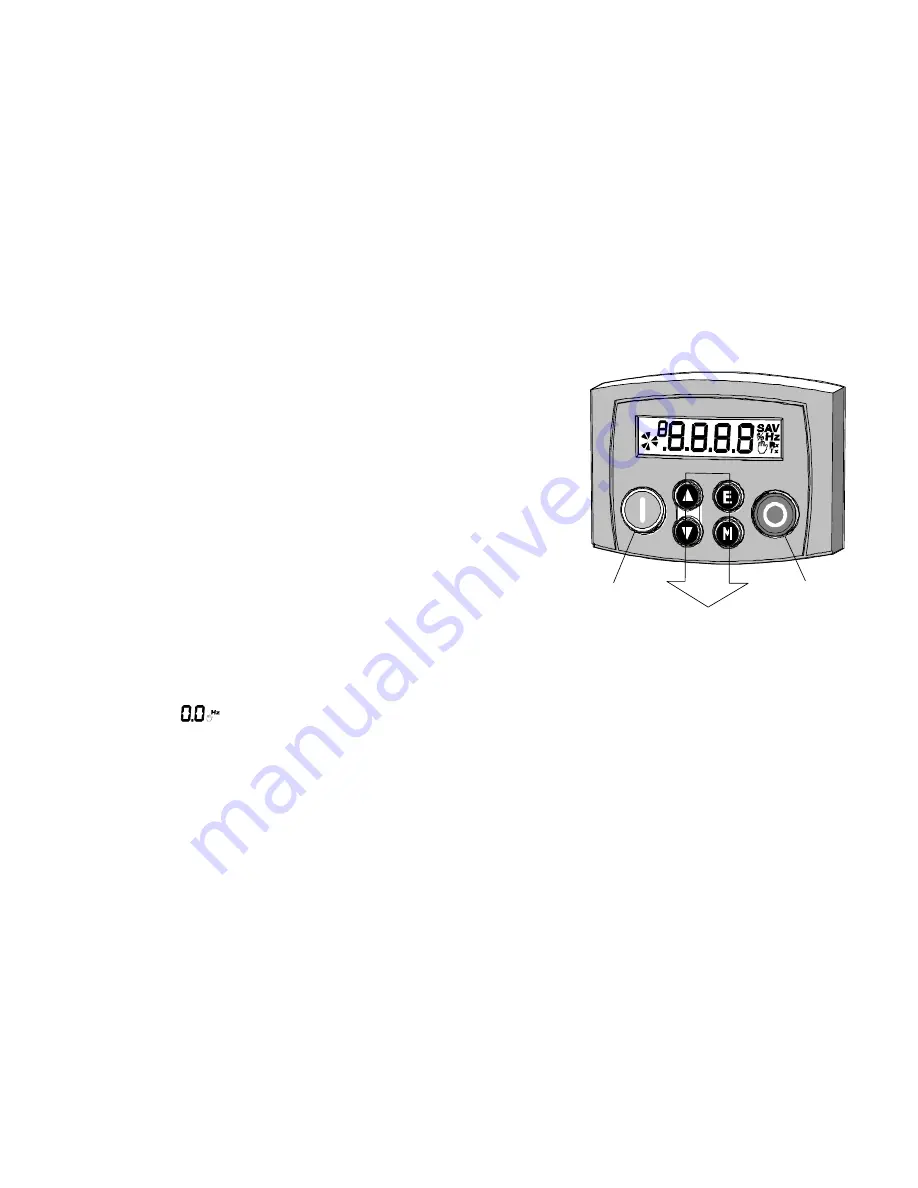
5-2
The Keypad
650S AC Drive
The 6511 Keypad
The 6511 Keypad (Man-Machine Interface, MMI) provides for local control
of the drive, monitoring, and complete access for application programming.
The 650S can be fitted with either a Standard or Remote Keypad. Both
Keypads fit on the front of the drive, but the Remote Keypad (with its extra
connector) can also be remote-mounted up to 3 metres away using a
connecting lead: refer to Chapter 3: “Installing the Drive” – Fitting the
Remote Keypad.
To remove a Keypad, simply pull it away from the drive. To refit it, push it
back into place.
The product rating label identifies the Drive/Keypad type: refer to Chapter 9:
“Technical Specifications” – Understanding the Product Code.
The Power-Up Condition
On initial power-up, direct from the factory, the drive is in Local Control and the MMI will display the Local Setpoint,
.
All parameters will be at factory default settings. Any changes to these conditions are automatically saved. The drive will
initialise on subsequent power-ups with the previously saved settings and control mode, Local or Remote Control.
Programming Keys
Local
Key
Control
Local
Key
Control