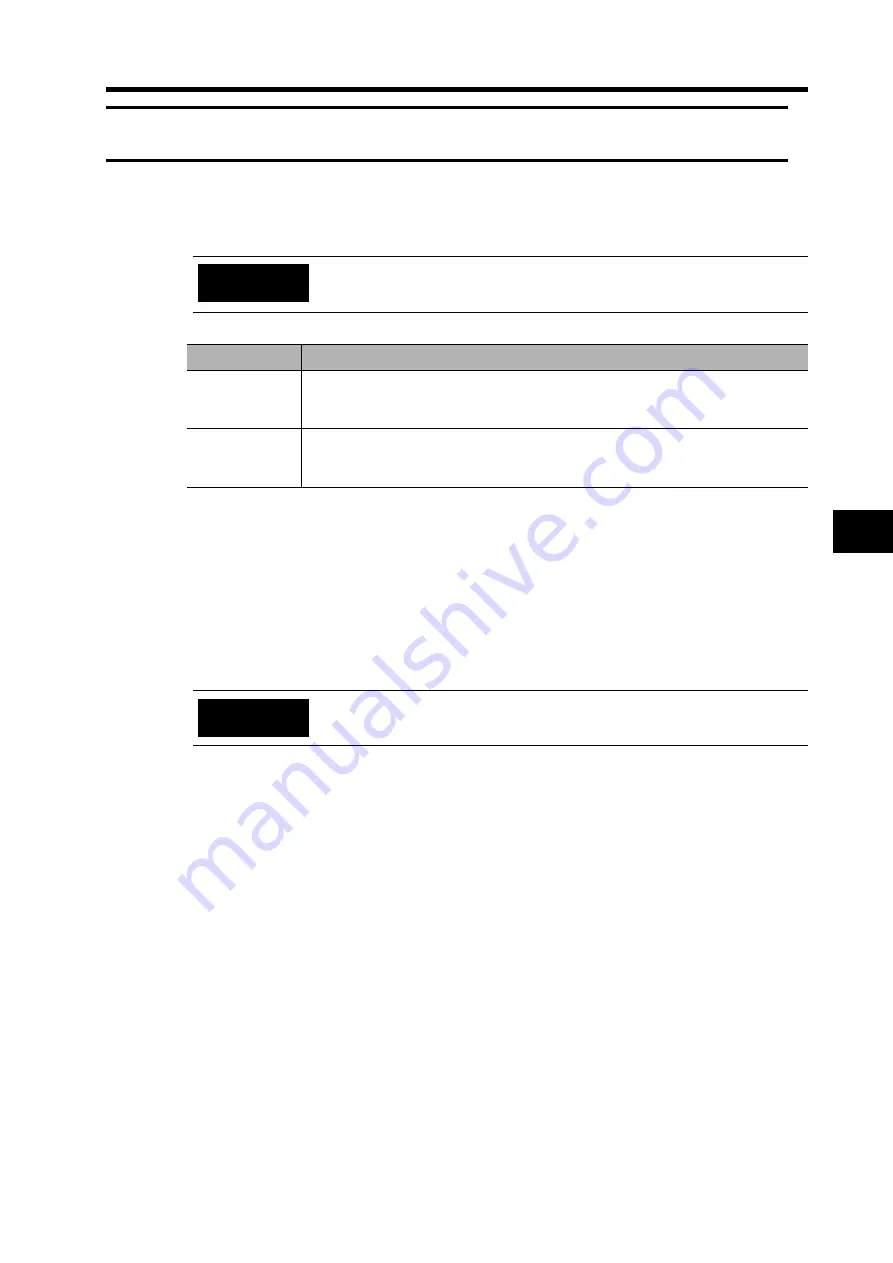
7-8
7-3 Autotuning
7
Adjustment Functions
7-3 Autotuning
Autotuning operates the Servomotor according to command patterns created automatically in the
Servo Drive, estimates the load inertia from the required torque and automatically sets the optimal
gain.
A tuning error will occur if the servo turns OFF (e.g., the RUN Command Input (RUN) turns OFF),
or a deviation counter reset occurs (e.g., the Deviation Counter Reset (ECRST)) during the
autotuning.
If the load inertia cannot be estimated during autotuning, the setting of each gain cannot be
changed and remains the same as before autotuning.
When autotuning is being executed, the Servomotor output torque will reach the maximum output
torque set in the Torque Limit (Pn5E).
When autotuning is being executed, the Forward Drive Prohibit Input and Reverse Drive Prohibit
Input will be ignored.
Autotuning Setting Method
1. Setting the Operating Pattern
Set the operating pattern using the Autotuning Operation Setting (Pn25).
The operating pattern set in Pn25 will repeat in a maximum of five cycles. Starting with the third
cycle, the acceleration level will double every cycle.
Depending on the load, the operating pattern does not repeat in five cycles when operation is
completed, or the acceleration does not change. In either case, this is not an error.
2. Moving the Load
Move the load to the position where there’s no problem if the Servomotor operates according to
the setting in Pn25. The Servomotor will rotate once or twice in both forward and reverse
depending on the settings.
3. Moving to the Autotuning Mode Display
For information on moving to the Autotuning Mode Display, refer to
Autotuning may not function properly under the conditions described in the
following table. If autotuning does not function properly, use manual
tuning.
Precautions
for Correct Use
Conditions under which autotuning does not function properly
Load inertia
If the load inertia is less than 3 times the rotor inertia.
If the load inertia is more than 20 times the rotor inertia.
If the load inertia changes.
Load
If the machine rigidity is extremely low.
If there is backlash or play in the system.
If the static friction torque is greater than the dynamic friction torque.
If the Servomotor oscillates, immediately cut off the power, or turn OFF the
RUN Command Input (RUN). Then, return each gain to the default setting.
Precautions
for Safe Use