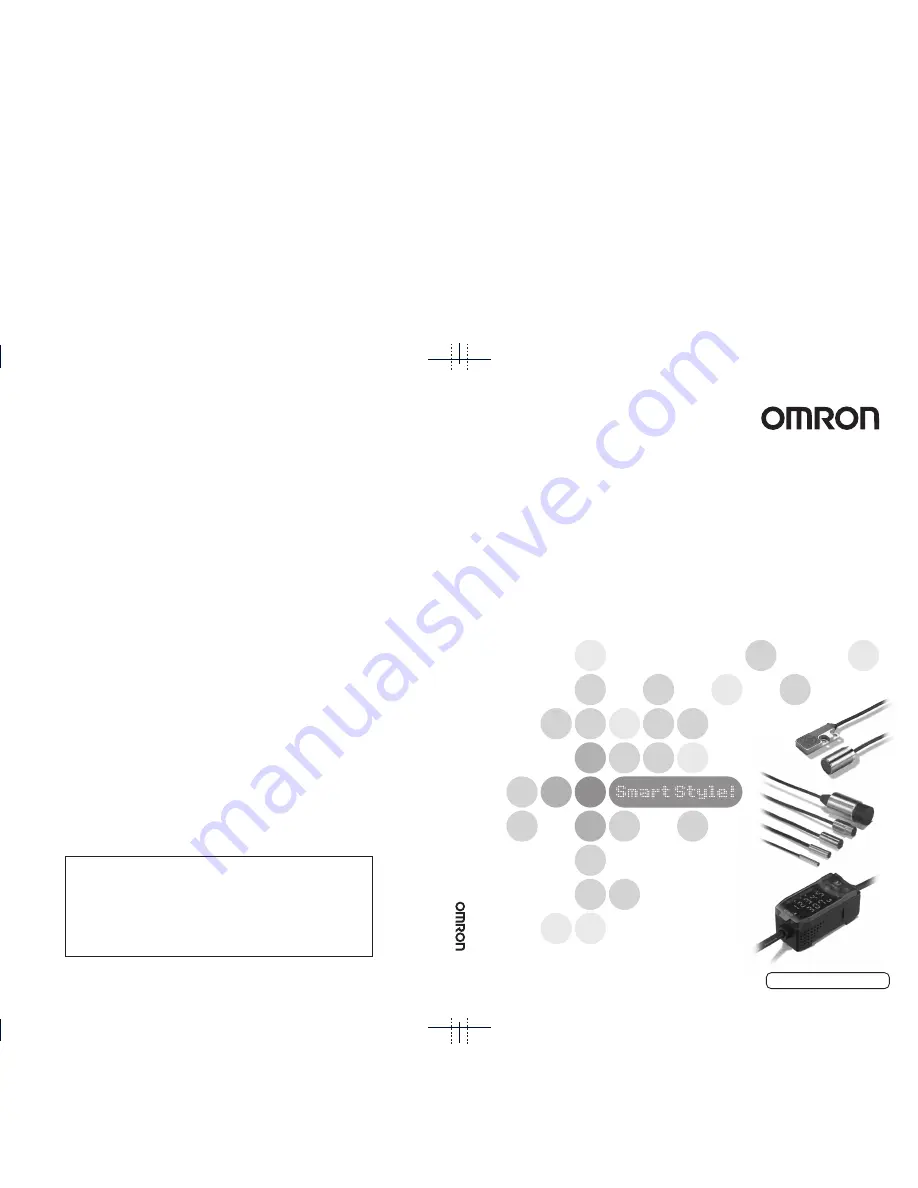
ZX-E Series
Smart Sensors: Inductive Displacement Type
ZX-E Series Smar
t Sensor
s:
Inductive Displacement
T
ype
Operation Manual
Cat. No. Z166-E1-02A
©
OMRON Corporation 2002
All Rights Reserved.
Note: Specifications subject to change without notice.
Printed in Japan.
0405-0.1M (1002) (M)
Authorized Distributor:
OMRON Corporation
Industrial Automation Company
Sensing Devices Division H.Q.
Application Sensors Division
Shiokoji Horikawa, Shimogyo-ku,
Kyoto, 600-8530 Japan
Tel: (81)75-344-7068/Fax: (81)75-344-7107
Regional Headquarters
OMRON EUROPE B.V.
Sensor Business Unit,
Carl-Benz-Str. 4, D-71154 Nufringen,
Germany
Tel: (49)7032-811-0/Fax: (49)7032-811-199
OMRON ELECTRONICS LLC
1 East Commerce Drive, Schaumburg, IL 60173
U.S.A.
Tel: (1)847-843-7900/Fax: (1)847-843-8568
OMRON ASIA PACIFIC PTE. LTD.
83 Clemenceau Avenue,
#11-01, UE Square,
239920 Singapore
Tel: (65)6835-3011/Fax: (65)6835-2711
OMRON (CHINA) CO., LTD.
Room 2211, Bank of China Tower,
200 Yin Cheng Road (M)
Shanghai, 200120 China
Tel: (86)21-5037-2222/Fax: (86)21-5037-2200
Operation Man
ual
Cat.
No.
Z166-E1-02A
Summary of Contents for ZX-E -
Page 4: ...2 Preface ZX E Operation Manual Preface ...
Page 8: ...6 Preface Contents ZX E Operation Manual Preface ...
Page 11: ...9 ZX E Operation Manual Preface PREFACE ...
Page 12: ...10 Preface ZX E Operation Manual PREFACE ...
Page 17: ...Section 1 FEATURES 15 ZX E Operation Manual Section 1 FEATURES ZX E Features 16 ...
Page 24: ...22 Section 1 ZX E Features ZX E Operation Manual Section 1 FEATURES ...
Page 62: ...60 Section 3 Adjusting Linearity ZX E Operation Manual Section 3 BASIC OPERATION ...
Page 162: ...160 Appendices Quick Reference for Displays ZX E Operation Manual APPENDICES ...