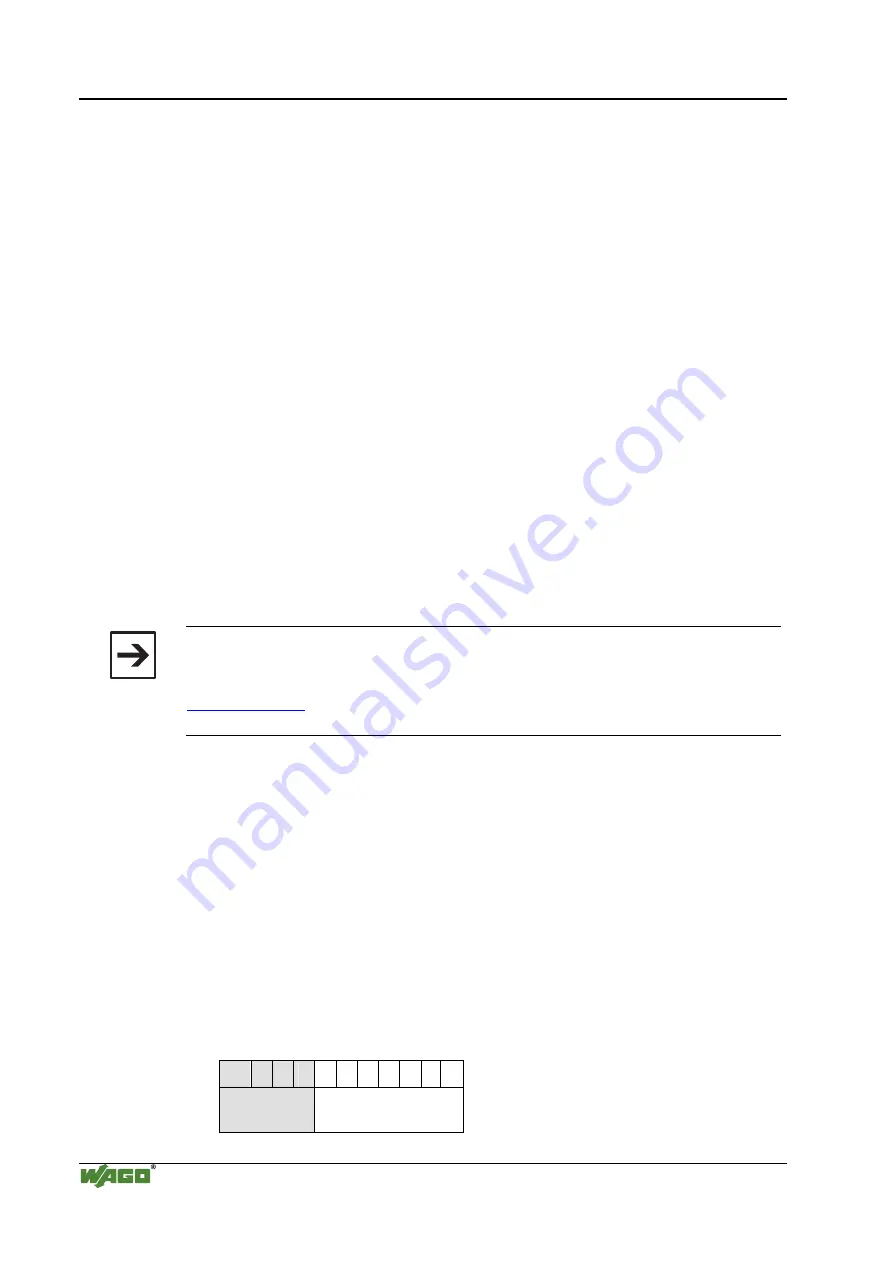
82 • CANopen
Network
Communication
WAGO-I/O-SYSTEM
750
CANopen
4.2.4 Interface Modules
In a network, all WAGO CANopen fieldbus nodes operate as slaves. The mas-
ter operation is taken over by a central control system, such as PLC, NC or
RC. The connection to fieldbus devices is made via interface modules
Interface modules for programmable logic controls (PLCs) and PC interface
PCBs for CANopen are offered by various manufacturers.
4.2.5 Configuration Software
Before a PLC can communicate I/O data with a fieldbus device, the fieldbus
controller board has to be configured for each field bus device on the network.
The software for configuring and diagnosing fieldbus networks is delivered
with the Interface modules for programmable logic controls (PLCs) or PC in-
terface PCBs for CANopen or it is contained in the used CAN Master-
Software (e. g. SyCon of the company Firma Hilscher GmbH).
The needed data to the WAGO CANopen couplers and controllers are made
available with the merging of the EDS files (Electrical Data Sheet) in the con-
figuration software.
Note
EDS and Symbol files for the configuration of I/O modules are available for free
download on the INTERNET Site:
/ Service / Downloads / Software / ELECTRONICC / EDS files
for CANopen.
4.3 Network Communication
With CANopen, data transmission, the triggering of events, signalling of error
states etc. takes place by means of communication objects. For this purpose,
each communication object is assigned a clear COB-ID (Communication Ob-
ject Identifier) in the network.
The COB ID assignment according to the Device profile DS401 results in ac-
cordance with the following table.
10 9
8 7 6 5 4
3
2 1
0
Function
code
node identifier
(0[= all], 1-127)