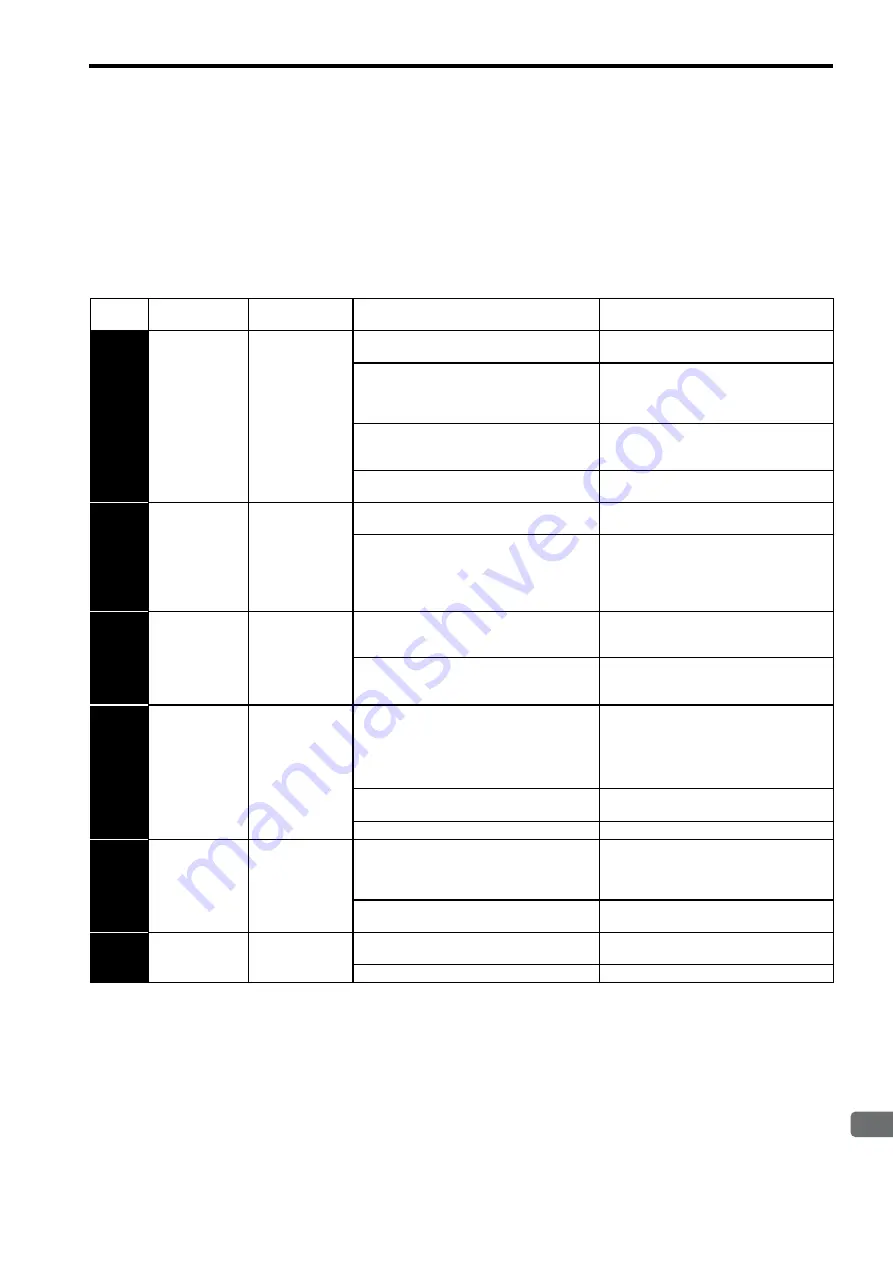
11.1 Troubleshooting
11-5
11
Inspection, Maintenance, and
T
roubleshooting
11.1.3 Troubleshooting of Alarm and Warning
When an error occurs in servo drive, an alarm display such as A.
and CPF
or warning display such as
A.9
appears on the panel operator. However, the display “A.--” is not an alarm. Refer to the following sec-
tions to identify the cause of an alarm and the action to be taken.
Contact your Yaskawa representative if the problem cannot be solved by the described corrective action.
(1) Alarm Display and Troubleshooting
Table 11.3 Alarm Display and Troubleshooting
Alarm
Display
Alarm Name
Situation at Alarm
Occurrence
Cause
Corrective Actions
A.02
Parameter
Breakdown
(The EEPROM
data storing the
parameter is
incorrect.)
Occurred when the
control power sup-
ply was turned ON.
The control power supply ranged from 30 VAC to
60 VAC.
Correct the power supply, and set Fn005 to ini-
tialize the parameter.
The power supply was turned OFF while changing
the parameter setting.
The power supply was turned OFF while an alarm
was being written.
Set Fn005 to initialize the parameter and input
the parameter again.
The number of times that parameters were written
exceeded the limit. For example, the parameter was
changed every scan through the host controller.
Replace the SERVOPACK.
(Recheck the parameter writing method.)
The SERVOPACK EEPROM and the related circuit
are faulty.
Replace the SERVOPACK.
A.03
Main Circuit
Encoder Error
(Not detected for
the SERVO-
PACK with the
capacity of 6.0
kW or more)
Occurred when the
control power sup-
ply was turned ON
or during operation
The control power supply ranged from 30 VAC to
60 VAC.
Correct the power supply.
A SERVOPACK fault occurred.
Replace the SERVOPACK.
A.04
Parameter
Setting Error
(The parameter
setting was out of
the allowable set-
ting range.)
Occurred when the
control power sup-
ply was turned ON.
The incorrect parameter was being loaded. (The
incorrect value was rejected as an error at the digital
operator.)
Set Fn005 to initialize the parameter.
The SERVOPACK EEPROM and the related circuit
are faulty.
Replace the SERVOPACK.
A.05
Combination
Error
(The SERVO-
PACK and servo-
motor capacities
do not corre-
spond.)
Occurred when the
control power sup-
ply was turned ON.
The SERVOPACK and servomotor capacities do
not correspond to each other.
Servomotor capacity / SERVOPACK capacity
≤
1/4
or servomotor capacity / SERVOPACK capacity
≥
4
Select the proper combination of SERVOPACK
and servomotor capacities.
The parameter that is written in the encoder is incor-
rect.
Replace the servomotor (encoder).
A SERVOPACK board fault occurred.
Replace the SERVOPACK.
A.09
Dividing Ratio
Setting Error
Occurred when the
control power sup-
ply was turned ON.
At Pn207.2=1, the setting of dividing ratio (Pn212)
is not acceptable (out of fixed increments), or
exceeds the value for the connected encoder resolu-
tion.
Correct the setting of Pn212, and turn OFF the
control power and turn it ON again.
The SERVOPACK EEPROM and the related circuit
are faulty.
Replace the SERVOPACK.
A.0A
Encoder Model
Unmatched
Occurred when the
control power sup-
ply was turned ON.
The connected serial encoder is not supported by
SGDM SERVOPACK.
Replace the servomotor with SGDM SERVO-
PACK supported model.
A SERVOPACK board fault occurred.
Replace the SERVOPACK.
Summary of Contents for Sigma-II Series
Page 384: ...8 3 8 Operation...