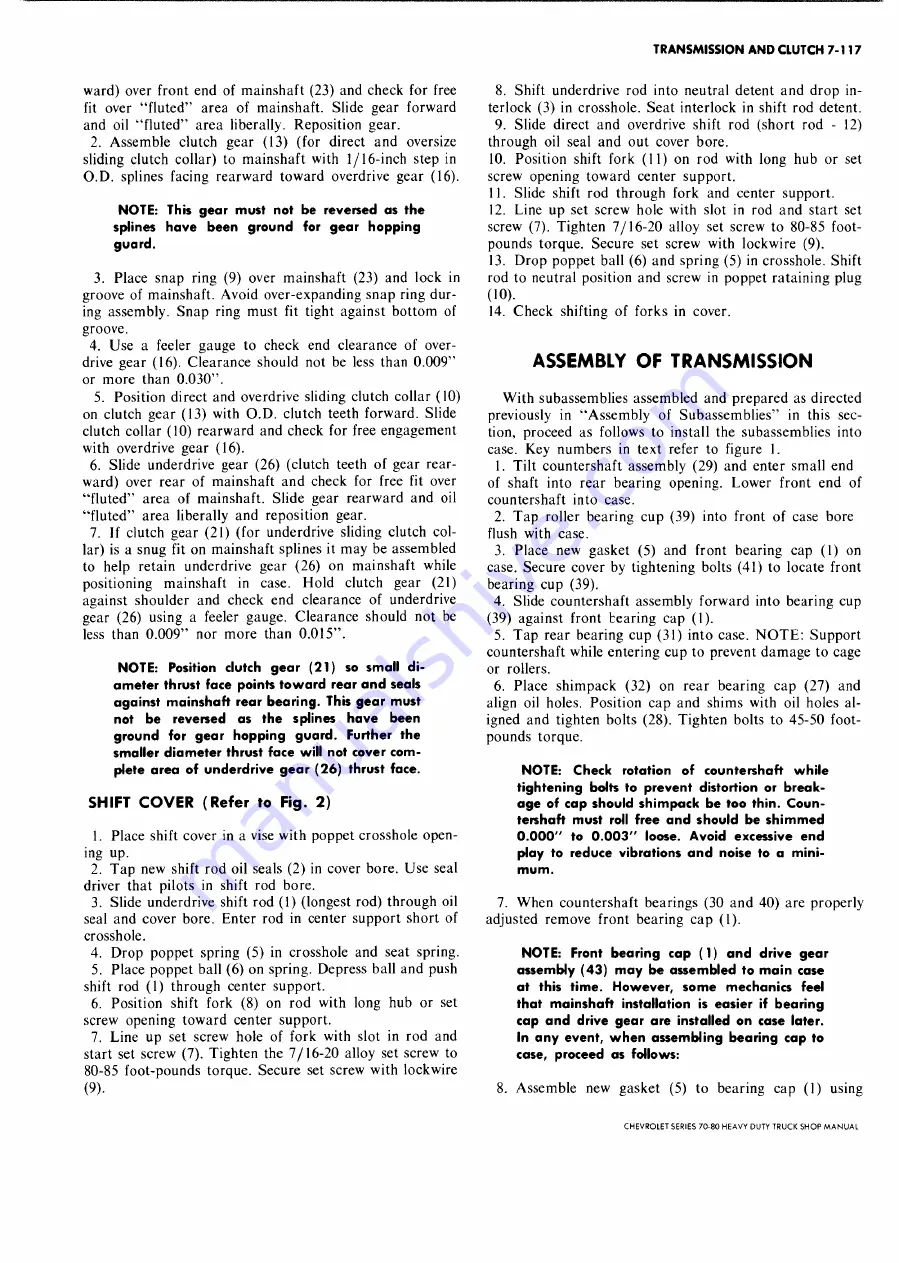
TRANSMISSION AND CLUTCH 7-117
ward) over front end of m ainshaft (23) and check for free
fit over “ fluted” area of m ainshaft. Slide gear forward
and oil “ fluted” area liberally. Reposition gear.
2. Assem ble clutch gear (13) (for direct and oversize
sliding clutch collar) to m ainshaft with 1/16-inch step in
O.D. splines facing rearw ard tow ard overdrive gear (16).
NOTE: This gear must not be reversed as the
splines have been ground for gear hopping
guard.
3. Place snap ring (9) over m ainshaft (23) and lock in
groove of m ainshaft. Avoid over-expanding snap ring d u r
ing assembly. Snap ring m ust fit tight against bottom of
groove.
4. Use a feeler gauge to check end clearance of over
drive gear (16). C learance should not be less than 0.009”
or m ore than 0.030” .
5. Position direct and overdrive sliding clutch collar (10)
on clutch gear (13) with O .D. clutch teeth forward. Slide
clutch collar (10) rearw ard and check for free engagem ent
with overdrive gear (16).
6. Slide underdrive gear (26) (clutch teeth of gear rear
ward) over rear of m ainshaft an d check for free fit over
“ fluted” area of m ainshaft. Slide gear rearw ard and oil
“ fluted” area liberally and reposition gear.
7. If clutch gear (21) (for underdrive sliding clutch col
lar) is a snug fit on m ainshaft splines it m ay be assembled
to help retain underdrive gear (26) on m ainshaft while
positioning m ainshaft in case. H old clutch gear (21)
against shoulder and check end clearance of underdrive
gear (26) using a feeler gauge. C learance should not be
less than 0.009” nor m ore than 0.015” .
NOTE: Position clutch gear (21) so small di
ameter thrust face points toward rear and seals
against mainshaft rear bearing. This gear must
not be reversed as the splines have been
ground for gear hopping guard. Further the
smaller diameter thrust face will not cover com
plete area of underdrive gear (26) thrust face.
SHIFT COVER (Refer to Fig. 2)
1. Place shift cover in a vise with poppet crosshole open
ing up.
2. T ap new shift rod oil seals (2) in cover bore. Use seal
driver that pilots in shift rod bore.
3. Slide underdrive shift rod (1) (longest rod) through oil
seal and cover bore. Enter rod in center support short of
crosshole.
4. D rop poppet spring (5) in crosshole and seat spring.
5. Place poppet ball (6) on spring. Depress ball and push
shift rod (1) through center support.
6. Position shift fork (8) on rod with long hub or set
screw opening tow ard center support.
7. Line up set screw hole of fork with slot in rod and
start set screw (7). Tighten the 7/16-20 alloy set screw to
80-85 foot-pounds torque. Secure set screw with lockwire
(9).
8. Shift underdrive rod into neutral detent an d drop in
terlock
(3)
in crosshole. Seat interlock in shift rod detent.
9.
Slide direct and overdrive shift rod (short rod -
12)
through oil seal and out cover bore.
10.
Position shift fork
(11)
on rod with long hub or set
screw opening tow ard center support.
11. Slide shift rod through fork and center support.
12.
Line up set screw hole with slot in rod and start set
screw
(7).
Tighten
7/16-20
alloy set screw to
80-85
foot
pounds torque. Secure set screw with lockwire
(9).
13.
D rop poppet ball
(6)
and spring
(5)
in crosshole. Shift
rod to neutral position and screw in poppet rataining plug
(
10
).
14.
Check shifting of forks in cover.
ASSEMBLY OF T R A N SM ISSIO N
W ith subassemblies assem bled and prepared as directed
previously in “ A ssem bly of Subassem blies” in this sec
tion, proceed as follows to install the subassem blies into
case. Key num bers in text refer to figure
1.
1.
Tilt countershaft assem bly
(29)
and enter small end
of shaft into rear bearing opening. Lower front end of
countershaft into case.
2.
T ap roller bearing cup
(39)
into front of case bore
flush with case.
3.
Place new gasket
(5)
and front bearing cap
(1)
on
case. Secure cover by tightening bolts (41) to locate front
bearing cup
(39).
4.
Slide countershaft assem bly forw ard into bearing cup
(39)
against front tea rin g cap
(1).
5.
T ap rear bearing cup
(31)
into case. N O T E : Support
countershaft while entering cup to prevent dam age to cage
or rollers.
6.
Place shim pack
(32)
on rear bearing cap
(27)
and
align oil holes. Position cap and shims with oil holes al
igned and tighten bolts
(28).
Tighten bolts to
45-50
foot
pounds torque.
NOTE: Check rotation of countershaft while
tightening bolts to prevent distortion or break
age of cap should shimpack be too thin. Coun
tershaft must roll free and should be shimmed
0.000" to 0.003" loose. Avoid excessive end
play to reduce vibrations and noise to a mini
mum.
7.
W hen countershaft bearings
(30
and
40)
are properly
adjusted remove front bearing cap (1).
NOTE: Front bearing cap (1) and drive gear
assembly (43) may be assembled to main case
at this time. However, some mechanics feel
that mainshaft installation is easier if bearing
cap and drive gear are installed on case later.
In any event, when assembling bearing cap to
case, proceed as follows:
8.
Assem ble new gasket
(5)
to bearing cap
(1)
using
CHEVROLET SERIES 70-80 H EAVY DUTY TRUCK SH O P M A N U A L
Содержание 70 1969 Series
Страница 1: ...CHEVROLET HEAVY DUTY TRUCK SHOP MANUAL...
Страница 3: ......
Страница 11: ...LUBRICATION 0 4 CHEVROLET SERIES 70 80 HEAVY DUTY TRUCK SHOP MANUAL...
Страница 27: ......
Страница 119: ......
Страница 361: ......
Страница 371: ......
Страница 403: ...TROUBLE ANALYSIS CHART ENGINE ELECTRICAL 6Y 32 CHEVROLET SERIES 70 80 HEAVY DUTY TRUCK SHOP MANUAL...
Страница 427: ......
Страница 443: ......
Страница 451: ......
Страница 493: ......
Страница 499: ......
Страница 549: ......
Страница 555: ......
Страница 609: ......
Страница 715: ...am...
Страница 745: ......
Страница 807: ...TRANSMISSION AND CLUTCH 7 61 CHEVROLET SERIES 70 80 HEAVY DUTY TRUCK SHOP M AN U AL Kgure 2 Clark 401 Transmission...
Страница 910: ......
Страница 913: ......