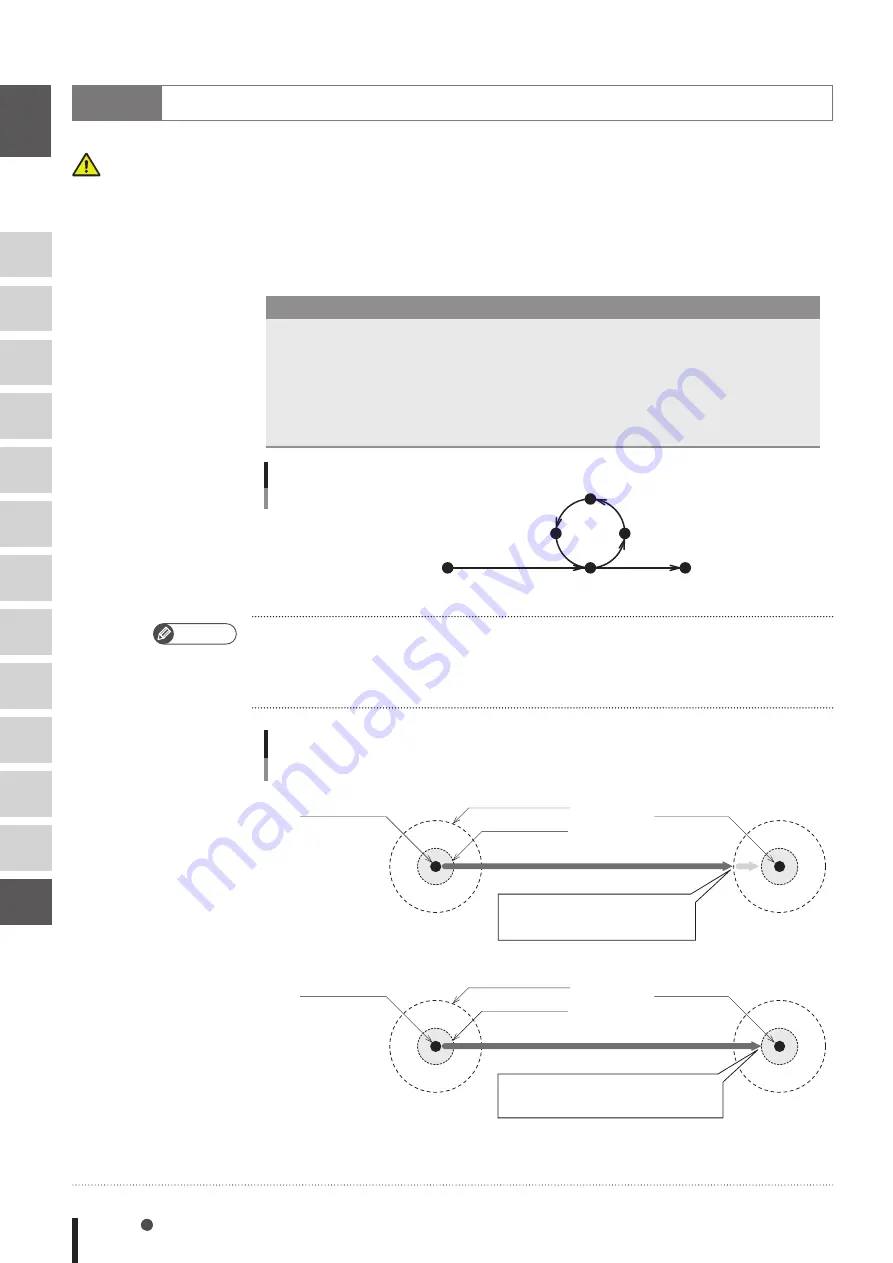
8-100 Chapter 8 Robot Language Lists
8
A
B
C
D
E
F
G
H
I
J
K
L
M
62
MOVE
●
●
Circular interpolation movement
Execution START condition: Movement of all specified axes is complete (within the tolerance range).
Execution END condition: Movement of all specified axes has begun.
All movement axes arrive at the same time.
In circular interpolation, an arc is generated based on 3 points: the current position, an
intermediate position, and the target position.
Therefore, circular interpolation must be
specified by an even number of points.
SAMPLE
MOVE L,P20 ···················· Linear interpolation movement of robot 1
occurs from the current position to P20.
MOVE C,P21,P22,P23,P20 ········ Circular interpolation movement occurs
through points P21, P22, P23, P20.
MOVE L,P24 ···················· Linear interpolation movement occurs
to P24.
SAMPLE:MOVE C
P23
Current position
P24
P22
P21
P20
33811-R7-00
• Circular interpolation is possible within the following range: radius 0.100mm to 5,000.000mm.
• Circle distortion may occur, depending on the speed, acceleration, and the distance between points.
• On robots with an R-axis, the R-axis speed may become too fast and cause an error, depending
on the R-axis movement distance.
Movement command types and the corresponding movement
Current position
Tolerance range
OUT position range
Target position
Current position
Tolerance range
OUT position range
Target position
The command ends when the axis
enters the OUT position range, and
the next command is then executed.
The next command is executed when
the axis arrives in the tolerance range.
1. PTP movement
2. Linear interpolation movement
33703-R9-00
CAUTION
•
In YRCX, the motion of
interpolation movement
c o m m a n d a n d E N D
condition are different
from conventional model.
Addition of the CONT
setting to the movement
command allows to the
equivalent movement
and END condition in
conventional model.
MEMO
Summary of Contents for SCARA YRCX Series
Page 1: ... 7 6HULHV DW 1R 1 5 5RERW RQWUROOHU 352 5 00 1 0 18 6 5 5RERWV 5 6HULHV ...
Page 2: ......
Page 20: ......
Page 26: ......
Page 27: ...Chapter 2 Constants 1 1 Outline 2 1 2 2 Numeric constants 2 1 3 3 Character constants 2 2 ...
Page 28: ......
Page 32: ......
Page 52: ......
Page 54: ......
Page 61: ...Chapter 5 Multiple Robot Control 1 1 Overview 5 1 2 2 Command list with a robot setting 5 2 ...
Page 62: ......
Page 66: ......
Page 76: ......
Page 78: ......
Page 92: ......
Page 328: ......
Page 408: ......
Page 409: ...Chapter 11 User program examples 1 1 Basic operation 11 1 2 2 Application 11 8 ...
Page 410: ......
Page 432: ......
Page 488: ......
Page 489: ...Chapter 13 Appendix 1 1 Reserved word list 13 1 2 2 Changes from conventional models 13 3 ...
Page 490: ......
Page 496: ......
Page 497: ...Index ...
Page 498: ......
Page 504: ......
Page 505: ......
Page 506: ... DW 1R 1 XWKRUL HG LVWULEXWRU 3ULQWHG LQ XURSH ...