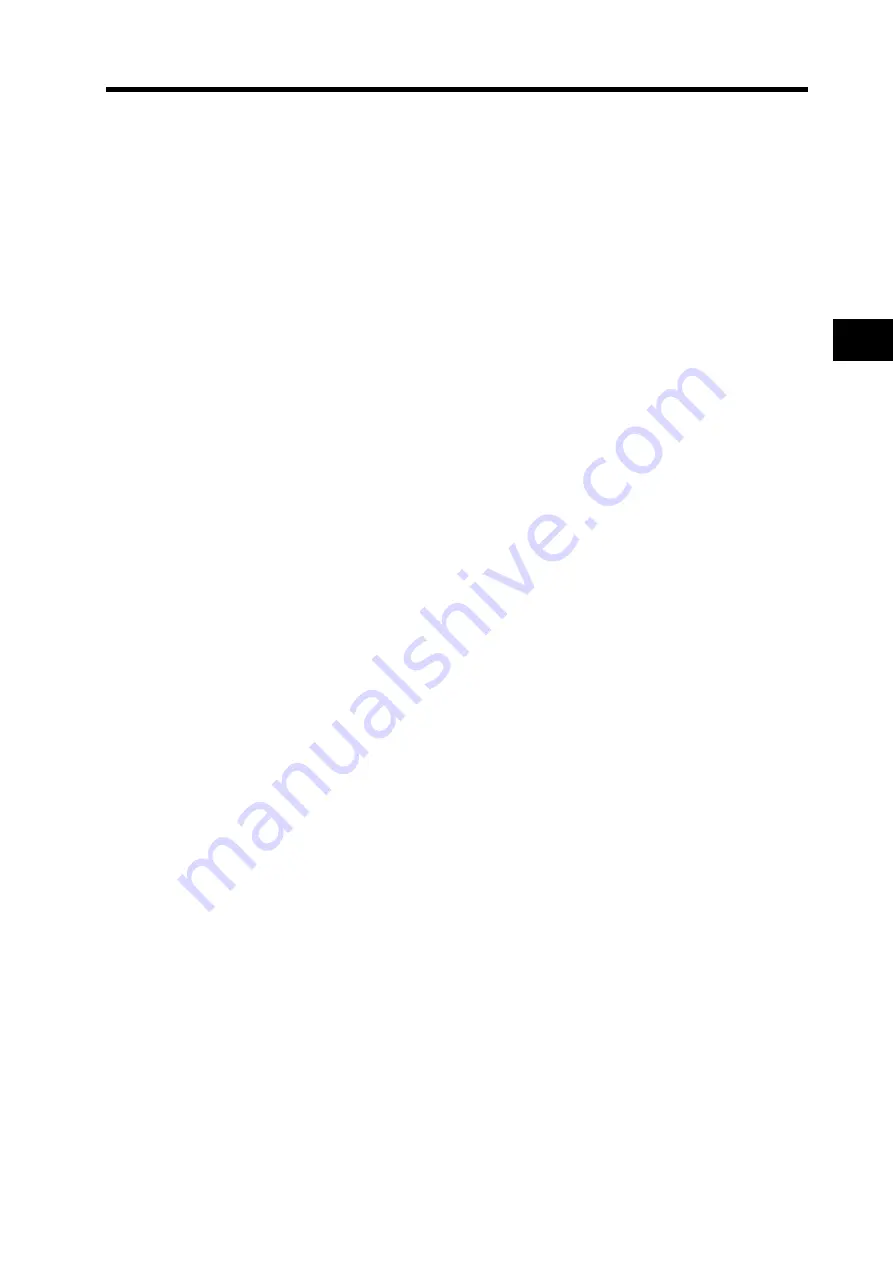
4-30
4-3 Wiring Conforming to EMC Directives
4
System Design
Improving Control I/O Signal Noise Resistance
Positioning can be affected and I/O signal errors can occur if control I/O is influenced by noise.
Use completely separate power supplies for the control power supply (especially 24 VDC) and for
the external operation power supply. In particular, do not connect the two power supply ground
wires.
Install a noise filter on the primary side of the control power supply.
If Servomotors with brakes are used, do not use the same 24-VDC power supply for both the
brakes and the control I/O. Additionally, do not connect the ground wires. Connecting the ground
wires may cause I/O signal errors.
Keep the power supply for pulse commands and deviation counter reset input lines separated from
the control power supply as far apart as possible. In particular, do not connect the two power
supply ground lines.
We recommend using line drivers for the pulse command output.
Always use twisted-pair shielded cable for the pulse command and deviation counter reset signal
lines, and connect both ends of the shield to frame grounds.
If the control power supply wiring is long, noise resistance can be improved by adding 1-
µ
F
laminated ceramic capacitors between the control power supply and ground at the Servo Drive
input section or the controller output section.
For open-collector specifications, keep the length of wires to within two meters.
Selecting Other Parts for Noise Resistance
This section explains the criteria for selecting other connection components required to improve
noise resistance.
Understand each component’s characteristics, such as its capacity, performance, and applicable
conditions when selecting the components.
For more details, contact the manufacturers directly.