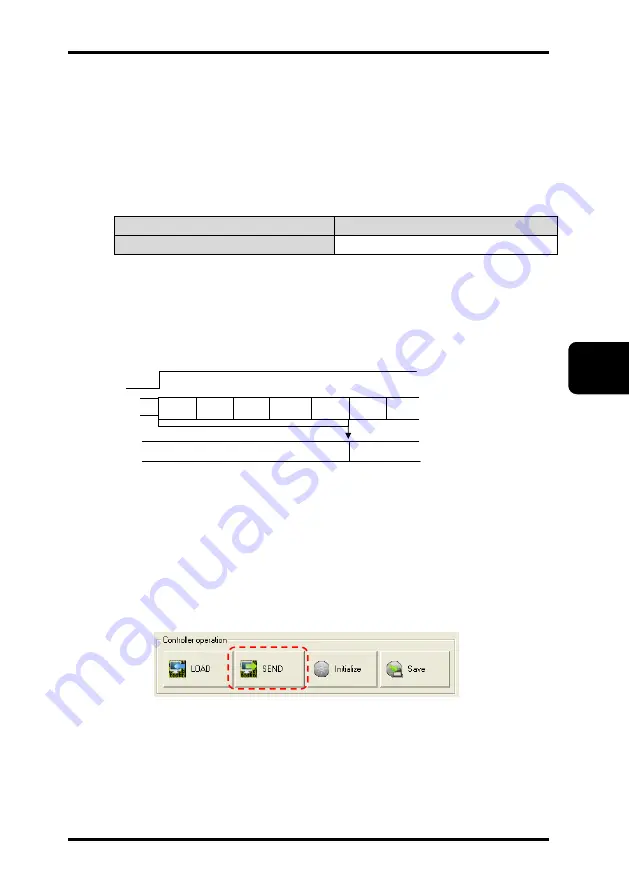
Chapter 4 Description of Functions
4-79
4
Filter
●Median filter
The median filtering process is performed in the time direction for the calcu-
lation values of OUT1, 2 and 3, and the measurement value of the shape
judgment. Except for sudden variations of the values, this process is effective
in stabilizing the measurement values.
Item
Setting range
Filter
None (default value), Median 3, 5, 7
Keep in mind that the calculated results will be in the unfixed state until the
data is accumulated to the size of the median filter.
When filter size is 5
Measurement value unfixed (Alarm value)
Measurement value processed with median filter
1
2
3
4
5
6
7
Sending set value to sensor
When the set values of each item for the HL-D3SMI are changed, the set
values in the sensor are not changed.
Before measurement, be sure to execute SEND operation on the main screen.
"SEND"
operation transmits the set values of all items in total.
Start of
measurenment
No. of
measurenment
Summary of Contents for HL-D3 Series
Page 9: ...Preface 7 ...
Page 27: ...Preface 24 MEMO ...
Page 43: ...Chapter 1 Before Use 1 16 1 MEMO ...
Page 219: ...Chapter 4 Description of Functions 4 140 4 MEMO ...
Page 298: ...1 Apx Appendix 1 Index 2 ...
Page 304: ......