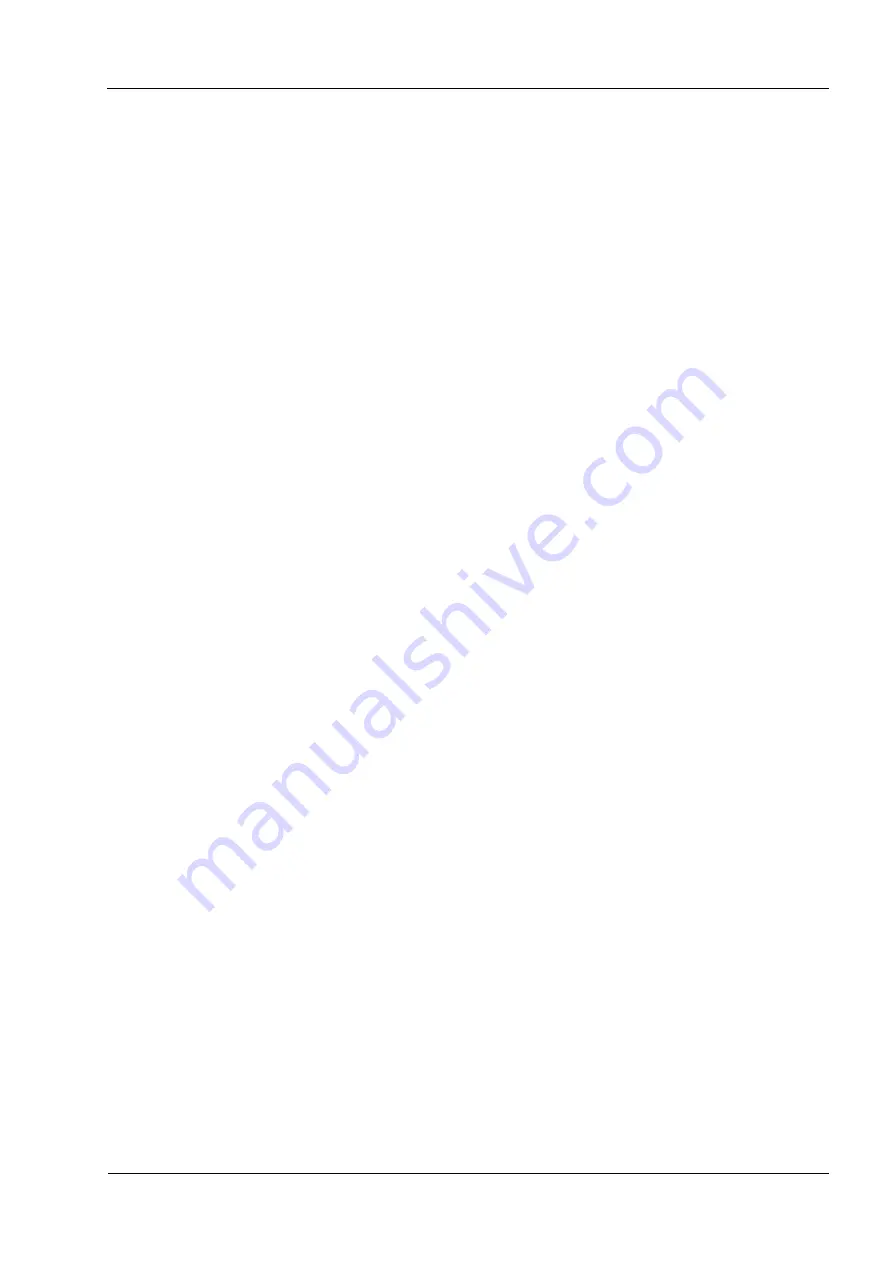
Workshop Manual, TPD 1353E, Issue 3
115
9
Peregrine EDi and 1300 Series EDi
Turbocharger
9
General description
Warning! Turbochargers operate at high speed and at high temperatures. Keep fingers, tools and other
objects away from the inlet and outlet ports of the turbocharger and avoid contact with hot surfaces.
A turbocharger, is fitted between the exhaust and induction manifolds. The turbocharger is driven by exhaust
gases and supplies air to the engine at more than atmospheric pressure. The turbocharger is lubricated by oil
from the oil filter head. The oil passes through the bearing housing of the turbocharger and returns to the
lubricating oil sump.
Some turbochargers are fitted with a waste-gate unit. This unit, which is controlled by boost pressure, allows
some of the exhaust gases to by-pass the turbine rotor at higher engine speeds. With this arrangement, the
turbocharger can be designed to be more effective at lower engine speeds.
Always use the manufacturer’s instructions and specialist assistance to fit the service kit for the turbocharger.
Caution: Do not use a caustic solution to clean the components of the turbocharger because the turbocharger
will be damaged.
This document has been printed from SPI². Not for Resale
Summary of Contents for 1300 EDi Series
Page 12: ...xii This page is intentionally blank This document has been printed from SPI Not for Resale...
Page 62: ...This page is intentionally blank This document has been printed from SPI Not for Resale...
Page 76: ...This page is intentionally blank This document has been printed from SPI Not for Resale...
Page 122: ...This page is intentionally blank This document has been printed from SPI Not for Resale...
Page 170: ...This page is intentionally blank This document has been printed from SPI Not for Resale...
Page 190: ...This page is intentionally blank This document has been printed from SPI Not for Resale...
Page 198: ...This page is intentionally blank This document has been printed from SPI Not for Resale...
Page 204: ...This page is intentionally blank This document has been printed from SPI Not for Resale...
Page 226: ...This page is intentionally blank This document has been printed from SPI Not for Resale...