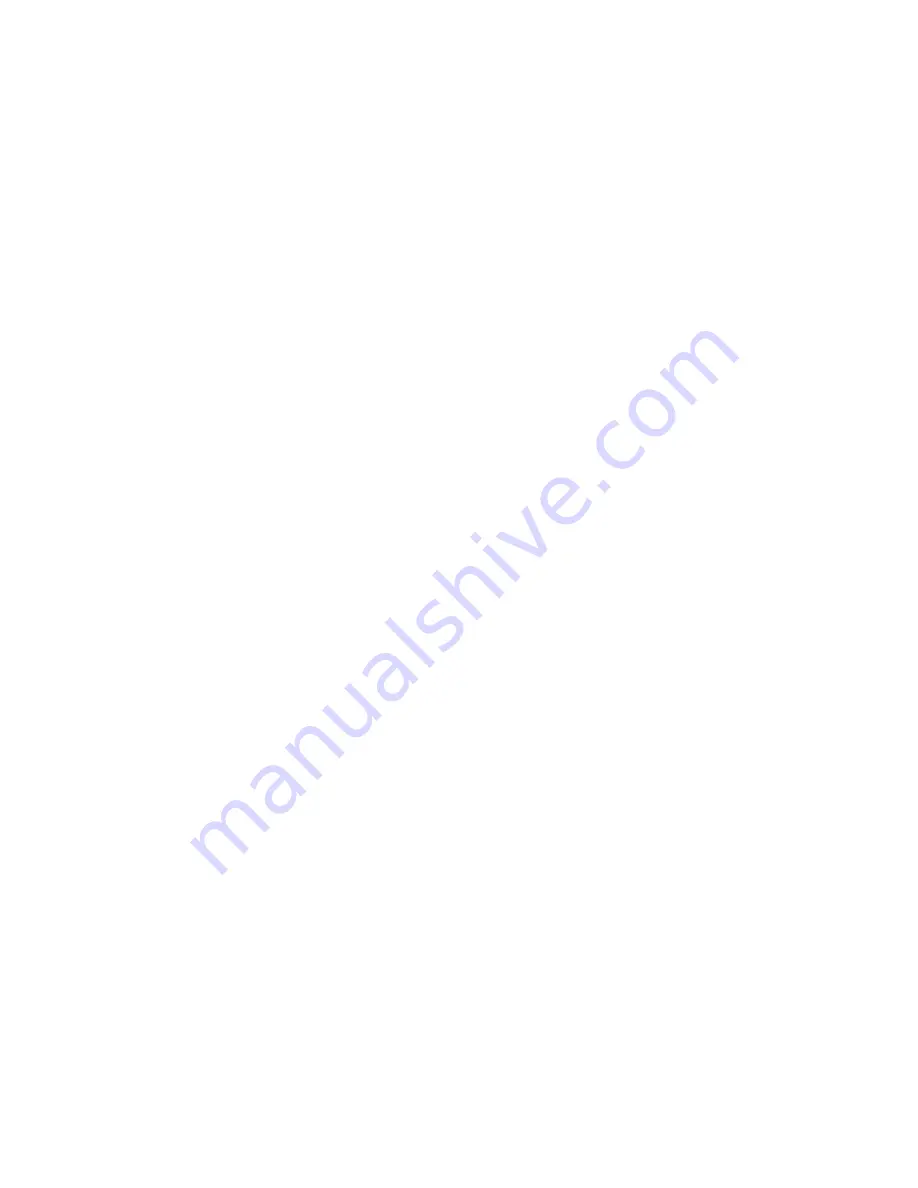
205
A
PPLICATION
L
IQU
ID
R
ATE
C
ONTROL
• Coverage Option
Based on the coverage option selected, this setting determines the behavior of the swath section when
entering/exiting an already applied area or field boundary. Options available include: Minimize Skip,
Minimize Overlap, and User Defined Percentage.
Auxiliary Input Settings
• Master Switch
Switch that performs global master control of all rate control channels.
• F1-F11
Settings determine the switch(es) that will operate the controlling channel specified from the configuration
setup. Single switches can be used to control multiple channels and swath sections.
Controller Settings
• Flow Meter Cal
Calibration value representing the number of pulses that equal one-gallon of product flow through the
controlling system.
• Control Valve Configuration
Setting specifies the type of control valve being used for the rate control functions of the controlling system.
• Response Threshold
Determines where the control channel switches between using Valve Response 1 and Valve Response 2
speed setting.
• Valve Response 1
Determines the speed of the servo valve when product control error exceeds the Response Threshold
setting. Valve Response 1 represents the fast speed of the servo valve.
• Valve Response 2
Determines the speed of the servo valve when product control error is less than the Response Threshold
setting. Valve Response 2 represents the slow speed of the servo valve.
• Allowable Error
Determines the percent of error that is allowed prior to the product control system making any flow rate
changes.
• Flow Control Delay
Setting for period of time from master switch on and the start of product application to the first flow control
correction. This setting can be used to eliminate unwanted correction of flow control at the start of each
pass. Typical setting values are zero for granular and 1 –2 seconds for liquid application control.
• Close Flow Control Valve When Rate Off
When selected the controlling system will shut down when there is either a zero rate in the field or entering
an already applied area. When unchecked the controlling system will stay in the last known state when the
sections are shut off.
• PWM Frequency
The frequency that the PWM control valve is pulsed at. Settings can be found from the manufacturer of the
valve. Typical settings range from 100-125 Hz.
• PWM Gain
Determines how aggressively the control valve responds when making rate change adjustments. The
higher the value the more aggressive the system response is.
Summary of Contents for ag leader
Page 1: ...Operators Manual Firmware Version 5 4 Ag Leader PN 4002722 Rev G ...
Page 2: ...Firmware Version 5 4 ...
Page 20: ...6 Firmware Version 5 4 ...
Page 38: ...24 Firmware Version 5 4 For more information see Legend Settings on page 52 ...
Page 55: ...41 SETUP M ANAGEMENT S ETUP Remove button Press to remove a business ...
Page 56: ...42 Firmware Version 5 4 ...
Page 78: ...64 Firmware Version 5 4 ...
Page 82: ...68 Firmware Version 5 4 Press to Export All Log files Export All Log Files ...
Page 84: ...70 Firmware Version 5 4 ...
Page 94: ...80 Firmware Version 5 4 ...
Page 108: ...94 Firmware Version 5 4 ...
Page 140: ...126 Firmware Version 5 4 ...
Page 154: ...140 Firmware Version 5 4 ...
Page 158: ...144 Firmware Version 5 4 ...
Page 162: ...148 Firmware Version 5 4 ...
Page 222: ...208 Firmware Version 5 4 ...
Page 244: ...230 Firmware Version 5 4 ...
Page 260: ...246 Firmware Version 5 4 ...
Page 290: ...276 Firmware Version 5 4 ...
Page 304: ...290 Firmware Version 5 4 ...