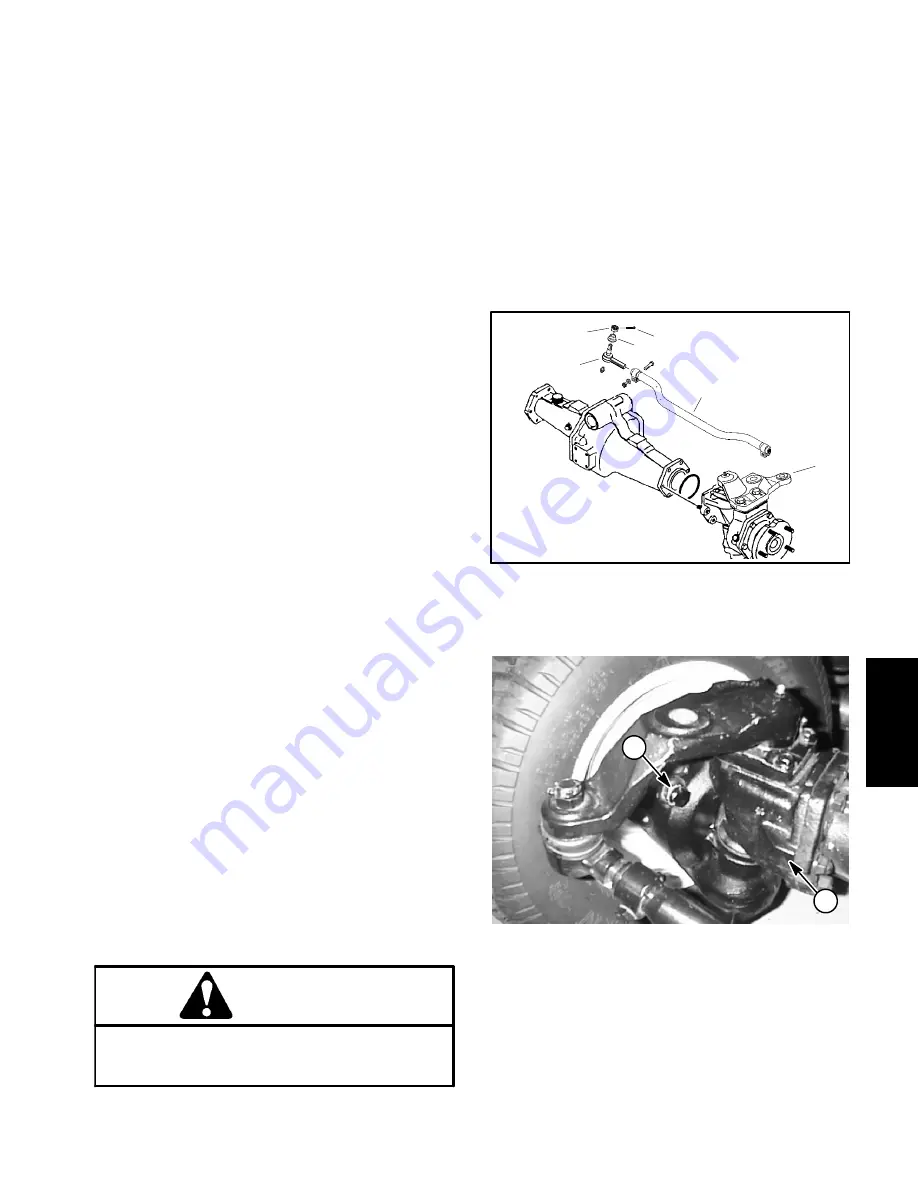
Reelmaster 7000
Page 6 -- 15
Axles, Planetaries and Brakes
7. Remove hydraulic hose from hydraulic fitting on side
of input gear case.
8. Remove lock nut and flat washer from axle pivot pin.
9. Support rear axle to prevent it from falling. Remove
pivot pin. Lower rear axle from machine. Note location
of thrust washer on both ends of axle mounting boss.
10.If needed for further axle disassembly, remove steer-
ing cylinder from axle (see Steering Cylinder in Service
and Repairs section of Chapter 4 -- Hydraulic System).
11.If required, remove tie rod ends from steering arms
on rear axle (Fig. 10). Remove the cotter pins and castle
nuts from the tie rod ball joints. Use a ball joint fork and
remove the tie rod ends from the axle steering arms.
12.Clean the rear axle pivot pin and pivot bushings. In-
spect the pin and bushings for wear or damage. Replace
components as necessary.
Install Rear Axle (Fig. 9)
1. If removed, install steering cylinder to axle assembly
(see Steering Cylinder in Service and Repairs section of
Chapter 4 -- Hydraulic System).
2. If removed, install the tie rod to rear axle (Fig. 10).
Tighten ball joint castle nuts and install new cotter pins.
3. Support axle under machine with a jack. Position
axle assembly to rear frame mount.
4. Install axle pivot pin to secure axle to frame. Make
sure to install thrust washer between axle pivot and
frame on both ends of the pivot. With washers installed,
there should be from 0.002 to 0.020 inch (0.05 to 0.51
mm) clearance between rear frame mount and axle
mounting boss. Add thrust washers if needed to adjust
clearance.
5. Install flat washer and lock nut onto axle pivot pin.
Lock nut should be tightened enough to allow pivot pin
to rotate (
70 ft--lb (94 N--m) maximum
).
6. Install hydraulic motor to axle assembly (see Rear
Axle Motor in Service and Repairs section of Chapter 4
-- Hydraulic System).
7. Install hydraulic hoses to steering cylinder and input
gear case.
Failure to maintain proper wheel lug nut torque
could result in failure or loss of wheel and may
result in personal injury.
WARNING
8. Install wheels to axle. Lower machine to ground.
Torque wheel lug nuts from
85 to 100 ft--lb (116 to 135
N--m)
.
9. Fill axle with SAE 85W--140 weight gear lube.
10.Check rear wheel toe--in and adjust if necessary (see
Traction Unit Operator’s Manual).
11.Check steering stop bolt adjustment. When the
steering cylinder is fully contracted (left turn), a gap of
1/16” (1.6 mm) should exist between bevel gear case
casting and stop bolt on left axle case. Figure 11 shows
stop bolt location.
1. Tie rod
2. Dust cover
3. Cotter pin
4. Castle nut
5. Tie rod end
6. Steering arm (LH)
Figure 10
1
2
3
5
4
6
1. Steering stop bolt
2. Bevel gear case (LH)
Figure 11
2
1
Axles,
Plan
etaries
an
d
B
rakes
Summary of Contents for Reelmaster 7000
Page 2: ...Reelmaster 7000 This page is intentionally blank ...
Page 4: ...Reelmaster 7000 This page is intentionally blank ...
Page 10: ...Reelmaster 7000 Page 1 6 Safety This page is intentionally blank ...
Page 12: ...0 09375 Reelmaster 7000 Page 2 2 Product Records and Maintenance Equivalents and Conversions ...
Page 34: ...Reelmaster 7000 Page 3 18 Kubota Diesel Engine This page is intentionally blank ...
Page 36: ...Reelmaster 7000 Hydraulic System Page 4 2 This page is intentionally blank ...
Page 45: ...Reelmaster 7000 Hydraulic System Page 4 11 This page is intentionally blank Hydraulic System ...
Page 115: ...Reelmaster 7000 Hydraulic System Page 4 81 This page is intentionally blank Hydraulic System ...
Page 131: ...Reelmaster 7000 Hydraulic System Page 4 97 This page is intentionally blank Hydraulic System ...
Page 139: ...Reelmaster 7000 Hydraulic System Page 4 105 This page is intentionally blank Hydraulic System ...
Page 147: ...Reelmaster 7000 Hydraulic System Page 4 113 This page is intentionally blank Hydraulic System ...
Page 151: ...Reelmaster 7000 Hydraulic System Page 4 117 This page is intentionally blank Hydraulic System ...
Page 168: ...Reelmaster 7000 Hydraulic System Page 4 134 This page is intentionally blank ...
Page 214: ...Reelmaster 7000 Page 5 46 Electrical System This page is intentionally blank ...
Page 247: ...Reelmaster 7000 Page 7 3 Chassis This page is intentionally blank Chassis ...
Page 264: ...Reelmaster 7000 Page 7 20 Chassis This page is intentionally blank ...
Page 271: ...Reelmaster 7000 DPA Cutting Units Page 8 7 This page is intentionally blank DPA Cutting Units ...
Page 304: ...Reelmaster 7000 DPA Cutting Units Page 8 40 This page is intentionally blank ...
Page 306: ...Reelmaster 7000 Foldout Drawings Page 9 2 This page is intentionally blank ...
Page 310: ...Page 9 6 Reelmaster 7000 Main Wire Harness ...
Page 312: ...Page 9 8 Reelmaster 7000 Seat and Console Wire Harness ...
Page 314: ...Page 9 10 Reelmaster 7000 Power Center Wire Harness ...