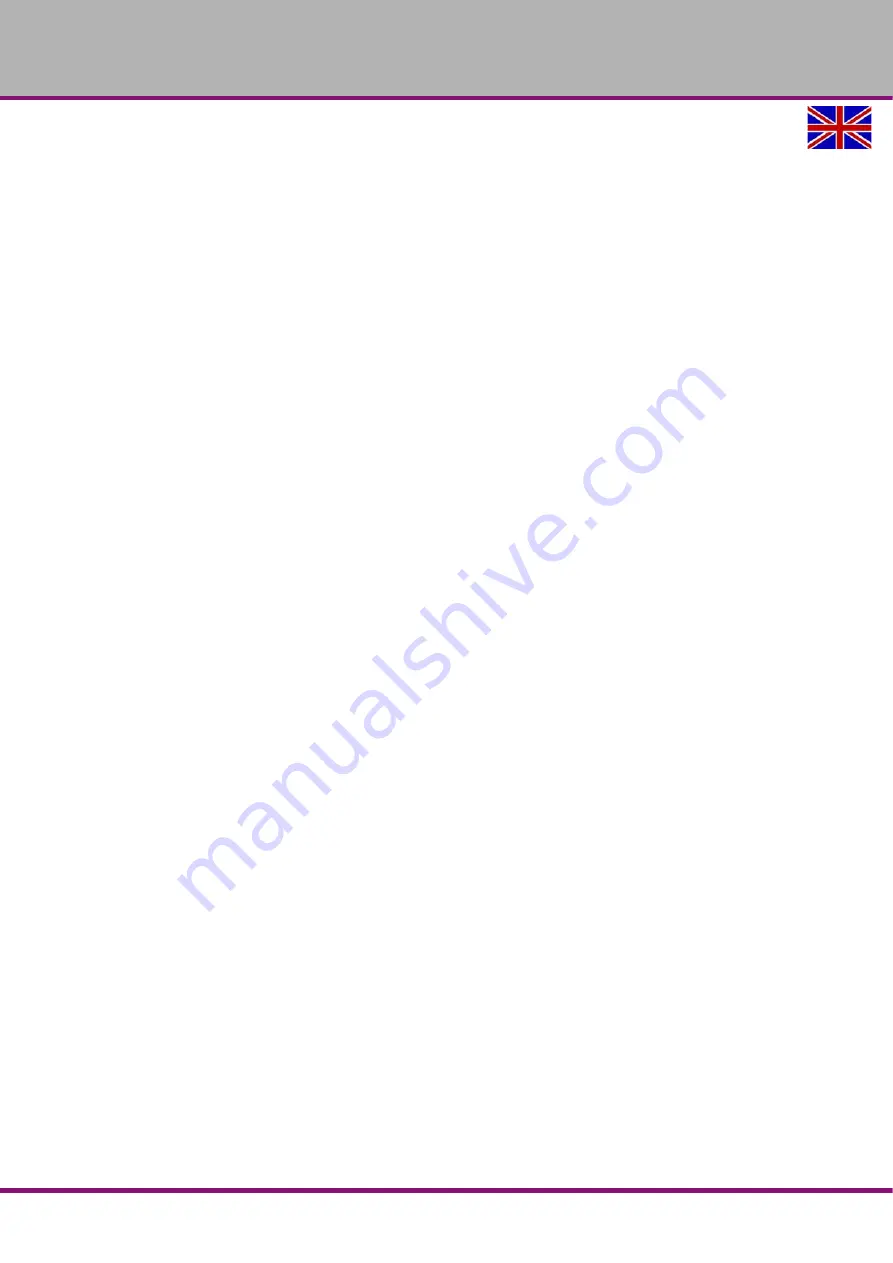
OPTIMUM
M A S C H I N E N - G E R M A N Y
General information about CNC
Version 1.1.6 dated 2014-10-16
Page 50
Original operating instructions
F150
GB
4
General information about CNC
4.1
Compensation of geometry
It is necessary to be able to measure any currently actual position of the CNC-controlled axis in
order to perform tool moves on workpieces.The measured value is related to a machine fixed
zero position and is compared to the target position which is predefined by the programs.
Required knowledge:
coordinate systems of the machine and workpiece
reference points of the machine, tool and workpiece
type of distance measurement
options of dimensioning and dimension compensation
Basics:
For chip removal relative moves between the tool and the workpiece are required. For program-
ming all moves are related to the resting workpiece.
4.2
Coordinate systems on CNC machine tools
Types of coordinate systems
Coordinate systems allow the exact description of all points on a working plane, respectively in
an area.
Generally they are divided into
Cartesian coordinate system and
the polar coordinate system
4.2.1 Cartesian coordinate system
A Cartesian coordinate system also called a rectangular coordinate system possesses two
coordinate axes (two-dimensional Cartesian coordinate system) or also three coordinate axes
(three-dimensional Cartesian coordinate system) which are perpendicular to one another in
order to exactly describe the points.
On a two-dimensional Cartesian coordinate system, e.g. on the X, Y-coordinate system, each
point is clearly defined on the plane by indicating the coordinates (X,Y).
The distance from the Y-axis is called the X-coordinate and the distance from the X-axis is
called Y-coordinate. Those coordinates may possess positive or negative algebraic signs.
The three-dimensional Cartesian coordinate system is required to display and determine the
position of special workpieces, e.g. milling parts.
In order to clearly describe a point in the space, three coordinates are required which are
named according to the corresponding axes X-, Y- or Z-coordinates.
Such three-dimensional coordinate systems with positive and negative areas on the coordinate
axis allow the exact description of any locations, e.g. in the working area of a CNC milling
machine, independent from where the workpiece datum is set.