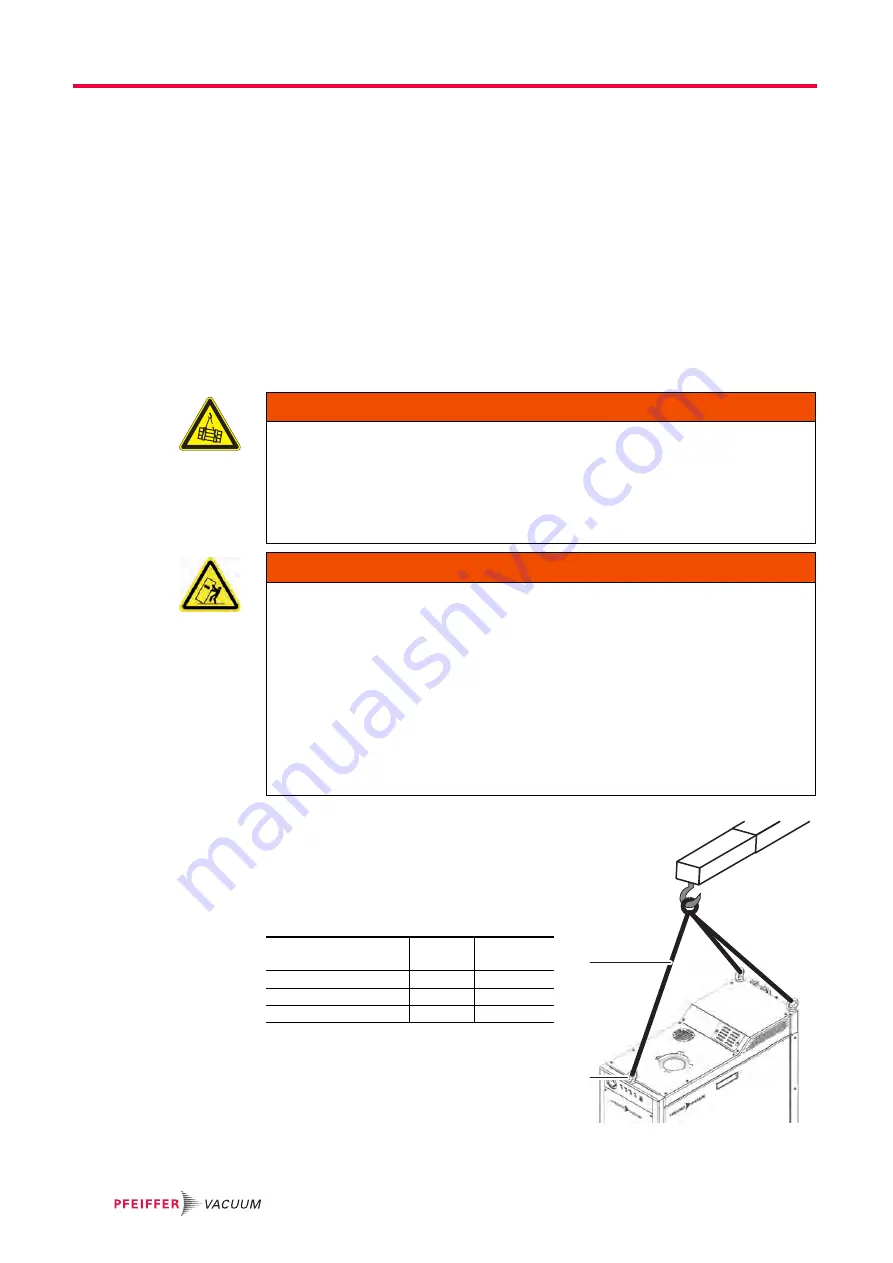
12
Transport and storage
3
Transport and storage
Upon delivery, check that the product has not been damaged during transport. If the
product is damaged, take the necessary measures with the carrier and notify the manu-
facturer. In all situations we recommend:
Keeping the product in its original packaging so it stays as clean as it was when dis-
patched by us. Only unpack the product once it has arrived at the location where it will
be used.
Keeping the packaging (recyclable materials) in case the product needs to be trans-
ported or stored.
Keeping the blanking plates in place on the inlet, exhaust and purge ports while the
product is not connected to the pumping line.
3.1
Transport
To lift the product:
Use a lifting device suitable for the product's
weight.
Use a lifting sling (1) with several arms with
the following characteristics:
Screw the hoisting rings (2) (delivered in the
crate in separate packaging) in the suitable
holes. With a sling (1), lift the pump using
hoisting rings.
Adjust the leveling pads of the frame and low-
er the pump on the castors to move it over
short distances.
WARNING
Risk of injury associated with heavy loads
Given the weight of the product, it should be removed from its packaging only by per-
sonnel qualified and trained in handling heavy materials.
Use the lifting rings and devices provided with the product.
The manufacturer cannot be held liable for the consequences of using lifting devices
other than those provided.
WARNING
Risk of tilting
Even though compliance with EEC safety rules is guaranteed, all necessary precautions
should be taken when moving, installing and operating the product.
Do not place the product on an inclined plane: its weight could cause the operator to
be dragged.
Only use castors to move it short distances.
Place it on a flat, hard floor.
Do not push the product sideways.
Adjust the levelling feet for operation to make sure that the pump is not supported by
the castors. (Refer to
Technical data and dimensions
in these operating instruc-
tions for location of the center of gravity.)
A 2404 to
A 3004
A 124 to
A 1804
Number of arms
4
3
Length of each arm
> 500 mm > 500 mm
Load per arm
> 400 kg
> 350 kg
1
2
Summary of Contents for A 1204H
Page 88: ...ETL Mark...
Page 89: ...Certificate of conformance to SEMI...