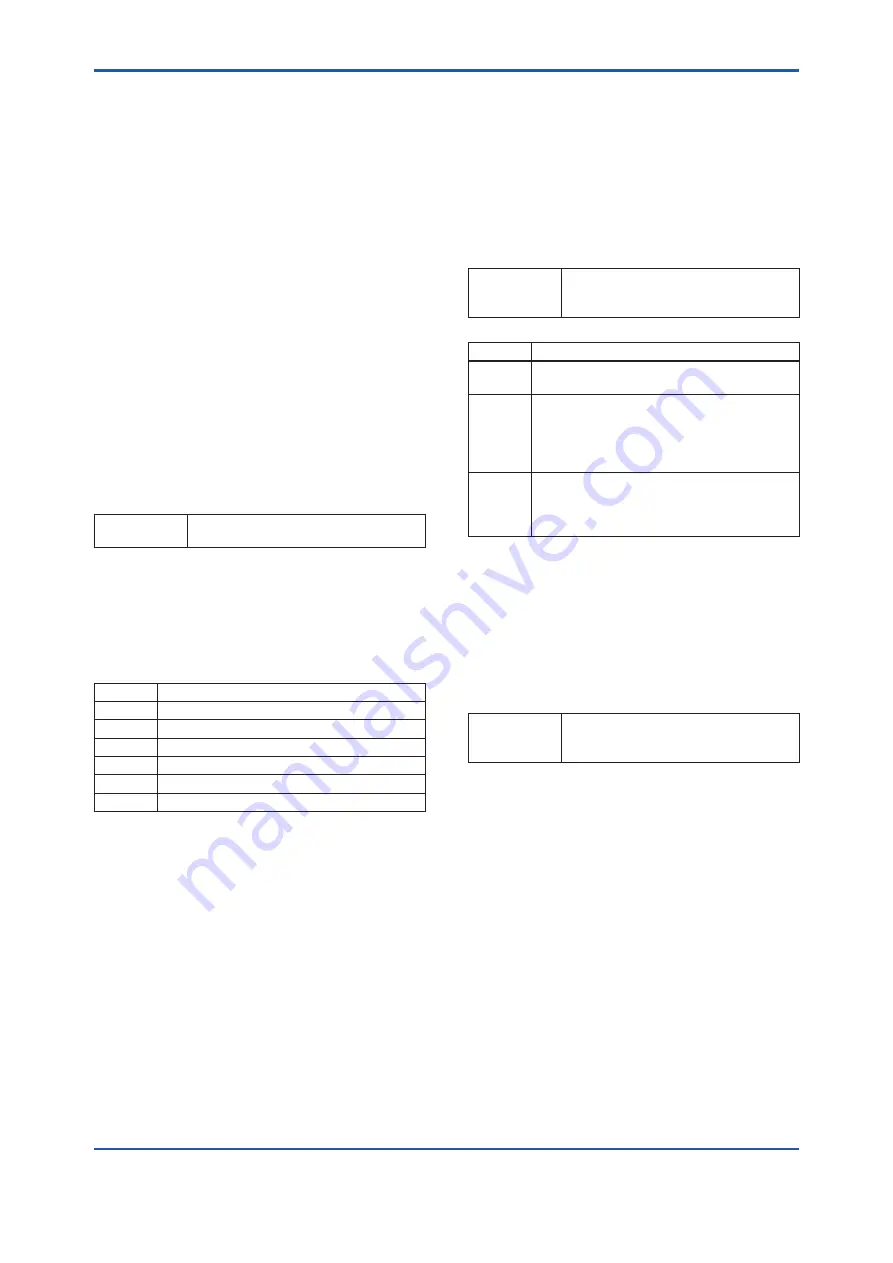
<7. HART Communication>
7-40
IM 01C25W05-01EN
● Invalid Ref BlkF, Pres 1, Pres2, or DP
This alarm indicates that the reference value
acquired under normal process conditions
is invalid. If the Ref BlkF value is invalid as a
reference value, only the blockage detection
that excludes the BlkF detection algorithm is
executed. If you need blockage detection that
uses the BlkF algorithm, reacquire Ref BlkF.
If Ref DPAvg falls below the Lim DPAvgmin
threshold or exceeds the Lim DPAvgmax
threshold, all reference values will be invalid.
If this occurs, alarms for all reference values
(Invalid Ref DP, Invalid Ref Pres 2, Invalid Ref
Pres 1, and Invalid Ref BlkF) will be generated.
■ Alarm masking
● Diag Option
Select which alarms will be reflected in analog
alerts and LCD display using the Diag Option
parameter.
• Recalling the Diag Option parameter
Recall
parameters
[Root menu] → Diag/Service → Diag
Parameters → Diag Option
Each bit of the Diag Option parameter
corresponds one-to-one to the bits of the Diag
Error parameter.
By factory default, the following alarms are
enabled (hexadecimal notation: 0x08f8).
Bit
Assignment
3
Large Fluct Pres 2
4
Large Fluct Pres 1
5
Pres 2 Side Blocking
6
Pres 1 Side Blocking
7
B Blocking
11
Invalid Ref DP
To reflect alarms in analog alerts and LCD
display, follow the procedure below.
1) Set the Diag Mode parameter to Stop.
2) From the alarms assigned to bits 2 to 14,
select the check boxes of the required
alarms.
■ Analog alert setup
● Diag Out Option
If impulse line blockage error or high-
temperature/low-temperature flange
temperature error occurs, the 4-20 mA analog
output can be shifted according to the specified
settings.
• Recalling the Diag Out Option parameter
Recall
parameters
[Root menu] → Diag/Service → Diag
Parameters → Diag Output → Diag Out
Option
Mode
Function
Off
The PV measurement is held, and alarm
occurrences are not reflected in the output.
Burnout When an alarm occurs, the analog output is
shifted to the value specified in the AO upper
limit parameter or AO lower limit parameter.
The direction in which the output is shifted
depend s on the Burnout switch setting.
Fall back When an alarm occurs, the output is held
at a certain value. The shift value can be
specified using the Diag Fixed Out Val
parameter.
● Diag Fixed Out Val
This is used when the Diag Output Option
parameter is set to Fall back.
When an alarm occurs, the output is held at the
value specified with this parameter. You can
enter the value in the range of 3.8 to 21.6 mA.
• Recalling the Diag Fixed Out Val parameter
Recall
parameters
[Root menu] → Diag/Service → Diag
Parameters → Diag Output → Diag
Fixed Out Val →