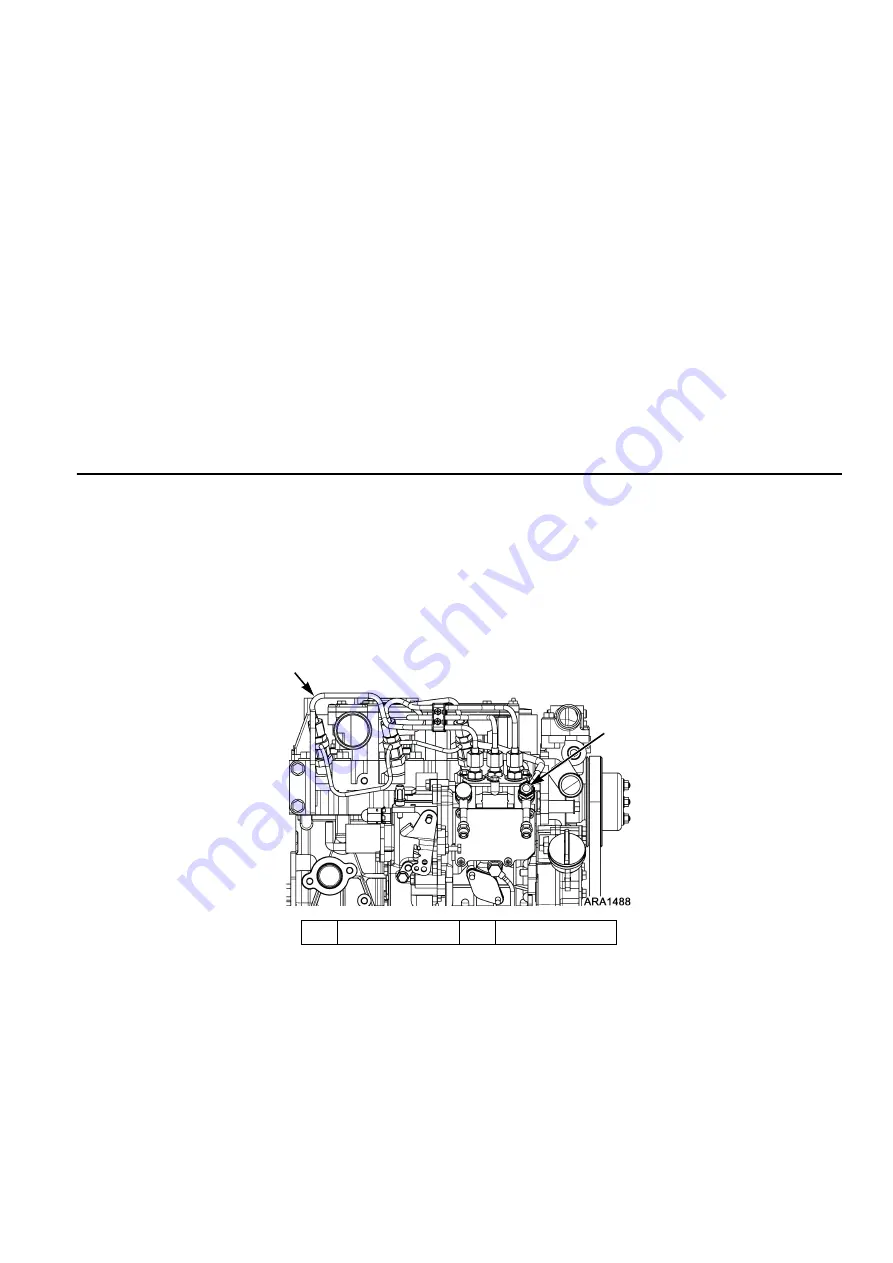
Engine Maintenance
9-13
The most common cause of fuel system problems is contamination. It cannot be stressed enough that the fuel must be clean,
fuel tanks must be free from contaminants, and the fuel filter must be changed regularly. Any time that the fuel system is opened
up, all possible precautions must be taken to keep dirt from entering the system. This means all fuel lines should be capped when
open. The work should be done in a relatively clean area, if possible, and the work should be completed in the shortest time
possible.
The injection nozzles must be tested (and repaired if necessary) at least every 3,000 hours in accordance with EPA 40 CFR
Part 89. Normal conditions are considered to be the use of clean high quality fuel, no used oil blending, and regular
maintenance of the fuel system according to the Maintenance Inspection Schedule. Refer to the TK270, TK370, and TK376
Overhaul Manual TK 53163 for injection nozzle testing and repair procedures.
Thermo King recommends that any major injection pump or nozzle repairs be done by a quality diesel injection service
specialty shop. The investment in equipment and facilities to service these components is quite high. Therefore, this equipment
is not found in most repair shops.
The following procedures can be done under field conditions:
• Bleeding air from the fuel system
• Maintenance involving the fuel tank and filter system
• Engine speed adjustments
• Electric transfer pump replacement or repair (10 psig [69 kPa] pump with diesel filter)
• Injection line replacement
• Pump timing
• Nozzle spray pattern testing and adjustment
• Minor rebuilding of nozzles.
Bleeding the Fuel System
The fuel system will have to have the air bled out if the engine runs out of fuel, if repairs are made to the fuel system, or air
gets into the system for any other reason.
MAKE SURE to keep the fuel tank vent open. If the vent becomes clogged, a partial vacuum develops in the tank, and this
increases the tendency for air to enter the system.
Proceed as follows:
1. Loosen the bleeder screw on the return fuel fitting of the injection pump.
2. Turn on the electric fuel pump. The electric fuel pump is energized when the
O
N
key is pushed. Tighten the bleeder screw on
the injection pump when clear flow of fuel appears.
NOTE: At initial starT-up, open the bleeder screw at the injection pump and bleed fuel until a clear
flow is noted.
3. Loosen the injector lines on the injection nozzles.
4. Crank the engine until fuel appears at the nozzles. Tighten the injector lines, and start the engine.
NOTE: Fuel will not appear at the nozzles by merely running the electric pump. The engine must be
cranked.
1.
Injector Line
2.
Bleeder Screw
Injection Pump
2
1
Summary of Contents for T-1000R
Page 14: ...Safety Precautions 2 6 Warning Decals 2e24151g0 ...
Page 34: ...Maintenance Inspection Schedule 4 10 ...
Page 57: ...Unit Description 5 23 Purge Mode UT Series 1 3 4 5 2 ...
Page 67: ...Unit Description 5 33 Zone 1 Cool and Zone 2 Cool UT SPECTRUM Units ...
Page 69: ...Unit Description 5 35 Purge Mode UT SPECTRUM Units ...
Page 71: ...Unit Description 5 37 Zone 1 Cool and Zone 2 Heat UT SPECTRUM Units ...
Page 72: ...Unit Description 5 38 ...
Page 74: ...Diesel Electric Menu 6 28 Adjust Brightness 6 29 Time 6 30 ...
Page 120: ...Operating Instructions Standard HMI 7 18 ...
Page 152: ...Engine Maintenance 9 14 T Series Fuel and Oil System Components TK 376 ...
Page 154: ...Engine Maintenance 9 16 T Series Fuel and Oil System Components TK 270 ...
Page 156: ...Engine Maintenance 9 18 UT Series Fuel System Components AMA768 ...
Page 172: ...Engine Maintenance 9 34 T Series Engine Mounting Components for 2 Cylinder Engine ...
Page 184: ...Engine Maintenance 9 46 ...
Page 238: ...Refrigeration Maintenance 10 54 ...
Page 246: ...Clutch Maintenance 11 8 ...
Page 258: ...Structural Maintenance 12 12 ...
Page 264: ...Mechanical Diagnosis 13 6 ...
Page 265: ...14 Electric Standby Diagnosis ...
Page 268: ...Electric Standby Diagnosis 14 4 ...
Page 269: ...15 Refrigeration System Diagnosis ...
Page 272: ...Refrigeration System Diagnosis 15 4 ...
Page 280: ...Remote Evaporators 16 8 ...