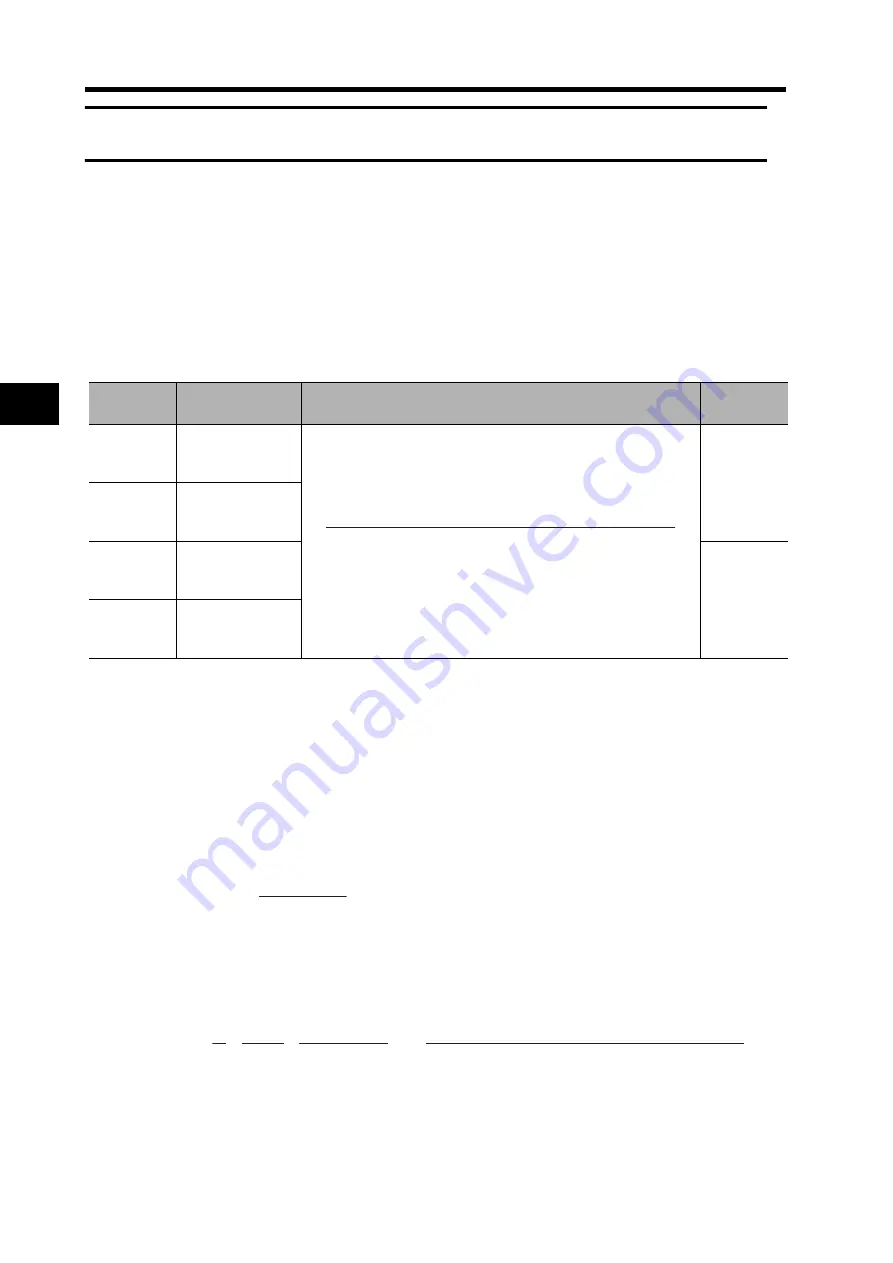
5-9
5-5 Electronic Gear
5
Operating Functions
5-5 Electronic Gear
The Servomotor can be rotated for the number of pulses obtained by multiplying the command
pulses by the electronic gear ratio.
This function is effective in the following cases:
When fine-tuning the position and speed of two lines that are to be synchronous.
When using a position controller with a low command pulse frequency.
When you want to set the machine travel distance per pulse, to 0.01 mm for example.
Parameters Requiring Settings
*1. The Electronic Gear Switch Input (GESEL) is used to switch between Electronic Gear Ratio
Numerator 1 (Pn46) and Electronic Gear Ratio Numerator 2 (Pn47).
Operation
Calculation Method
The following equation shows the relation between the number of internal command pulses (F)
after the electronic gear ratio multiplication and the number of command pulses (f) per Servomotor
rotation.
The Servomotor has a 2,500 pulses/rotation encoder. Therefore, the number of internal command
pulses (F) in the Servo Drive is 10,000 pulses/rotation (2,500 pulses/rotation
×
4).
Given the conditions above, the relation between the number of command pulses per Servomotor
rotation (f) and the electronic gear ratio is as follows:
Parameter
No.
Parameter name
Explanation
Reference
Pn46
Electronic Gear
Ratio Numerator 1
*1
Set the pulse rate for command pulses and Servomotor travel dis-
tance.
The maximum value of the calculated numerator is 2,621,440.
Any higher setting than this will be invalid, and the numerator will
be 2,621,440.
Pn47
Electronic Gear
Ratio Numerator 2
*1
Pn4A
Electronic Gear
Ratio Numerator
Exponent
Pn4B
Electronic Gear
Ratio
Denominator
Electronic Gear Ratio Denominator (Pn4B)
x 2
Electronic Gear Ratio Numerator Exponent (Pn4A)
Electronic Gear Ratio Numerator 1 (Pn46)
or
Electronic Gear Ratio Numerator 2 (Pn47)
F = f
×
Pn4B
Pn46
×
2
Pn4A
=
Pn4B
Pn46
×
2
Pn4A
F
f
10000
f
=
(
)
=
Encoder resolution (by a factor of 4)
Number of command pulses for Servomotor rotation