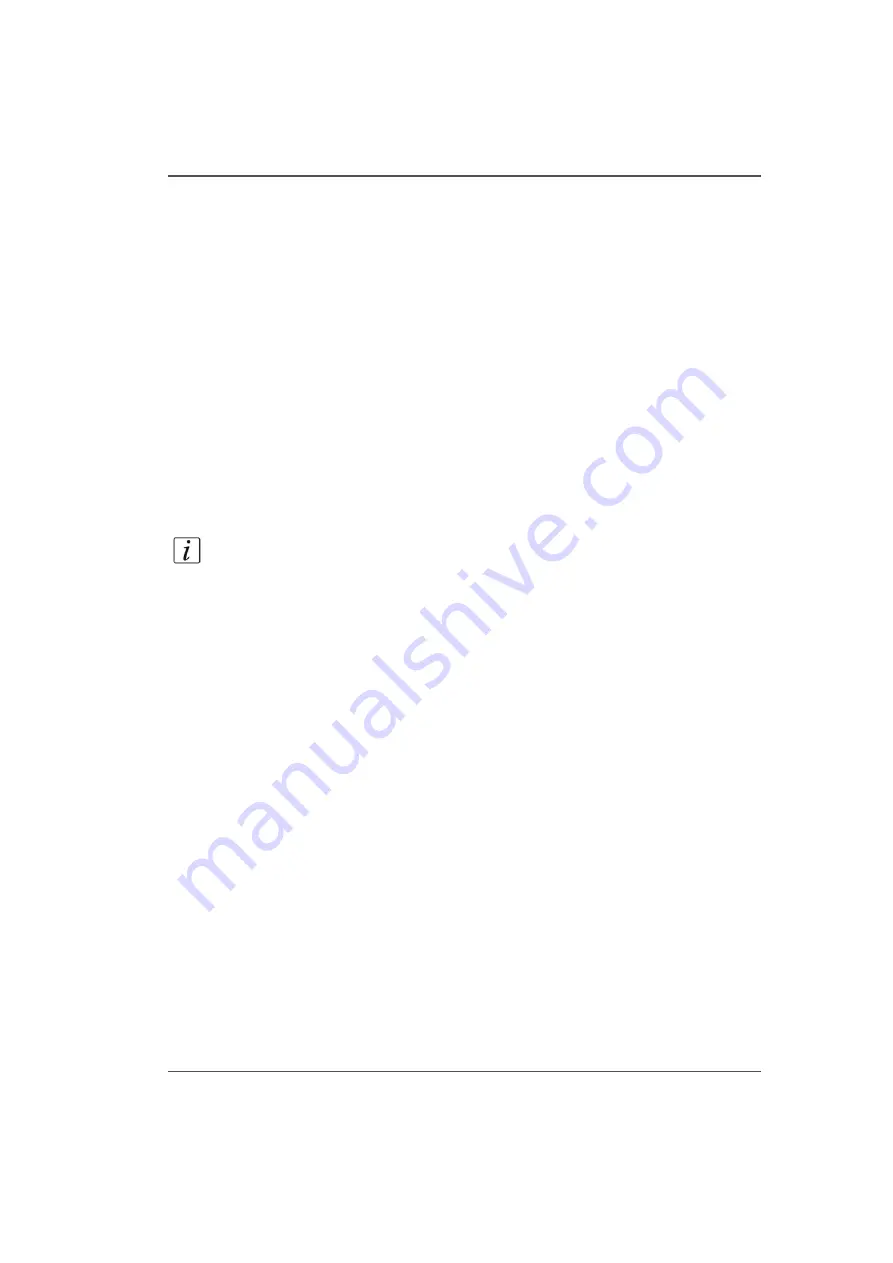
105
Roll Media Theory of Operations
Introduction to Media Loading
Loading and threading roll media is a manual process. A media shaft is required for
both the supply and take-up media rolls. The function of the shaft is to provide
additional core support and a non-slip drive condition between the drive motors and
the media rolls. The media shafts must be inserted in to the supply media roll and
take-up media core before they can be loaded. The media shafts are inserted
manually and are automatically locked in place by a spring-loaded media shaft drive
couplers. In order to thread media from the supply roll to the take-up roll the operator
uses a foot pedal to control the take-up media drive. The foot pedals allow the supply
media to be driven forward or reverse in non-initialized control mode. While media
is being driven forward the operator can manually guide the media under the media
tension bar then up and over the platen. The forward and reverse drive directions can
be used to help position the media to facilitate taping to the take-up media core.
Refer to media threading label on the Roll Media Option for details on how to thread
the media when loading. The media roll can be threaded to print either print side
out or print side in.
Note:
For optimum printing results it is recommended the media be aligned such
that no more than a 1mm offset exists between the supply and take-up media rolls.
The Roll Media Option design does not have a media drive pinch. Therefore, all
printing requires the media to be taped to the take-up media core. Once the media
has been taped to the take-up core the operator selects the icon Initialize.
Media Initialization
A media supply roll must be installed, and media threaded and taped to the take-up
core before you can initialize the media. The media initialization process prepares
the printer for printing after the operator selects the Initialize icon in the Roll
Manger. When the initialization is complete, the system will switch to the initialized
control mode and is ready for printing.
Introduction to Media Unloading
Select the Unload Media icon from the printer software to change the control mode
from initialized to non-initialized. . At this point the supply shaft pays out a small
amount of media until the media tension bar is in the zero position (stationary-sitting
on the media ramp). This is required so the media tension bar does not fall down if
the media cannot be held stationary by the vacuum platen during the cutting process.
The Unload Media command changes the functionality of the foot pedal switches to
the following:
During this mode the system monitors the position of the media tension bar and the
supply roll. If upward media tension bar motion or forward supply roll motion is
Summary of Contents for Arizona 250 GT
Page 1: ...Arizona 250 GT Oc User manual User Manual Revision D...
Page 6: ...6 Table of Contents...
Page 7: ...7 Chapter 1 Introduction...
Page 16: ...16 Chapter 1 Introduction Product Compliance...
Page 17: ...17 Chapter 2 Product Overview...
Page 21: ...21 Chapter 3 Safety Information...
Page 45: ...45 Chapter 4 How to Navigate the User Interface...
Page 51: ...51 Operator Interface Hardware Thermal fluid heater Purge pump Purge valve Printheads jetting...
Page 70: ...70 Chapter 4 How to Navigate the User Interface Installation and Upgrade Module...
Page 71: ...71 Chapter 5 How to Operate the Arizona 250 GT...
Page 96: ...96 Chapter 5 How to Operate the Arizona 250 GT Underlay Board to Reduce Artifacts...
Page 97: ...97 Chapter 6 How to Operate the Roll Media Option...
Page 122: ...122 Chapter 6 How to Operate the Roll Media Option How to Determine Media Advance Correction...
Page 123: ...123 Chapter 7 How to Use the Static Suppression Upgrade Kit...
Page 127: ...127 Chapter 8 Ink System Management...
Page 134: ...134 Chapter 8 Ink System Management How to Change Ink Bags...
Page 135: ...135 Chapter 9 Error Handling and Troubleshooting...
Page 139: ...139 Chapter 10 Printer Maintenance...
Page 172: ...172 Chapter 10 Printer Maintenance How to Clean the Rubber Capstan...
Page 173: ...173 Appendix A Application Information...
Page 176: ...176 Appendix A Application Information Application Resources on the Web Site...