radome.
All modules have a service and power LED status indicator. Each module is encapsulated
in a metal box with self-contained mounting bolts. If necessary, belts and modules can be
exchanged through the service hatch on site.
You can do remote diagnostics and service with the ADU. Its built-in test equipment
checks constantly the modules for proper functioning, it monitors and logs information
for all modules. The ADU performs a POST (Power On Self Test) and you can request a
self test (PAST, Person Activated Self Test) and Continuous Monitoring (CM). Error
codes can be read out in the web interface and in the display of the ACU.
The ADU software is updated automatically when making a software update of the ACU.
1.1.3
Antenna Control Unit (ACU)
The ACU is the central control unit in the system. It contains all user interfaces and
manages all communication between the ADU and the connected GMU, a connected PC
and an optional FleetBroadband service communication line. The ACU has a display,
status LEDs and a keypad. It provides a DHCP client. During configuration you can
configure heading offset, save satellite setups and enter
No Transmit Zones
(blocking
zones in which the ADU does not transmit).
The user PC (user WAN) for Internet access etc. is connected to the ACU, not the GMU.
The ACU provides DC power to the ADU through a single coaxial cable. The ACU
comes in a 19” rack version.
You can do remote diagnostics and service with the ACU. Its built-in test equipment
checks constantly the device for proper functioning. It performs POST (Power On Self
Test) and you can request a PAST (Person Activated Self Test). Continuous Monitoring
(CM) is also available. BITE error codes can be read out in the web interface and in the
display of the ACU.
Figure 1-6: Antenna Control Unit
Содержание FV-110GX
Страница 1: ...GX TERMINAL FV 110GX OPERATOR S MANUAL www furuno com Model ...
Страница 16: ...xiv This page is intentionally left blank ...
Страница 46: ...Installation of the ADU 2 22 N connector interface on the ADU ...
Страница 54: ...To connect the ADU ACU and GMU 2 30 This page is intentionally left blank ...
Страница 110: ...Installation check list Functional test in harbor 6 4 This page is intentionally left blank ...
Страница 135: ...Alternative ground for steel hulls A 5 Figure A 3 Grounding at a dedicated RF ground alternative ...
Страница 164: ...Supported commands C 10 This page is intentionally left blank ...
Страница 165: ...D 1 Appendix D Approvals D This appendix lists the approvals for FV 110GX OEM declaration ...
Страница 166: ...OEM declaration D 2 D 1 OEM declaration ...
Страница 173: ...OD 1 30 Jul 2018 H MAKI ...
Страница 174: ...OD 2 30 Jul 2018 H MAKI ...
Страница 175: ...OD 3 2 Oct 2018 H MAKI ...
Страница 176: ...OD 4 2 Oct 2018 H MAKI ...
Страница 178: ......
Страница 186: ......