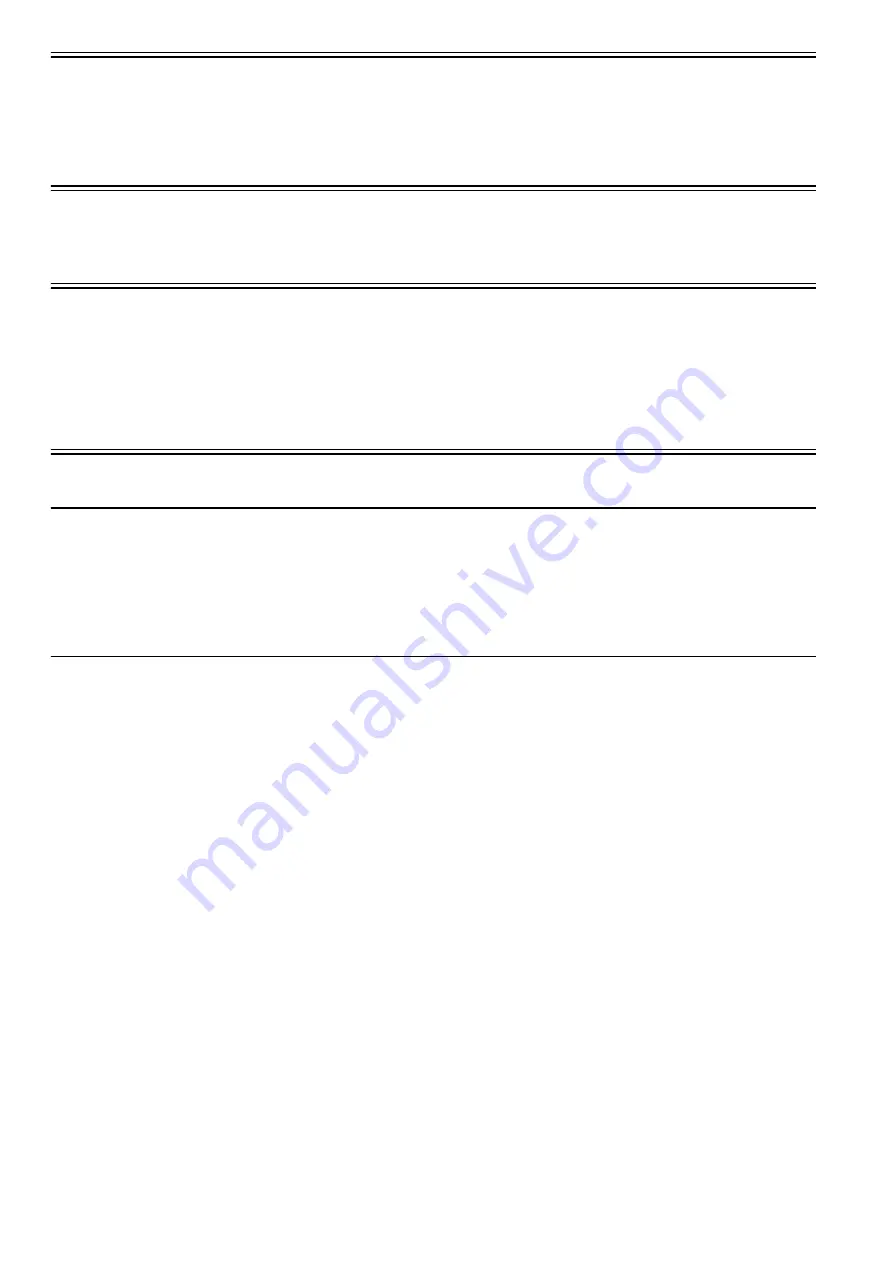
Structural Maintenance
12-2
UNIT AND ENGINE MOUNTING BOLTS
Periodically check and tighten all unit and engine mounting bolts.
T-Series:
Torque the unit mounting bolts to 60 fT-lb (81 N•m). Torque the engine mounting bolts to 64 fT-lb (87 N•m).
UT-Series:
Torque the condenser section mounting bolts to 130-170 fT-lb (176-230 N•m). Torque the evaporating mounting
bolts to 60 fT-lb (81 N•m). Torque the engine mounting bolts to 50 fT-lb (68 N•m).
UNIT INSPECTION
Inspect the unit during unit pretrip inspection and scheduled maintenance inspections for loose or broken wires or hardware,
compressor oil leaks, or other physical damage which might affect unit performance and require repair or replacement of parts.
CONDENSER, EVAPORATOR AND RADIATOR COILS
Clean the coils during scheduled maintenance inspections. Remove any debris (e.g., leaves or plastic wrap) that reduces the
air flow. Clean dirty coils with compressed air or a pressure washer. Be careful not to bend the fins when cleaning a coil. If
possible, blow the air or water through the coil in the direction opposite the normal air flow. Repair bent fins and any other
noticeable damage.
MICRO-CHANNEL COIL CLEANING RECOMMENDATIONS
Cleaning Intervals
• The coils should be cleaned a Minimum of once a year.
• It is recommended that any time the unit is in for service or maintenance that the coils be inspected and cleaned if needed.
• The coil should be cleaned if there are visible accumulations that obstruct the view of the fins or tubes of the coil.
• The coils should be cleaned if there is debris imbedded in the tubes and fins
The area and conditions in which the unit operates will dictate the cleaning intervals and method(s) needed.
Cleaning Methods (listed in order of recommended method)
• Take a cloth or towel and wipe the air side of the coil going with the fins, across the tubes. (Results shown in Figure .) The
coil will clean in a manner similar to the way lint cleans from the lint trap of a household clothes dryer.
• Use a soft bristled brush (DO NOT USE A WIRE BRUSH) and brush the coil going with the fins, across the tubes. The coil
will clean in a manner similar to the way lint cleans from the lint trap of a household clothes dryer.
• A vacuum with a soft attachment can be used to suck the debris off the face as well as in the fins and tubes from the air side
of the coil.
• Compressed air can be used and will work best when blown thru the coil from the non-air side when possible. Blowing thru
from the airside may imbed debris in the coil that was only on the surface. It is recommended to start with one of the first
three options before using compressed air if the non-air side is not accessible. The angle at which the air should be directed
at the coil should not be less than 75 degrees (see Figure ).
• Power water sprayer may be used in pressures under 600 psi. Water will work best when blown thru the coil from the non-air
side when possible. Spraying thru from the airside may imbed debris in the coil that was only on the surface. It is
recommended to start with one of the first three options before using water if the non-air side is not accessible. The angle at
which the water should be directed at the coil should not be less than 75 degrees (see Figure ).
NOTE:Chemicals to aid in cleaning WILL VOID WARRANTY and are NOT RECOMMENDED.
In some instances in may take a combination of two methods to result in a clean coil. Such as, first wiping the coil to clean the
surface and then using a vacuum, water or compressed air to clean down in the fins. This will depend on the type of debris that
needs to be cleaned from the coil.
Be sure not to contact the coil with any hard vacuum nozzle, air nozzle, or any other tool. This will damage the tubes of the coil.
CAUTION: Air pressure should not be high enough to damage coil fins.
Summary of Contents for T-1000R
Page 14: ...Safety Precautions 2 6 Warning Decals 2e24151g0 ...
Page 34: ...Maintenance Inspection Schedule 4 10 ...
Page 57: ...Unit Description 5 23 Purge Mode UT Series 1 3 4 5 2 ...
Page 67: ...Unit Description 5 33 Zone 1 Cool and Zone 2 Cool UT SPECTRUM Units ...
Page 69: ...Unit Description 5 35 Purge Mode UT SPECTRUM Units ...
Page 71: ...Unit Description 5 37 Zone 1 Cool and Zone 2 Heat UT SPECTRUM Units ...
Page 72: ...Unit Description 5 38 ...
Page 74: ...Diesel Electric Menu 6 28 Adjust Brightness 6 29 Time 6 30 ...
Page 120: ...Operating Instructions Standard HMI 7 18 ...
Page 152: ...Engine Maintenance 9 14 T Series Fuel and Oil System Components TK 376 ...
Page 154: ...Engine Maintenance 9 16 T Series Fuel and Oil System Components TK 270 ...
Page 156: ...Engine Maintenance 9 18 UT Series Fuel System Components AMA768 ...
Page 172: ...Engine Maintenance 9 34 T Series Engine Mounting Components for 2 Cylinder Engine ...
Page 184: ...Engine Maintenance 9 46 ...
Page 238: ...Refrigeration Maintenance 10 54 ...
Page 246: ...Clutch Maintenance 11 8 ...
Page 258: ...Structural Maintenance 12 12 ...
Page 264: ...Mechanical Diagnosis 13 6 ...
Page 265: ...14 Electric Standby Diagnosis ...
Page 268: ...Electric Standby Diagnosis 14 4 ...
Page 269: ...15 Refrigeration System Diagnosis ...
Page 272: ...Refrigeration System Diagnosis 15 4 ...
Page 280: ...Remote Evaporators 16 8 ...