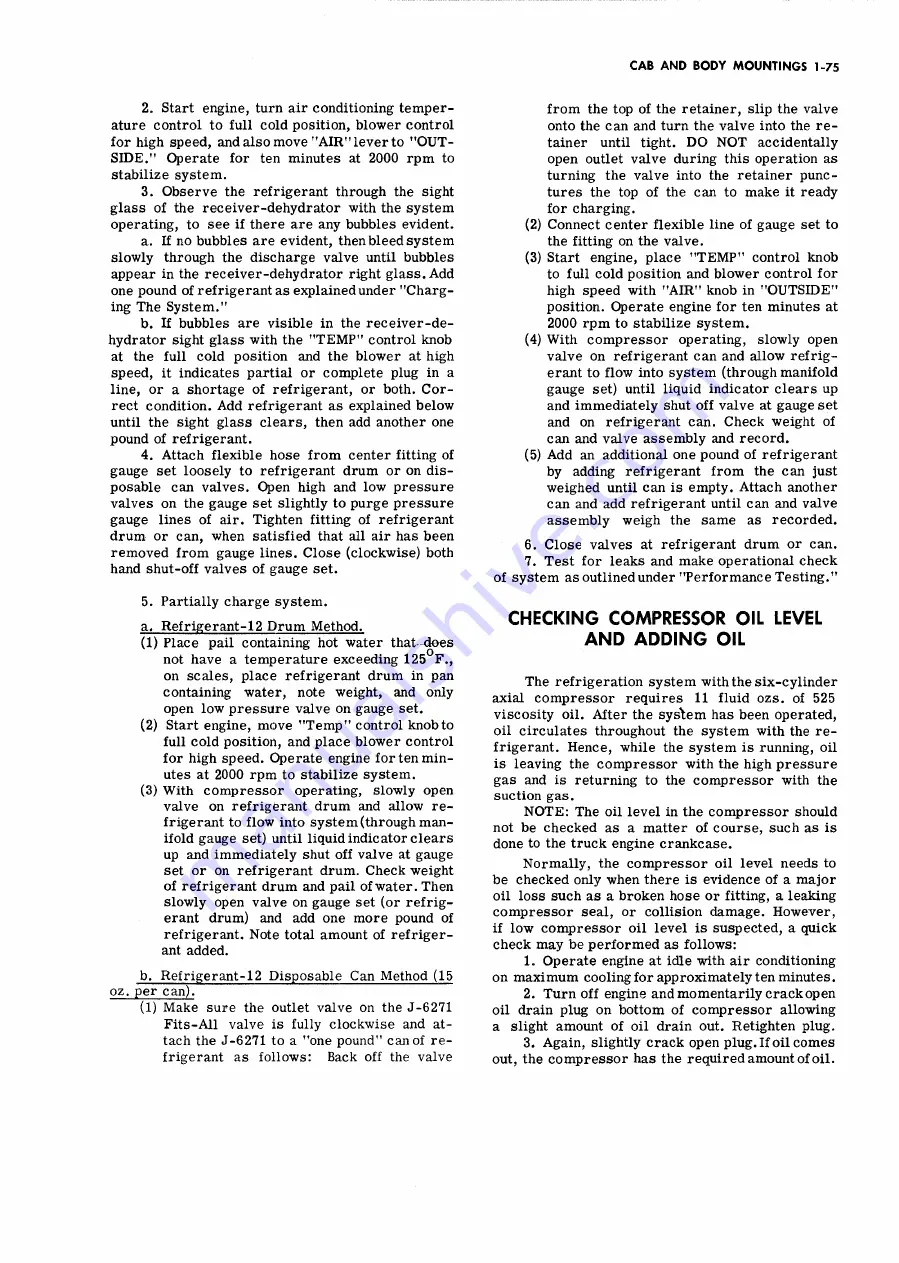
CAB A N D BO DY M O U N T IN G S 1-75
2. Start engine, turn air conditioning temper
ature control to full cold position, blower control
for high speed, and also move "A IR " lever to " O U T
S ID E ." Operate for ten minutes at 2000 rpm to
stabilize system.
3. Observe the refrigerant through the sight
glass of the receiver-dehydrator with the system
operating, to see if there are any bubbles evident.
a. If no bubbles are evident, then bleed system
slowly through the discharge valve until bubbles
appear in the receiver-dehydrator right glass. Add
one pound of refrigerant as explained under "Charg
ing The System."
b. If bubbles are visible in the receiver-de
hydrator sight glass with the " T E M P " control knob
at the full cold position and the blower at high
speed, it indicates partial or complete plug in a
line, or a shortage of refrigerant, or both. Cor
rect condition. Add refrigerant as explained below
until the sight glass clears, then add another one
pound of refrigerant.
4. Attach flexible hose from center fitting of
gauge set loosely to refrigerant drum or on dis
posable can valves. Open high and low pressure
valves on the gauge set slightly to purge pressure
gauge lines of air. Tighten fitting of refrigerant
drum or can, when satisfied that all air has been
removed from gauge lines. Close (clockwise) both
hand shut-off valves of gauge set.
5. Partially charge system.
a. Refrigerant-12 Drum Method.
(1) Place pail containing hot water that -does
not have a temperature exceeding 125 F.,
on scales, place refrigerant drum in pan
containing water, note weight, and only
open low pressure valve on gauge set.
(2) Start engine, move "T e m p " control knob to
full cold position, and place blower control
for high speed. Operate engine for ten min
utes at 2000 rpm to stabilize system.
(3) With compressor operating, slowly open
valve on refrigerant drum and allow re
frigerant to flow into system (through man
ifold gauge set) until liquid indicator clears
up and immediately shut off valve at gauge
set or on refrigerant drum. Check weight
of refrigerant drum and pail of water. Then
slowly open valve on gauge set (or refrig
erant drum) and add one more pound of
refrigerant. Note total amount of refriger
ant added.
b. Refrigerant-12 Disposable Can Method (15
oz. per can).
(1) Make sure the outlet valve on the J-6271
Fits-All valve is fully clockwise and at
tach the J-6271 to a "one pound" can of re
frigerant as follows:
Back off the valve
from the top of the retainer, slip the valve
onto the can and turn the valve into the re
tainer until tight. D O N O T accidentally
open outlet valve during this operation as
turning the valve into the retainer punc
tures the top of the can to make it ready
for charging.
(2) Connect center flexible line of gauge set to
the fitting on the valve.
(3) Start engine, place " T E M P ” control knob
to full cold position and blower control for
high speed with "A IR " knob in "O U T S ID E "
position. Operate engine for ten minutes at
2000 rpm to stabilize system.
(4) With compressor operating, slowly open
valve on refrigerant can and allow refrig
erant to flow into system (through manifold
gauge set) until liquid indicator clears up
and immediately shut off valve at gauge set
and on refrigerant can. Check weight of
can and valve assembly and record.
(5) Add an additional one pound of refrigerant
by adding refrigerant from the can just
weighed until can is empty. Attach another
can and add refrigerant until can and valve
assembly weigh the same as recorded.
6. Close valves at refrigerant drum or can.
7. Test for leaks and make operational check
of system as outlined under "Performance Testing."
CHECKING COMPRESSOR OIL LEVEL
AN D ADDIN G OIL
The refrigeration system with the six-cylinder
axial compressor requires 11 fluid ozs. of 525
viscosity oil. After the system has been operated,
oil circulates throughout the system with the re
frigerant. Hence, while the system is running, oil
is leaving the compressor with the high pressure
gas and is returning to the compressor with the
suction gas.
N O T E : The oil level in the compressor should
not be checked as a matter of course, such as is
done to the truck engine crankcase.
Normally, the compressor oil level needs to
be checked only when there is evidence of a major
oil loss such as a broken hose or fitting, a leaking
compressor seal, or collision damage. However,
if low compressor oil level is suspected, a quick
check may be performed as follows:
1. Operate engine at idle with air conditioning
on maximum cooling for approximately ten minutes.
2. Turn off engine and momentarily crack open
oil drain plug on bottom of compressor allowing
a slight amount of oil drain out. Retighten plug.
3. Again, slightly crack open plug. If oil comes
out, the compressor has the required amount of oil.
Содержание 70 1969 Series
Страница 1: ...CHEVROLET HEAVY DUTY TRUCK SHOP MANUAL...
Страница 3: ......
Страница 11: ...LUBRICATION 0 4 CHEVROLET SERIES 70 80 HEAVY DUTY TRUCK SHOP MANUAL...
Страница 27: ......
Страница 119: ......
Страница 361: ......
Страница 371: ......
Страница 403: ...TROUBLE ANALYSIS CHART ENGINE ELECTRICAL 6Y 32 CHEVROLET SERIES 70 80 HEAVY DUTY TRUCK SHOP MANUAL...
Страница 427: ......
Страница 443: ......
Страница 451: ......
Страница 493: ......
Страница 499: ......
Страница 549: ......
Страница 555: ......
Страница 609: ......
Страница 715: ...am...
Страница 745: ......
Страница 807: ...TRANSMISSION AND CLUTCH 7 61 CHEVROLET SERIES 70 80 HEAVY DUTY TRUCK SHOP M AN U AL Kgure 2 Clark 401 Transmission...
Страница 910: ......
Страница 913: ......