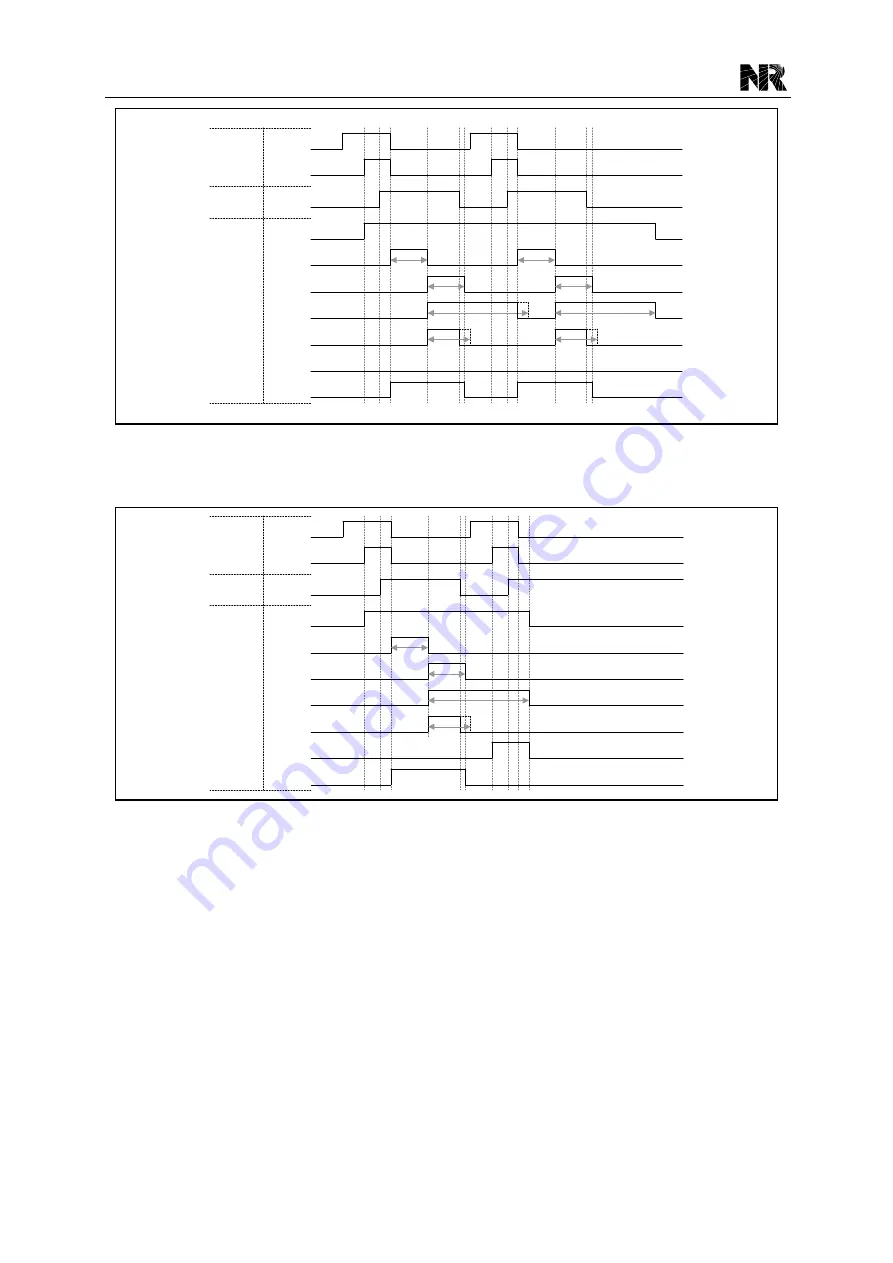
3 Operation Theory
PCS-9611 Feeder Relay
3-56
Date: 2014-04-08
Pickup
Trip
Open
Active
Reclose
Dead Time
Circuit
Breaker
Protection
Auto-
recloser
Reset
CB Check
79.t_Fail
79.t_Reclaim
79.t_3PS1
79.t_Fail
79.t_3PS2
79.t_Reclaim
79.t_DDO_AR
79.t_DDO_AR
Fail
Inprog
Figure 3.17-1 Timing diagram for a successful second reclosing
An example of a timing diagram for an unsuccessful one-shot reclosing is shown as below.
Pickup
Trip
Open
Active
Reclose
Dead Time
Circuit
Breaker
Protection
Auto-
recloser
Reset
CB Check
79.t_Fail
79.t_Reclaim
79.t_3PS1
79.t_DDO_AR
Fail
Inprog
Figure 3.17-2 Timing diagram for an unsuccessful one-shot reclosing
Summary of Contents for PCS-9611
Page 1: ...PCS 9611 Feeder Relay Instruction Manual NR Electric Co Ltd...
Page 2: ......
Page 10: ...1 Introduction PCS 9611 Feeder Relay 1 b Date 2014 04 08...
Page 30: ...2 Technical Data PCS 9611 Feeder Relay 2 14 Date 2014 04 08...
Page 36: ...3 Operation Theory PCS 9611 Feeder Relay 3 f Date 2014 04 08...
Page 108: ...4 Supervision PCS 9611 Feeder Relay 4 b Date 2014 04 08...
Page 116: ...5 Management Function PCS 9611 Feeder Relay 5 b Date 2014 04 08...
Page 120: ...5 Management Function PCS 9611 Feeder Relay 5 4 Date 2014 04 08...
Page 218: ...9 Configurable Function PCS 9611 Feeder Relay 9 b Date 2014 04 08...
Page 232: ...9 Configurable Function PCS 9611 Feeder Relay 9 14 Date 2014 04 08...
Page 262: ...11 Installation PCS 9611 Feeder Relay 11 b Date 2014 04 08...
Page 272: ...12 Commissioning PCS 9611 Feeder Relay 12 b Date 2014 04 08...
Page 292: ...13 Maintenance PCS 9611 Feeder Relay 13 b Date 2014 04 08...
Page 296: ...14 Decommissioning and Disposal PCS 9611 Feeder Relay 14 b Date 2014 04 08...
Page 298: ...14 Decommissioning and Disposal PCS 9611 Feeder Relay 14 2 Date 2014 04 08...
Page 300: ...15 Manual Version History PCS 9611 Feeder Relay 15 2 Date 2014 04 08...