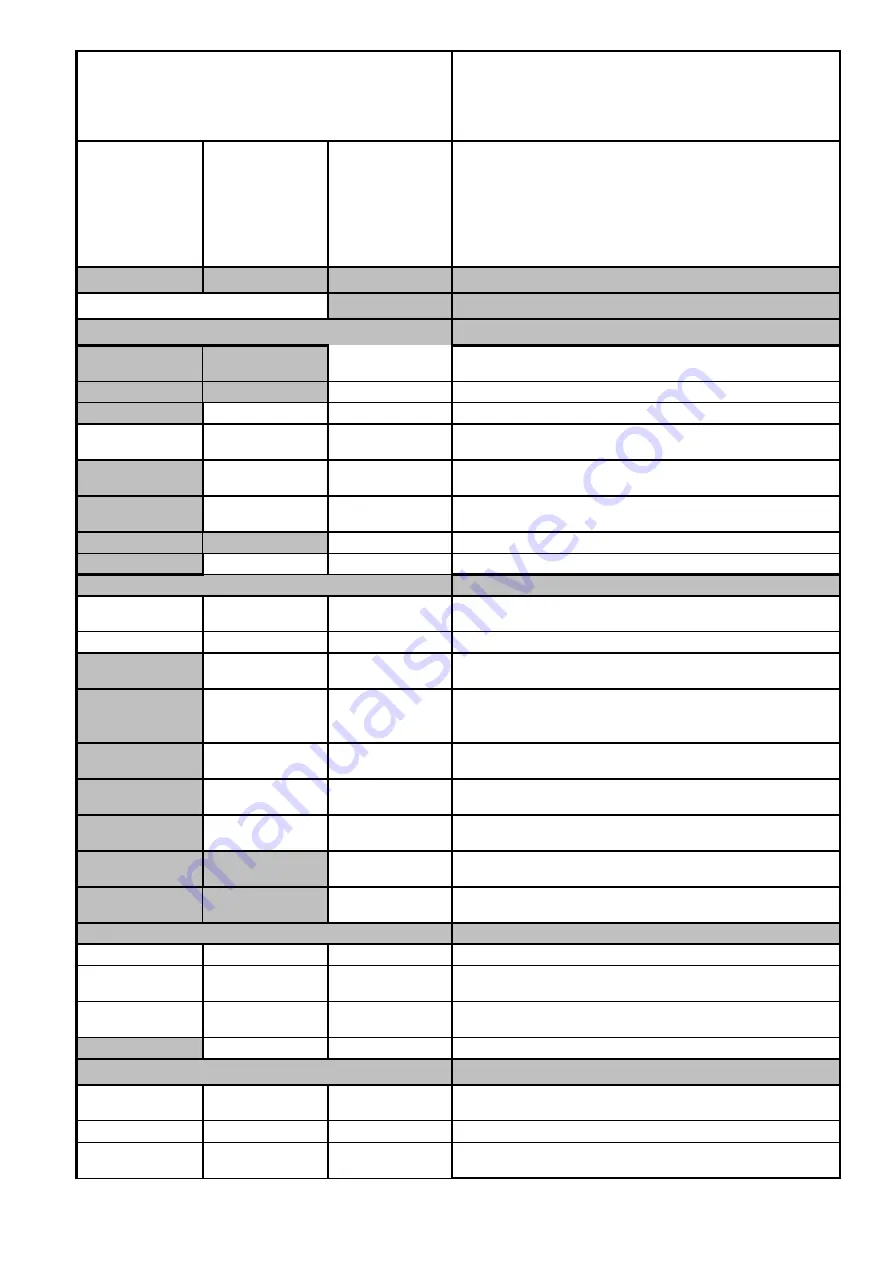
Maintenance Inspection Schedule
4-3
The service technician is responsible for assessing the
condition of all parts & components found during any service
operation to be in a condition suitable for further operation
up to the next scheduled service. If parts not considered in
suitable condition they should be replaced.
INSPECTION
A SERVICE
Every 1000 hours
Or every 6 Months
(whichever comes
first)
SERVICE
B SERVICE
Every 2000 hours
Or every 12
Months
(whichever comes
first)
SERVICE
C SERVICE
Every 4000 hours
Or every 24
Months
(whichever comes
first)
Check/Inspect/Adjust/Change/Replace
1.0 hr
2.5 hrs
3.75 hrs
EDAC Labour standard
5.0 hrs
For 24 months items
Electrical
Check alternator connections for corrosion and clean and protect
as required.
Inspect alternator brushes
Check evaporator damper system for correct operation
**Inspect battery terminals, and electrolyte level. ***If EON
battery only inspect terminals
Check battery fixture. Remove clean and protect battery
terminals. Wet cell batteries, check electrolyte specific gravity
Visually inspect all unit wire harness for damaged wires or
connections. (Pay particular attention to interconnect harnesses)
Check idler and fan shafts and electric motor bearings 24 months
Check operating modes on electric standby.
Refrigeration
Visually inspect condenser/radiator & evaporator coils for
damage & dirt ingress
Check refrigerant level.
Leak test entire unit - or annually or as required for F-Gas control
regulations
Check for correct suction & discharge pressures & when
equipped operation of ETV. (For ETV check use service test
mode)
Check operating pressure on mechanical throttling valve units in
heat cycle with higher than 15'C box temperature
Check compressor oil level and condition.(When returning to
cool from heat cycle above)
Perform full series of pump down internal sealing point tests &
compressor efficiency test.
* Replace refrigeration filter/dehydrator. This should also be
performed whenever system is opened for service
* Replace compressor oil filter when compressor drive belt is
replaced.
Structural & Vehicle Body
Check all doors: operation & hardware security
Visually inspect unit for damaged, loose or broken skins, parts &
fittings (includes air ducts and bulkheads)
Check all unit mounting bolts, external mounted equipment &
wiring, hoses, fuel lines etc.
Clean micro-channel condenser and radiator
Miscellaneous
* Check calibration of return and discharge sensors as per
customers HACCP or annually.
Check operation of all accessories
Check service records and ensure all service and warranty
modifications have been completed. Upgrades not included.
Summary of Contents for T-1000R
Page 14: ...Safety Precautions 2 6 Warning Decals 2e24151g0 ...
Page 34: ...Maintenance Inspection Schedule 4 10 ...
Page 57: ...Unit Description 5 23 Purge Mode UT Series 1 3 4 5 2 ...
Page 67: ...Unit Description 5 33 Zone 1 Cool and Zone 2 Cool UT SPECTRUM Units ...
Page 69: ...Unit Description 5 35 Purge Mode UT SPECTRUM Units ...
Page 71: ...Unit Description 5 37 Zone 1 Cool and Zone 2 Heat UT SPECTRUM Units ...
Page 72: ...Unit Description 5 38 ...
Page 74: ...Diesel Electric Menu 6 28 Adjust Brightness 6 29 Time 6 30 ...
Page 120: ...Operating Instructions Standard HMI 7 18 ...
Page 152: ...Engine Maintenance 9 14 T Series Fuel and Oil System Components TK 376 ...
Page 154: ...Engine Maintenance 9 16 T Series Fuel and Oil System Components TK 270 ...
Page 156: ...Engine Maintenance 9 18 UT Series Fuel System Components AMA768 ...
Page 172: ...Engine Maintenance 9 34 T Series Engine Mounting Components for 2 Cylinder Engine ...
Page 184: ...Engine Maintenance 9 46 ...
Page 238: ...Refrigeration Maintenance 10 54 ...
Page 246: ...Clutch Maintenance 11 8 ...
Page 258: ...Structural Maintenance 12 12 ...
Page 264: ...Mechanical Diagnosis 13 6 ...
Page 265: ...14 Electric Standby Diagnosis ...
Page 268: ...Electric Standby Diagnosis 14 4 ...
Page 269: ...15 Refrigeration System Diagnosis ...
Page 272: ...Refrigeration System Diagnosis 15 4 ...
Page 280: ...Remote Evaporators 16 8 ...