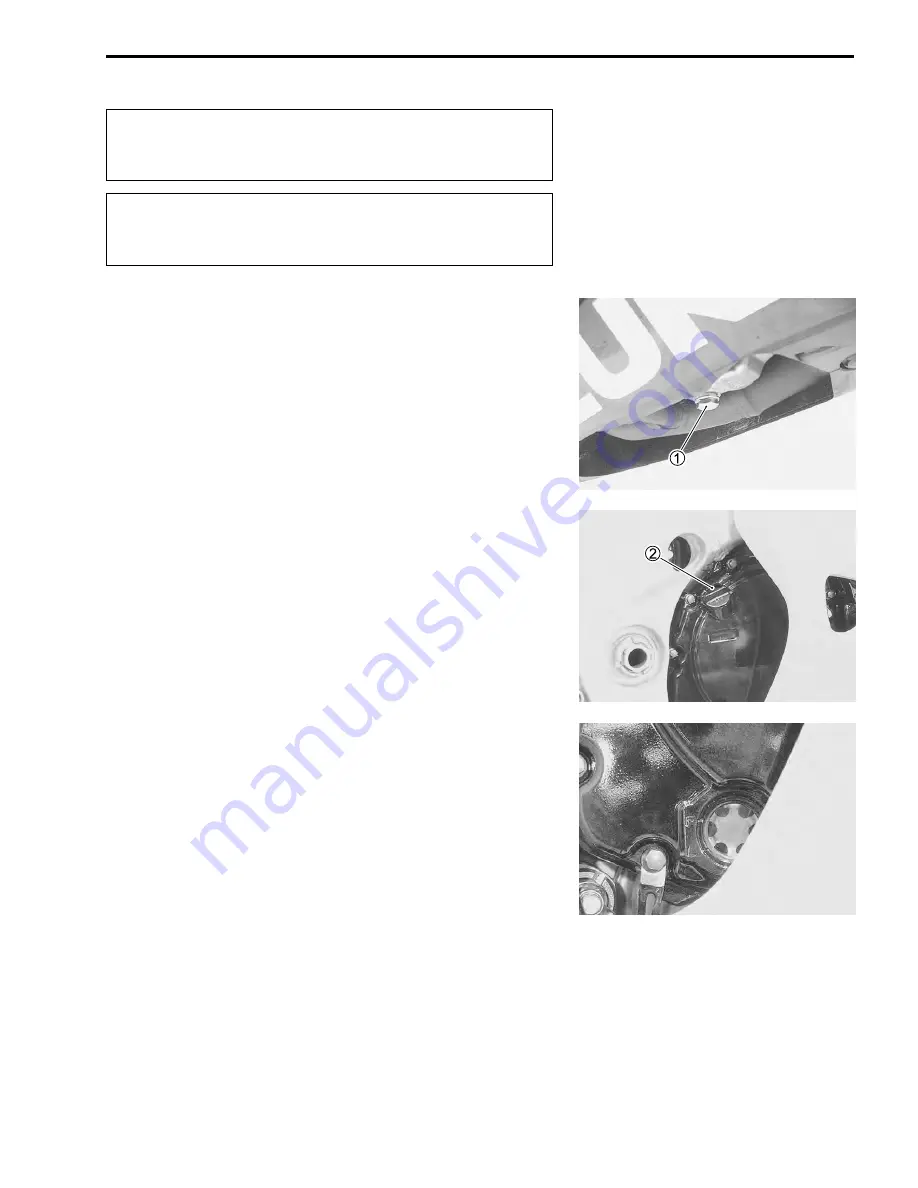
PERIODIC MAINTENANCE 2-13
ENGINE OIL AND OIL FILTER
(ENGINE OIL)
Replace initially at 1 000 km (600 miles, 1 month) and ev-
ery 6 000 km (4 000 miles, 6 months) thereafter.
(OIL FILTER)
Replace initially at 1 000 km (600 miles, 1 month) and ev-
ery 18 000 km (11 000 miles, 18 months) thereafter.
Oil should be changed while the engine is warm. Oil filter replace-
ment at the above intervals, should be done together with the en-
gine oil change.
ENGINE OIL REPLACEMENT
• Keep the motorcycle upright.
• Place an oil pan below the engine, and drain oil by removing the
oil drain plug
1
and filler cap
2
.
• Tighten the drain plug
1
to the specified torque, and pour fresh
oil through the oil filler. The engine will hold about 2.8 L (3.0/2.5
US/Imp qt) of oil. Use an API classification of SF or SG oil with
SAE 10W/40 viscosity.
!
!
!
!
!
Oil drain plug: 23 N.m (2.3 kgf.m, 16.5 lb-ft)
• Start up the engine and allow it to run for several minutes at
idling speed.
• Turn off the engine and wait about three minutes, then check
the oil level through the inspection window. If the level is below
mark “L”, add oil to “F” level. If the level is above mark “F”, drain
oil to “F” level.
Summary of Contents for GSX-R750
Page 1: ...GSX R750 SUZUKI MOTOR CORPORATION PRINTED IN JAPAN FEBRUARY 2000 99500 37112 03E...
Page 46: ...PERIODIC MAINTENANCE 2 29...
Page 97: ...ENGINE 3 49 Driveshaft Countershaft TRANSMISSION PARTS LOCATION...
Page 172: ...FISYSTEMANDINTAKEAIRSYSTEM 4 25 FI SYSTEM WIRING DIAGRAM...
Page 249: ...5 20 COOLINGANDLUBRICATIONSYSTEM ENGINE LUBRICATION SYSTEM MAIN GALLERY To sub gallery...
Page 250: ...COOLINGANDLUBRICATIONSYSTEM 5 21...