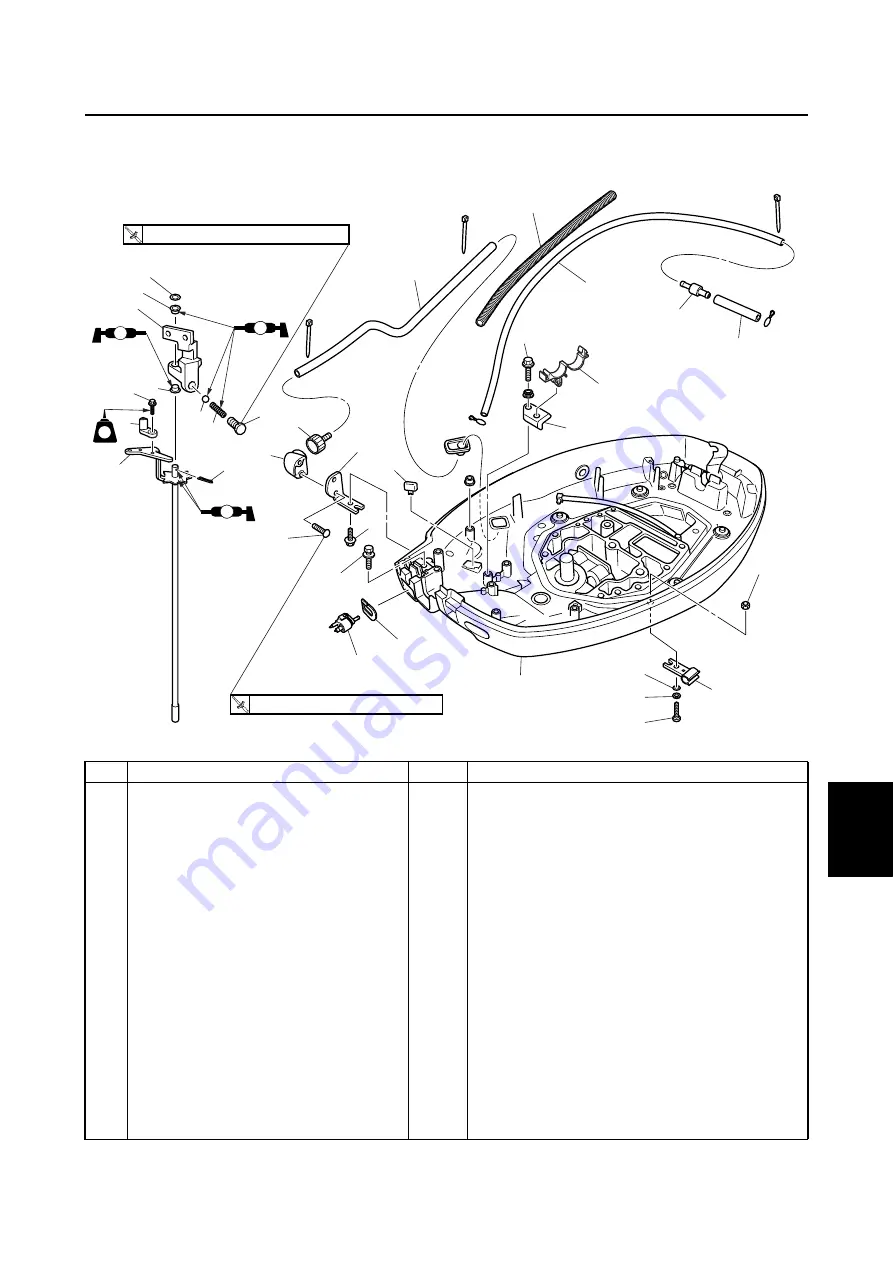
6C13G11
7-10
1
2
3
4
5
6
7
8
9
7
No.
Part name
Q’ty
Remarks
18
Bolt
1
M6
×
25 mm
19
Fuel joint
1
20
Seal
1
21
Bottom cowling assembly
1
22
Bolt
1
M6
×
20 mm
23
Holder
1
24
Washer
1
25
Washer
1
26
Holder
1
27
Nut
1
28
Fuel hose
1
29
Joint
1
30
Fuel hose
1
31
Corrugated tube
1
32
Holder
1
33
Bracket
1
34
Bolt
1
M6
×
15 mm
S6C17060
T
R
.
.
2 N
·
m (0.2 kgf
·
m, 1.5 ft
·
Ib)
A
A
A
A
1
2
3
4
5
7
A
A
6
8
9
10
11
12
13
14
16
15
17
18
19
20
21
22
24
25
23
27
33
32
34
31
30
29
28
26
T
R
.
.
18 N
·
m (1.8 kgf
·
m, 13.3 ft
·
Ib)
LT
242
Summary of Contents for F50F
Page 1: ...F50F FT50G F60C FT60D SERVICE MANUAL 6C1 28197 3G 11 290551 ...
Page 4: ......
Page 48: ...SPEC Specifications 2 25 6C13G11 MEMO ...
Page 190: ...LOWR Lower unit 6 47 6C13G11 Shimming FT50 FT60 6 ...
Page 195: ...6C13G11 6 52 1 2 3 4 5 6 7 8 9 MEMO Backlash FT50 FT60 ...
Page 221: ...6C13G11 7 24 1 2 3 4 5 6 7 8 9 Steering arm ...
Page 249: ...6C13G11 7 52 1 2 3 4 5 6 7 8 9 MEMO Power trim and tilt electrical system ...
Page 272: ...ELEC Electrical systems 8 21 6C13G11 MEMO ...
Page 301: ...6C13G11 i 5 1 2 3 4 5 6 7 8 9 Index MEMO ...
Page 303: ......
Page 304: ...YAMAHA MOTOR CO LTD Printed in the Netherlands Jul 2004 1 2 1 CR E_2 ...