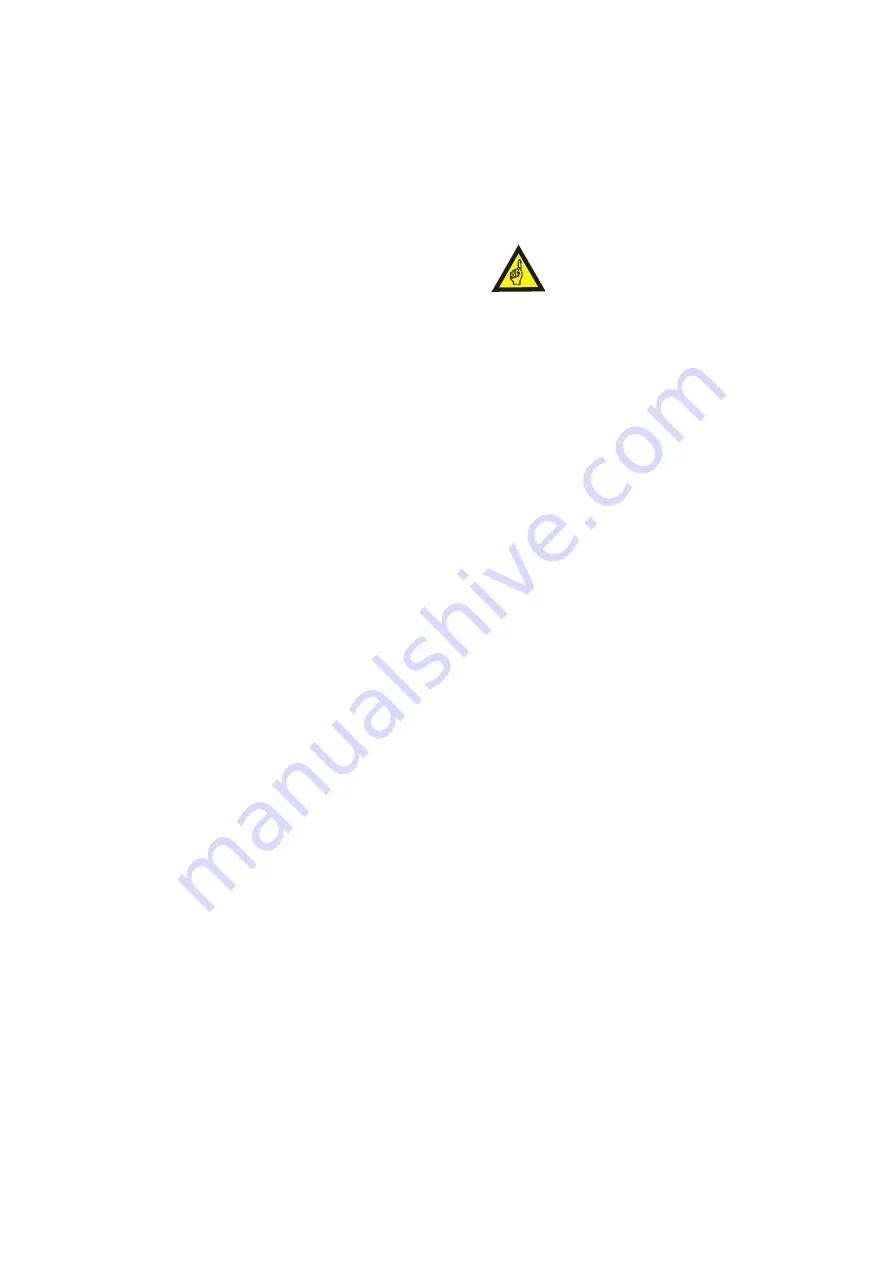
OPERATING INSTRUCTIONS
4618 - 021
27
MANUALLY SETTING THE DETECTOR FOR A PRODUCT
General
At this stage the metal detector should have been
installed and the user should be familiar with the
principles of operation, basic operation of the control
panel, and have worked through the universal settings
guide as described in previous sections.
The Safeline detector has the ability to store settings
for 21 different product numbers. Each product
number represents a group of settings, the
appropriate setting of sensitivity, phase, frequency,
power drive, timer type, inverse detect, automatic
tracking, and product signal cancellation may be
allocated to each product number. Note product signal
cancellation is available in five product numbers only.
Sensitivity, phase, frequency, and power drive when
set correctly will optimise the detection sensitivity.
The timer type will optimise reject operation, for
different pack lengths or product speed.
Inverse detection will allow the action of the reject
timer to be reversed, allowing product with no metal
contamination to be rejected whilst metal
contaminated product is accepted.
Automatic tracking will ensure that the products
sensitivity and phase value remain optimised for
products with varying product effect characteristics.
Product signal cancellation may give improved
performance for a minority of products which present
consistent product effect characteristics.
The phase control can play a dominant role in
optimising the detectors performance for particular
products. For many products, those which do not
exhibit a product effect, the optimum setting of the
detector will be with phase set at around 0
°
. With
those products that exhibit a product effect, improved
detection sensitivity can be achieved by aligning the
phase control to minimise the product signal.
When making adjustments to the detector for a
particular product the user should ensure that product
is passed through the detector aperture in its usual
manner to create a worst case product effect
condition.
Notes on Passing Product Through the
Detector
NOTE
The product should be continually moving, the
detector will not operate with standing/stationary
product in the aperture.
To ensure that the detector is set up correctly and will
operate satisfactorily during normal production, we
recommend that the product used for set up is passed
through the detector in the worst case position and
orientation which would occur during normal
production.
The worst case product effect condition is when the
greatest disturbance of the coil system/largest product
signal is experienced. This occurs when the coil
system condition changes from no product to
maximum product.
If the product is a continuous length/strip, the worst
case product effect is given from the leading
edge/face of the product. Product fully spanning the
detector head gives a much reduced signal.
With individual or boxed/cartoned product the worst
case product effect condition occurs as the product
enters and leaves the detector. If the product is
rectangular the product effect signal will generally be
more severe if the product enters the detector
aperture long edge leading, as opposed to short edge
leading. The gaps between the products will create
the worst case product effect condition. If successive
products are touching a reduced product signal will
result.
For the majority of product types the worst case
condition occurs the closer the product is to the faces
of the detector aperture.
The technique of setting up to the worst case product
effect condition will ensure that no false product
rejections occur during normal running conditions.
Summary of Contents for Signature
Page 16: ......
Page 26: ...INSTALLATION 10 4618 021 Fig 5 Typical Metal Detector Conveyor ...
Page 31: ...INSTALLATION 4618 021 15 Fig 10 Cable Gland Assemblies for Power Supply Unit ...
Page 52: ...OPERATING INSTRUCTIONS 36 4618 021 Fig 14 Supervisor Mode Flow Chart ...
Page 55: ...OPERATING INSTRUCTIONS 4618 021 39 Fig 15 Engineer Mode Flow Chart ...
Page 71: ...OPERATING INSTRUCTIONS 4618 021 55 Fig 16 Pack Sensor Mode Flow Chart ...
Page 82: ...OPERATING INSTRUCTIONS 66 4618 021 Fig 18 QA Inspector And Operator Flow Chart ...
Page 92: ...OPERATING INSTRUCTIONS 76 4618 021 Fig 19 Viewing Mode Flow Chart ...