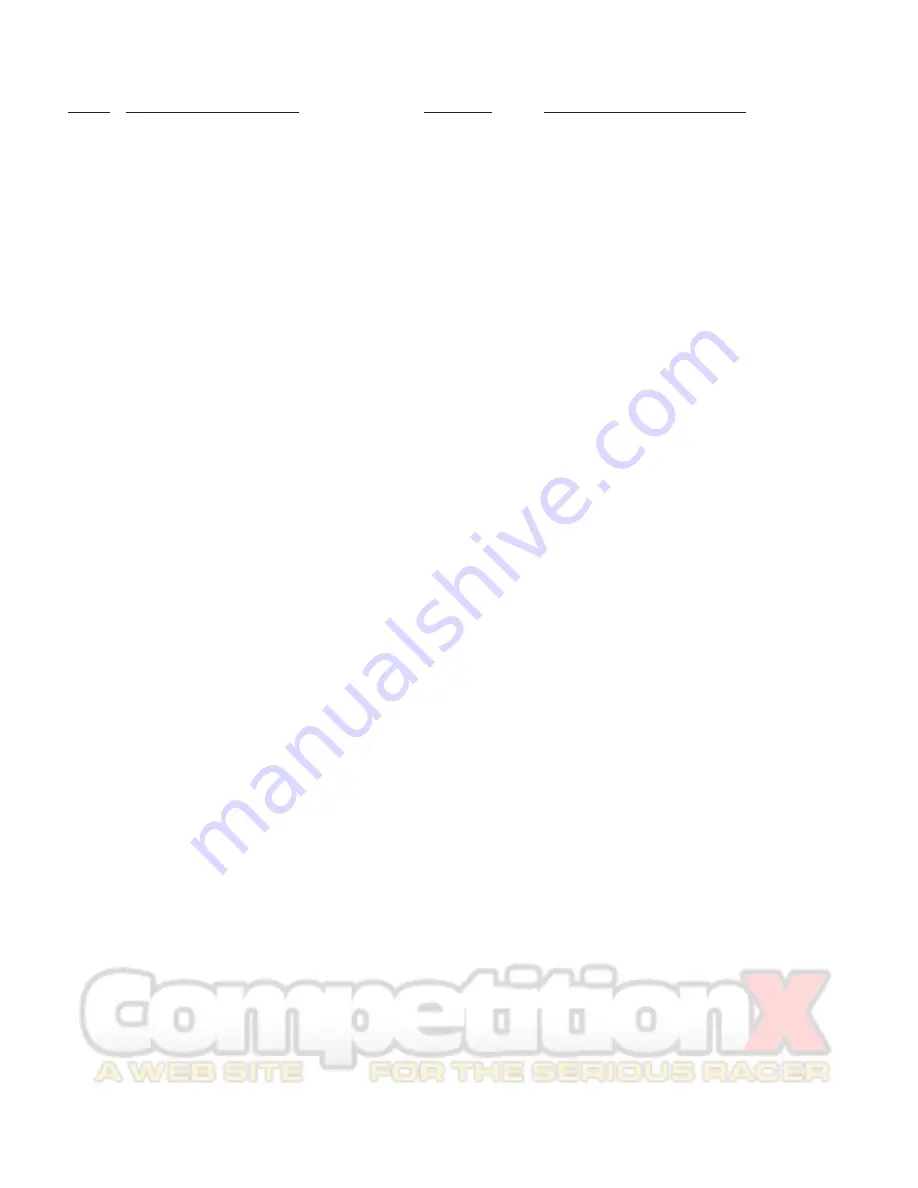
35
KEY #
KIT/PART DESCRIPTION
PART NO.
SPARE PARTS DESCRIPTION
58
#4 WASHER
LOSA6350
#4 and 1/8" Hardened Washers
59
DOGBONE
LOSA3091
Dogbone/Driveshaft - GenII - T
60
U-JOINT CROSS BALL
LOSA3027
Universal Bearing Cross, Reubildable
61
SOLID U-JOINT PIN
LOSA6407
U-Joint Pins (solid) 2.5mm x 12mm
62
REAR AXLE
LOSA3031
OFFSET REAR AXLE, .100, XXX2
63
U-JOINT YOKE
LOSA3083
Yoke and Screw for Dogbone
64
ASSEMBLY WRENCH
LOSA6030
Assembly Wrench (version 2)
65
HUB CARRIER, RIGHT REAR
LOSA2123
Rear Hubs - VLA - 3 Hole
66
HUB CARRIER, LEFT REAR
LOSA2123
Rear Hubs - VLA - 3 Hole
67
BEARING SPACER, FRONT/REAR
LOSA9942
Bearing Spacer/Wheel Washer Set
68
SPACER, REAR AXLE
LOSA9942
Bearing Spacer/Wheel Washer Set
69
DRIVE PIN, REAR AXLE
LOSA6401
Pins — Wheels and Gears
70
SPACER, REAR HUB
LOSA2127
Rear Hub Spacers (1/8" x .060")
71
HINGE PIN, FRONT KING/REAR OUTER
LOSA6088
Hinge Pins, 1/8" x 1.246", Ti-Nitride
72
2-3/4" TITANIUM TURNBUCKLE
N/A
73
DIFF NUT CARRIER
LOSA2911
One-Piece Diff Nut/Carrier
74
5/64" ALLEN WRENCH
N/A
75
BELEVILLE WASHER
LOSA2933
Differential Screw, Hardware, and Seal
76
DIFF SPRING
LOSA2933
Differential Screw, Hardware, and Seal
77
MALE OUTDRIVE HALF
LOSA2935
Outdrive Cup/Diff Set
78
DIFF GREASE (CLEAR)
LOSA3065
Silicone Differential Compound
79
DIFF RING
LOSA3070
Transmission Drive Rings (2)
80
5mm x 8mm BEARING
LOSA6907
5mm x 8mm Bearings
81
DIFF GEAR
LOSA3074
Transmission Diff Gear, 46 Teeth
82
3/32" CARBIDE DIFF BALLS
LOSA6951
3/32" Carbide Diff Balls (12)
83
FEMALE OUTDRIVE HALF
LOSA2935
Outdrive Cup/Diff Set
84
DIFF ADJUSTING SCREW
LOSA2933
Differential Screw, Hardware, and Seal
85
FOAM THRUST BEARING SEAL
LOSA2933
Differential Screw, Hardware, and Seal
86
3mm x 8mm THRUST BEARING WASHER
LOSA3099
Full Compliment Thrust Bearing Set
87
WHITE THRUST / ASSEMBLY GREASE
LOSA3066
Assembly Grease
88
5/64" THRUST BEARING BALLS
LOSA3099
Full Compliment Thrust Bearing Set
89
4-40 x 7/8" FLAT HEAD SCREW
LOSA6226
4-40 x 7/8" Flat-Head Screws (10)
90
TOP SHAFT
LOSA9932
Alum. Gear /Slipper Shaft, 18 Teeth
91
4-40 x 5/16" BUTTON HEAD SCREW
LOSA6245
4-40 x 5/16 Button Head Screws (10)
92
1/16" ALLEN WRENCH
N/A
94
LEFT GEARBOX HALF
LOSA2938
Transmission Case Set and Spacer (Gen II)
95
1/2" x 3/4" BEARING
LOSA6908
1/2" x 3/4" Ball Bearings w/Teflon Seal (2)
96
MOTOR PLATE
LOSA2941
Lightened Motor Plate - Black Anodize
97
RIGHT GEARBOX HALF
LOSA2938
Transmission Case Set and Spacer (Gen II)
98
IDLER GEAR SHAFT
LOSA2937
Idler Gear, 32 Teeth, and Shaft
99
TOP SHAFT SPACER
LOSA2938
Transmission Case Set and Spacer (Gen II)
100
1/8" x 3/8" BEARING
LOSA6909
1/8" x 3/8" Ball Bearings (2)
101
IDLER GEAR
LOSA2937
Idler Gear, 32 Teeth, and Shaft
102
2-56 x 3/8" CAP HEAD SCREW
LOSA2940
Transmission Screw Set (Gen II)
103
4-40 x 1" CAP HEAD SCREW
LOSA6223
Transmission Screw Set (Gen II)
104
SLIPPER BACK PLATE
LOSA3132
Slipper Backing Plate
105
SLIPPER PAD
LOSA3123
Slipper Pad
106
86 TOOTH SPUR GEAR
LOSA3987
86T 48-Pitch Kevlar® Spur Gear
107
SLIPPER SPACER
LOSA3124
Slipper Spring, Cup, Spacer, Bushing, and Washer
108
SLIPPER SPRING
LOSA3124
Slipper Spring, Cup, Spacer, Bushing, and Washer
109
SPRING RETAINING WASHER
LOSA3124
Slipper Spring, Cup, Spacer, Bushing, and Washer
110
4-40 LOCKNUT
LOSA6305
4-40 Aluminum Locknuts, Low Profile (6)
111
MOTOR GUARD
LOSA4121
Motor Guard, & Body Mnts. - Black
112
4-40 x 1-1/2" CAP HEAD SCREW
LOSA2940
Transmission Screw Set (Gen II)
113
SHOCK O-RING
LOSA5014
O-Rings for Shock Cartridge (8)
114
SHOCK CARTRIDGE BODY
LOSA5015
Double O-Ring Shock Cartridge
115
SHOCK CARTRIDGE SPACER
LOSA5015
Double O-Ring Shock Cartridge