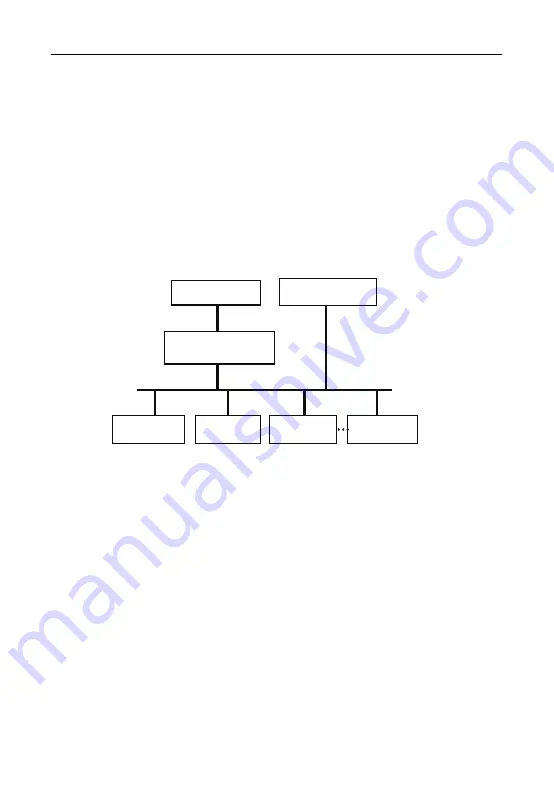
Modbus communication protocol
75
Appendix A Modbus Communication Protocol
A.1 Summary
We provide general RS485 communication interface in our inverters for the user. Through
this communication interface upper device (such as HMI, PC, PLC controller and etc.) can
perform centralized monitor to the inverter (such as to set inverter parameter, control run of
inverter, read work state of the inverter).
This communication protocol is interface criterion file designed for realizing
above-mentioned function, please read it earnestly and program according to it so that realize
long-distance and network control to the inverter.
A.2 Communication networking mode
Fig.A-1 Networking graph
A.3 Communication mode
At present,EN600PV inverter can be used only as Slave device in RS485 net. Can realize
communication between inverters through PC, PLC or HMI if it needed. Specific communication
mode is as mentioned below:
(1) PC or PLC as mainframe
,
inverter as Slave device, point-to-point communication
between mainframe and Slave device.
(2) Slave device don’t response when mainframe send out command by broadcast address.
(3) User can set local address, baud rate and data format of the inverter through Slave device
keypad or serial communication mode.
(4) EN600PV provides the RS485 interface.
(5) Default mode: Asynchronous serial
,
semiduplex transport mode. There are RTU and
ASCII two mode . Default format and transport rate: 8-N-1, 9600bps.
A.4 Transmission mode
Asynchronous serial, semiduplex transport mode. Default format and transport rate: 8-N-1,
9600bps. The detail setting parameter, please refer to the F05 group function mode.(Remark: the
parameter is valid under the Modbus communication, the other parameter comply with the original
service manual)
mainframe is PC
mainframe is PLC
232-485
conversion
module
EN600PV
EN600PV
EN600PV
EN600PV
or
RS232
RS485
ENC