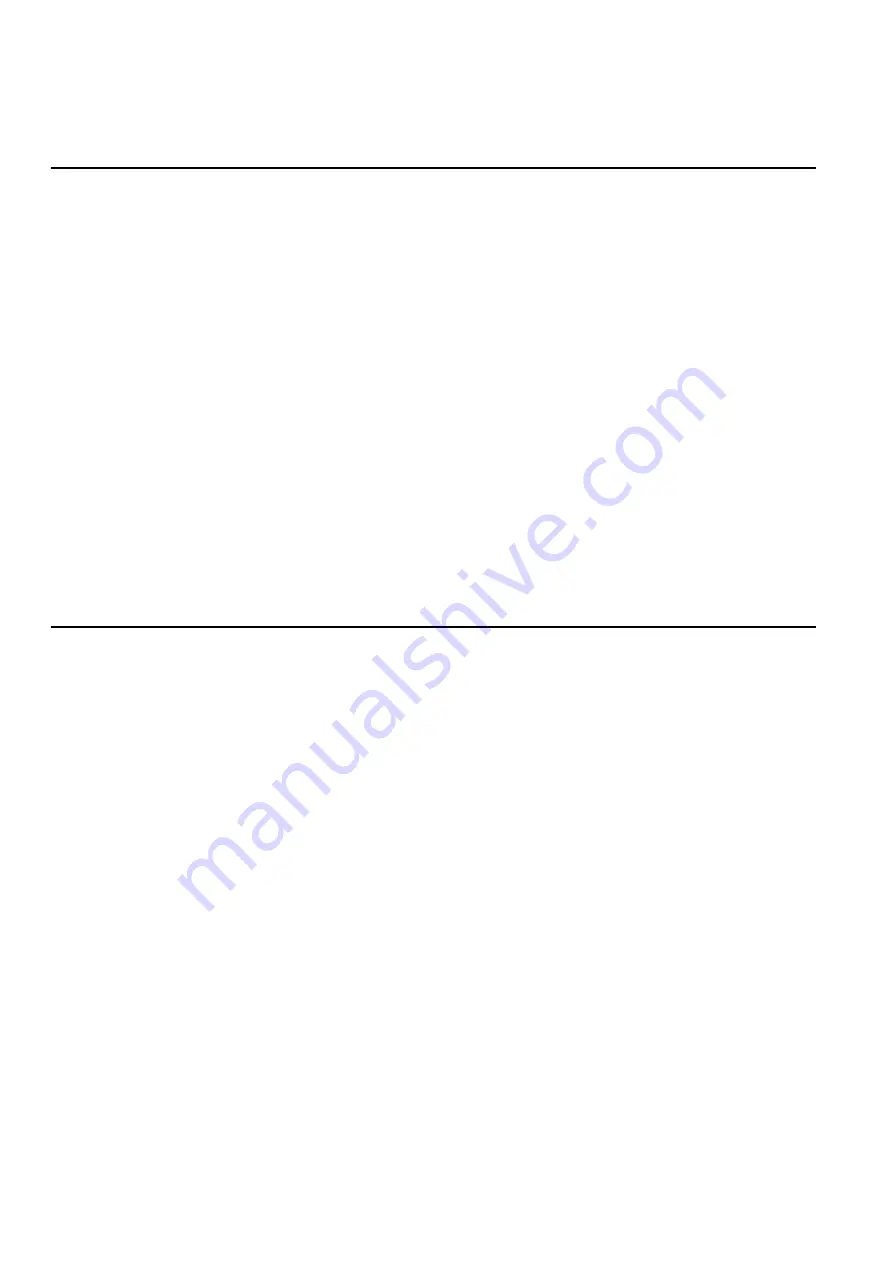
Refrigeration Maintenance
10-28
12. Replace SAE plug in compressor body. Torque mounting screws to 11 to 12.5 Nm.
13. Add compressor oil through the fitting at the oil filter cover. Add the same amount of oil that was removed. If the compressor
oil removed from the compressor was NOT measured and step 1 of the compressor removal procedure was followed to return
as much oil as possible to the compressor, then add 1.2 litres of compressor oil. Use polyol ester oil, P/N 203-433.
14. Install compressor in unit (see compressor installation procedure above).
Scroll Compressor High Temperature Switch Replacement
NOTE: Replace the compressor high temperature switch whenever the insulation on the leads has been broken or the switch
is believed to be defective.
Parts Required
• Temperature Switch Assembly, P/N 41-2467
• Plastic Cap, P/N 22-1040
• Dielectric Compound, P/N 203-501
• Silicone Sealant
To change the switch:
1. Cut through silicone sealant surrounding plastic cap.
2. Pry plastic cap out of compressor end plate.
3. Remove temperature switch assembly by pulling it out of cavity.
4. Clean all debris from end plate and cavity.
5. Insert 0.25 to 0.50 ml of dielectric compound into high temperature switch cavity.
6. Apply 0.25 to 0.50 ml of dielectric compound between the new switch element and sleeve.
7. Fold the sleeve over, fully protecting the switch element.
8. Firmly press the temperature switch assembly into the cavity.
9. Completely fill remaining void in cavity with silicone to protect against water infiltration.
10. With switch wires and slot in cap facing down, press new plastic cap in place on cavity. Protective cap will snap into place
when correctly seated.
Scroll Compressor Liquid Injection Fitting Replacement
Parts Required
• O-ring, P/N 33-2995
• Liquid Injection Fitting, P/N 66-9056
To replace the fitting:
1. Remove the refrigerant charge.
2. Clean dirt from area around fitting.
3. Unsolder injection tube from fitting.
NOTE: Use a heat sink or wrap the injection fitting with wet rags before unsoldering the connection to prevent damage to the
O-ring in the fitting.
4. Visually inspect screen in liquid injection fitting to verify it is plugged.
5. If plugged, carefully unscrew liquid injection fitting from compressor.
6. Install new O-ring on new liquid injection fitting.
7. Lubricate new O-ring with compressor oil, P/N 203-433.
8. Carefully thread new liquid injection fitting through compressor body into steel block on the inside. Make sure the fitting is
not cross-threaded in the steel block. Torque fitting to 11 to 13.5 Nm.
9. Solder the liquid injection tube to injection fitting.
NOTE: Use a heat sink or wrap the injection fitting with wet rags before soldering the connection to prevent damage to the
O-ring in the fitting.
10. Pressurise the system and test for refrigerant leaks.
11. If no leaks are found, evacuate the system.
12. Charge the unit with refrigerant.
13. Operate the unit at least 30 minutes and then inspect the oil level in the compressor. Add or remove oil if necessary.
14. Check the refrigerant charge and add refrigerant if needed.
Summary of Contents for T-1000R
Page 14: ...Safety Precautions 2 6 Warning Decals 2e24151g0 ...
Page 34: ...Maintenance Inspection Schedule 4 10 ...
Page 57: ...Unit Description 5 23 Purge Mode UT Series 1 3 4 5 2 ...
Page 67: ...Unit Description 5 33 Zone 1 Cool and Zone 2 Cool UT SPECTRUM Units ...
Page 69: ...Unit Description 5 35 Purge Mode UT SPECTRUM Units ...
Page 71: ...Unit Description 5 37 Zone 1 Cool and Zone 2 Heat UT SPECTRUM Units ...
Page 72: ...Unit Description 5 38 ...
Page 74: ...Diesel Electric Menu 6 28 Adjust Brightness 6 29 Time 6 30 ...
Page 120: ...Operating Instructions Standard HMI 7 18 ...
Page 152: ...Engine Maintenance 9 14 T Series Fuel and Oil System Components TK 376 ...
Page 154: ...Engine Maintenance 9 16 T Series Fuel and Oil System Components TK 270 ...
Page 156: ...Engine Maintenance 9 18 UT Series Fuel System Components AMA768 ...
Page 172: ...Engine Maintenance 9 34 T Series Engine Mounting Components for 2 Cylinder Engine ...
Page 184: ...Engine Maintenance 9 46 ...
Page 238: ...Refrigeration Maintenance 10 54 ...
Page 246: ...Clutch Maintenance 11 8 ...
Page 258: ...Structural Maintenance 12 12 ...
Page 264: ...Mechanical Diagnosis 13 6 ...
Page 265: ...14 Electric Standby Diagnosis ...
Page 268: ...Electric Standby Diagnosis 14 4 ...
Page 269: ...15 Refrigeration System Diagnosis ...
Page 272: ...Refrigeration System Diagnosis 15 4 ...
Page 280: ...Remote Evaporators 16 8 ...