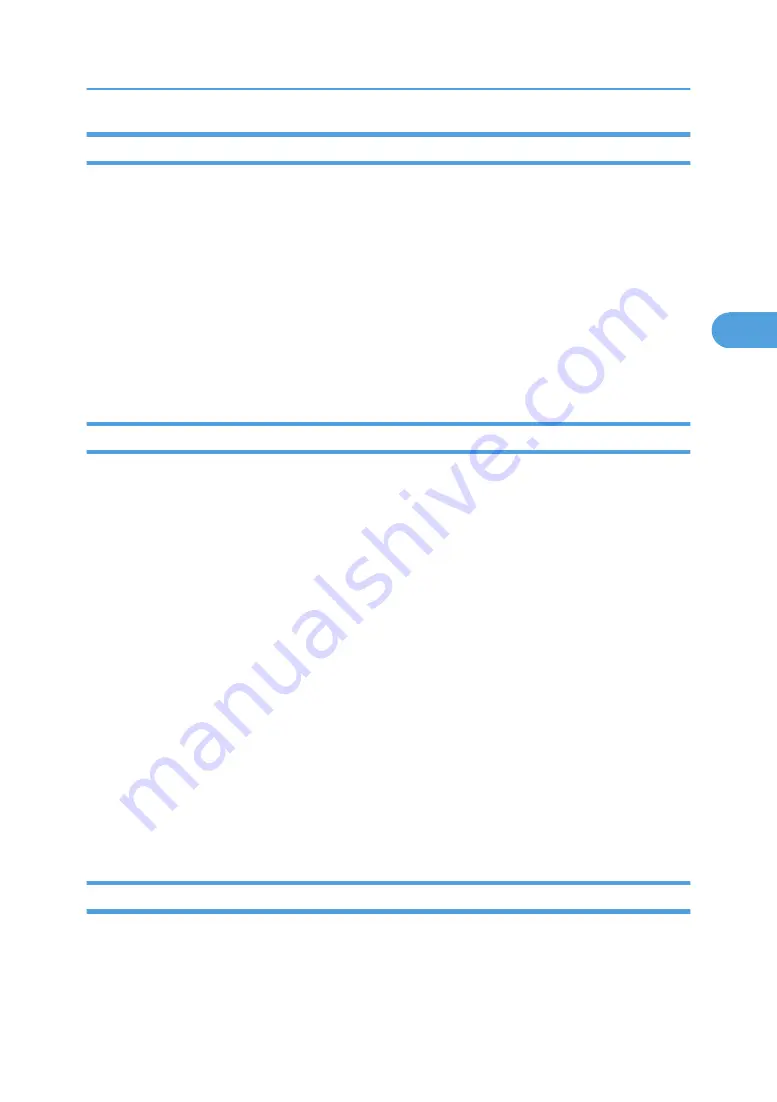
After installing the new PM parts
1. Turn on the main power switch.
2. Output the SMC logging data with SP5-990-004 and check the counter values.
3. Make sure that the PM counters for the replaced units are “0” with SP7-803. If the PM counter for a
unit was not reset, then reset that counter with SP 7-804.
4. Make sure that the exchange counter counts up with SP7-853.
5. Make sure that the counters for the previous units (SP7-906) on the new SMC logging data list (from
step 2 above) are equal to the counters (SP7-803) for these units on the previous SMC logging data
list (the list that was output in the “Before removing the old parts” section).
6. Make sure that the unit replacement date is updated with SP7-950.
Preparation before operation check
1. Clean the exposure glasses (for DF and book scanning).
2. Enter the user tools mode.
3. Do the “Automatic Color Calibration “(ACC) for the copier mode & printer mode as follows:
• Print the ACC test pattern (User Tools > Maintenance > ACC > Start).
• Put the printout on the exposure glass.
• Put 10 sheets of white paper on the test chart. This ensures the precise ACC adjustment.
• Close the ARDF or the platen cover.
• Press “Start Scanning” on the LCD. Then, the machine starts the ACC.
4. Exit the User Tools mode, and then enter the SP mode.
5. Do the “Forced line position adjustment” as follows.
• First do SP2-111-3 (Mode c).
• Then do SP2-111-1 (Mode a).
• To check if SP 2-111-1 was successful, watch the screen during the process. A message is
displayed at the end. Also, you can check the result with SP 2-194-10 to -12.
6. Exit the SP mode.
Operation check
Check if the sample image has been copied normally.
PM Parts Settings
153
3
Summary of Contents for MPC 2800 AT-C2
Page 1: ...Model AT C2 Machine Code D023 D025 Field Service Manual July 2008 Subject to change...
Page 2: ......
Page 16: ...Overview Component Layout 1 Product Information 14 1...
Page 152: ...2 Installation 150 2...
Page 156: ...3 Preventive Maintenance 154 3...
Page 171: ...Left Cover 1 Left cover A x 6 Rear Cover 1 Rear cover A x 8 Exterior Covers 169 4...
Page 176: ...3 Ozone filters A in the right top cover 4 Replacement and Adjustment 174 4...
Page 243: ...3 Toner transport motor A x 3 x 1 Toner Collection Unit 1 Gear Unit p 228 Drive Unit 241 4...
Page 249: ...6 Development clutch K A x 1 Drive Unit 247 4...
Page 265: ...8 Thermopile F x 2 x 1 Fusing 263 4...
Page 287: ...Controller Box Open I ITB Power Supply Board Electrical Components 285 4...
Page 327: ...Controller Self Diagnostics 325 5...
Page 354: ...MEMO 352...
Page 355: ...Model AT C2 Machine Code D023 D025 Appendices July 2008 Subject to change...
Page 356: ......
Page 359: ...SP1 xxx System and Others 496 SP2 XXX Scanning image quality 496 3...
Page 360: ...4...
Page 396: ...2 Appendix Maintenance Tables 40 2...
Page 474: ...4 Appendix Process Control Error Conditions 118 4...
Page 476: ...5 Appendix Troubleshooting Guide 120 5...
Page 484: ...5 Appendix Troubleshooting Guide 128 5...
Page 492: ...Sensor Locations 6 Appendix Jam Detection 136 6...
Page 500: ...7 Appendix Electrical Component Defects 144 7...
Page 854: ...MEMO 498...
Page 855: ...MEMO 499...
Page 856: ...MEMO 500 EN...