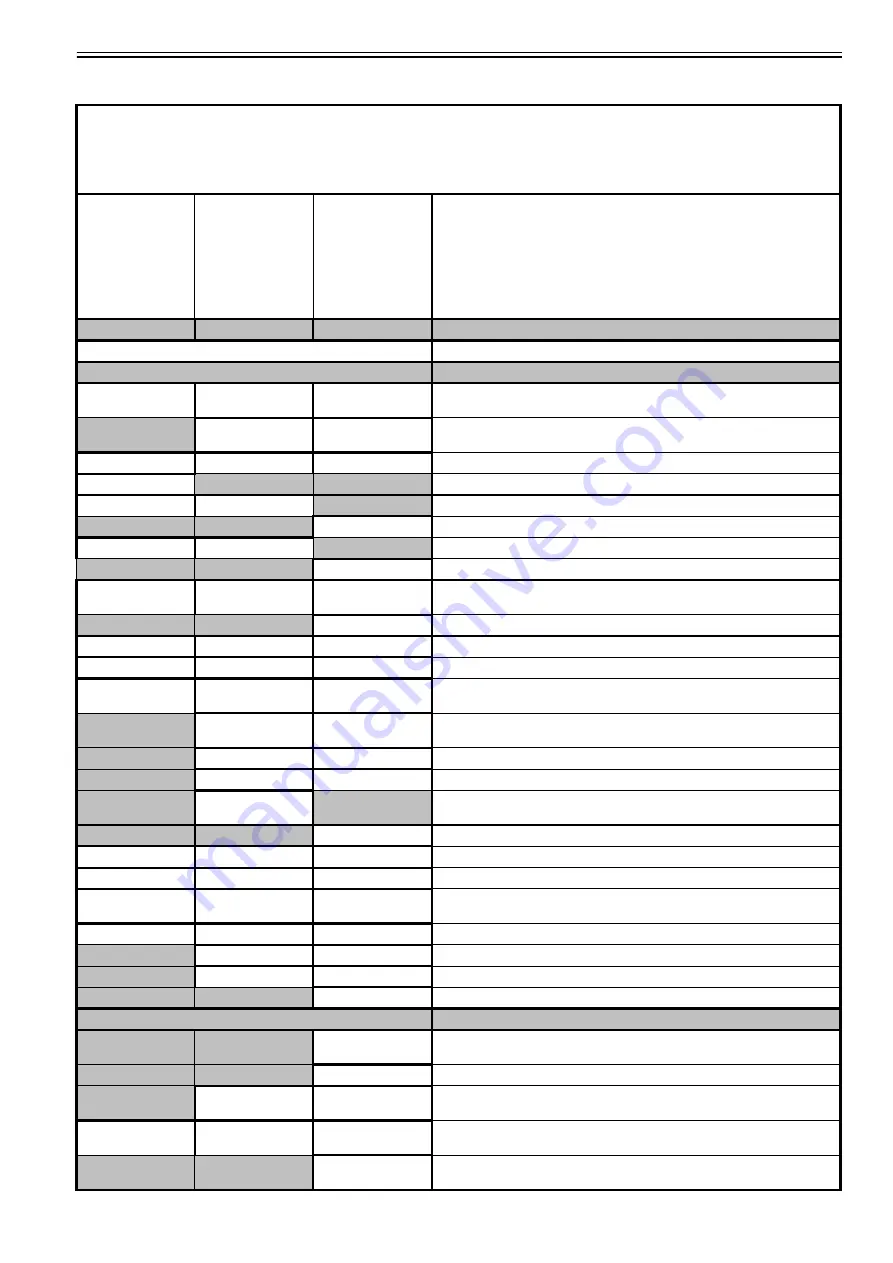
Maintenance Inspection Schedule
4-5
UNIT MODELS: T-500R
The service technician is responsible for assessing the condition
of all parts & components found during any service operation to
be in a condition suitable for further operation up to the next
scheduled service. If parts not considered in suitable condition
they should be replaced.
INSPECTION
A SERVICE
Every 500 hours
Or every 6
Months
(whichever comes
first)
SERVICE
B SERVICE
Every 1000 hours
Or every 12
Months
(whichever comes
first)
SERVICE
C SERVICE
Every 2000 hours
Or every 24
Months
(whichever comes
first)
Check/Inspect/Adjust/Change/Replace
1.0 hr
2.5 hrs
5.5 hrs
EDAC Labour standard
Engine & Unit Mechanical Items
Download Remote Watch maintenance logger - Check alarm codes
& take corrective action as required
Check HMI & Controller software revision - InstalI latest revision if
customer approved or approved by Thermo King for upgrade.
Check fuel supply.
Check engine oil level.
Check engine coolant level.
Check & maintain coolant antifreeze at -35'C
Inspect compressor, fan drive & water pump belts for condition
Replace all belts every 4000hrs or every 48 months
Inspect all belt tension devises & belt idler pulley for condition &
correct operation
Check water pump seal for weep age and bearing serviceability.
Perform Automatic Pre-Trip
Listen for unusual noises, vibrations, etc.
Visually inspect exhaust system for leakage and abnormal smoke or
particulate emissions.
Check engine oil pressure hot, on high speed - Minimum 276 kPa,
2.76 bar, 40 psi.
Check & adjust engine speeds (high and low speed).
Change engine oil (hot) and oil filter
Inspect cyclonic air filter element - Dependent on operating condi-
tions, assess fitness to continue to next service.
Change air filter every 4000 hrs or 48 months
Check air cleaner hose for security & damage.
Drain fuel tank condensate water and assess fuel cleanliness
Check fuel tank fixings, fuel filler cap security, pipe fittings & air
vent.
* Check/Clean/Replace external fuel pre-filter if fitted.
Inspect & clean fuel transfer pump inlet strainer
Replace unit fuel filter
Check condition of engine vibration mounts.
Electrical
Check alternator charge rate regulation voltage, maximum amper-
age output and pre-heater amp draw.
Inspect alternator bearings
Check defrost initiation and termination. Check evaporator fans
function during defrost (fans should be stopped during defrost)
**Inspect battery terminals, and electrolyte level. ***If EON bat-
tery only inspect terminals
Remove clean and protect battery terminals.
Wet cell batteries, check electrolyte specific gravity
Summary of Contents for T-1000R
Page 14: ...Safety Precautions 2 6 Warning Decals 2e24151g0 ...
Page 34: ...Maintenance Inspection Schedule 4 10 ...
Page 57: ...Unit Description 5 23 Purge Mode UT Series 1 3 4 5 2 ...
Page 67: ...Unit Description 5 33 Zone 1 Cool and Zone 2 Cool UT SPECTRUM Units ...
Page 69: ...Unit Description 5 35 Purge Mode UT SPECTRUM Units ...
Page 71: ...Unit Description 5 37 Zone 1 Cool and Zone 2 Heat UT SPECTRUM Units ...
Page 72: ...Unit Description 5 38 ...
Page 74: ...Diesel Electric Menu 6 28 Adjust Brightness 6 29 Time 6 30 ...
Page 120: ...Operating Instructions Standard HMI 7 18 ...
Page 152: ...Engine Maintenance 9 14 T Series Fuel and Oil System Components TK 376 ...
Page 154: ...Engine Maintenance 9 16 T Series Fuel and Oil System Components TK 270 ...
Page 156: ...Engine Maintenance 9 18 UT Series Fuel System Components AMA768 ...
Page 172: ...Engine Maintenance 9 34 T Series Engine Mounting Components for 2 Cylinder Engine ...
Page 184: ...Engine Maintenance 9 46 ...
Page 238: ...Refrigeration Maintenance 10 54 ...
Page 246: ...Clutch Maintenance 11 8 ...
Page 258: ...Structural Maintenance 12 12 ...
Page 264: ...Mechanical Diagnosis 13 6 ...
Page 265: ...14 Electric Standby Diagnosis ...
Page 268: ...Electric Standby Diagnosis 14 4 ...
Page 269: ...15 Refrigeration System Diagnosis ...
Page 272: ...Refrigeration System Diagnosis 15 4 ...
Page 280: ...Remote Evaporators 16 8 ...