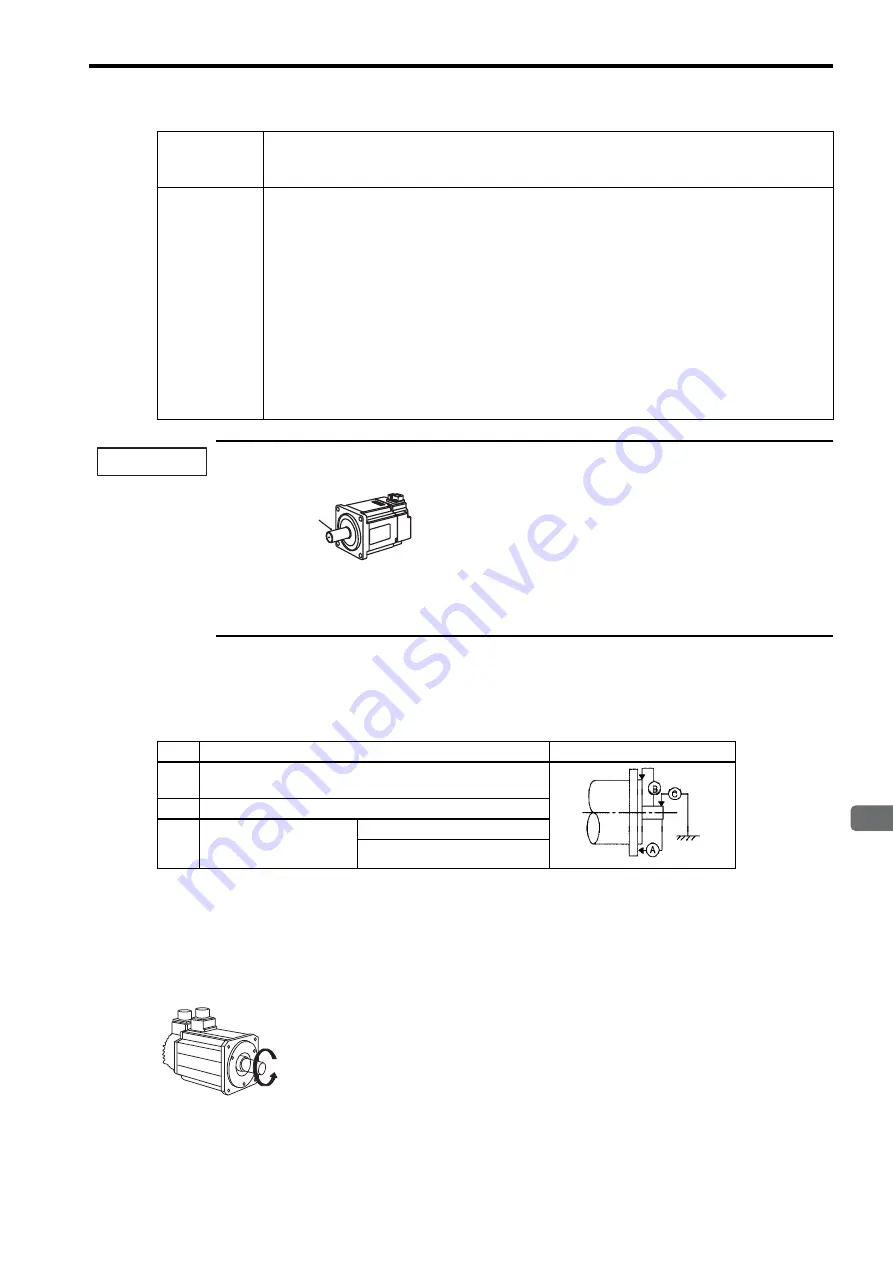
3.8 Mechanical Specifications of SGMAH, SGMPH, SGMGH, SGMSH, and SGMDH Servomotors
3-39
3
Servomotor Specifications and Dimensional Drawings
1. Before starting installation, thoroughly remove the anticorrosive paint that coats the end of the motor
shaft.
2. Vibration from improper alignment of shafts will damage the bearings.
3. Do not allow direct impact to be applied to the shafts when installing the coupling as the encoder
mounted on the opposite end of the shaft may be damaged.
3.8.2 Mechanical Tolerance
The following table shows tolerances for the servomotor’s output shaft and installation area. For more details on
tolerances, refer to the dimensional drawing of the individual servomotor.
* 11 kW and 15 kW SGM
H Servomotors: 0.06 mm
3.8.3 Direction of Servomotor Rotation
Positive rotation of the servomotor is counterclockwise when viewed from the load. (When the servomotor has a
gear, the rotating direction of the gear output shaft will vary depending on the gear type. Check the rotating direc-
tion of your servomotor with dimensional drawings etc..)
Cable Stress
Make sure there are no bends or tension on the power lines.
Especially be careful to wire signal line cables so that they are not subject to stress because the core
wires are very thin at only 0.2 to 0.3 mm.
Connectors
Observe the following precautions:
• Make sure there is no foreign matters such as dust and metal chips in the connector before
connecting.
• When the connectors are connected to the motor, be sure to connect the end of servomotor main
circuit cables before connecting the encoder cable’s end.
If the encoder cable’s end is connected first, the encoder may be damaged because of the voltage
differences between FGs.
• Make sure of the pin arrangement.
• Do not apply shock to resin connectors. Otherwise, they may be damaged.
• When handling a servomotor with its cables connected, hold the servomotor or the connectors.
Otherwise, the cables will be damaged.
• When bending cables are used, wiring must be performed so that excessive stress will not be applied
to the connector section. Failure to observe this caution may damage the connector.
IMPORTANT
Anticorrosive
paint is
coated here.
Tolerance T. I. R. (Total Indicator Reading)
Reference Diagram
A
Perpendicularity between the flange face and output
shaft: 0.04 mm
∗
B
Mating concentricity of the flange O.D.: 0.04
C
Run-out at the end
of the shaft
30 W to 5.0 kW: 0.02 mm
5.5 kW to 15.0 kW: 0.04 mm
Positive direction
Summary of Contents for Sigma-II Series
Page 384: ...8 3 8 Operation...