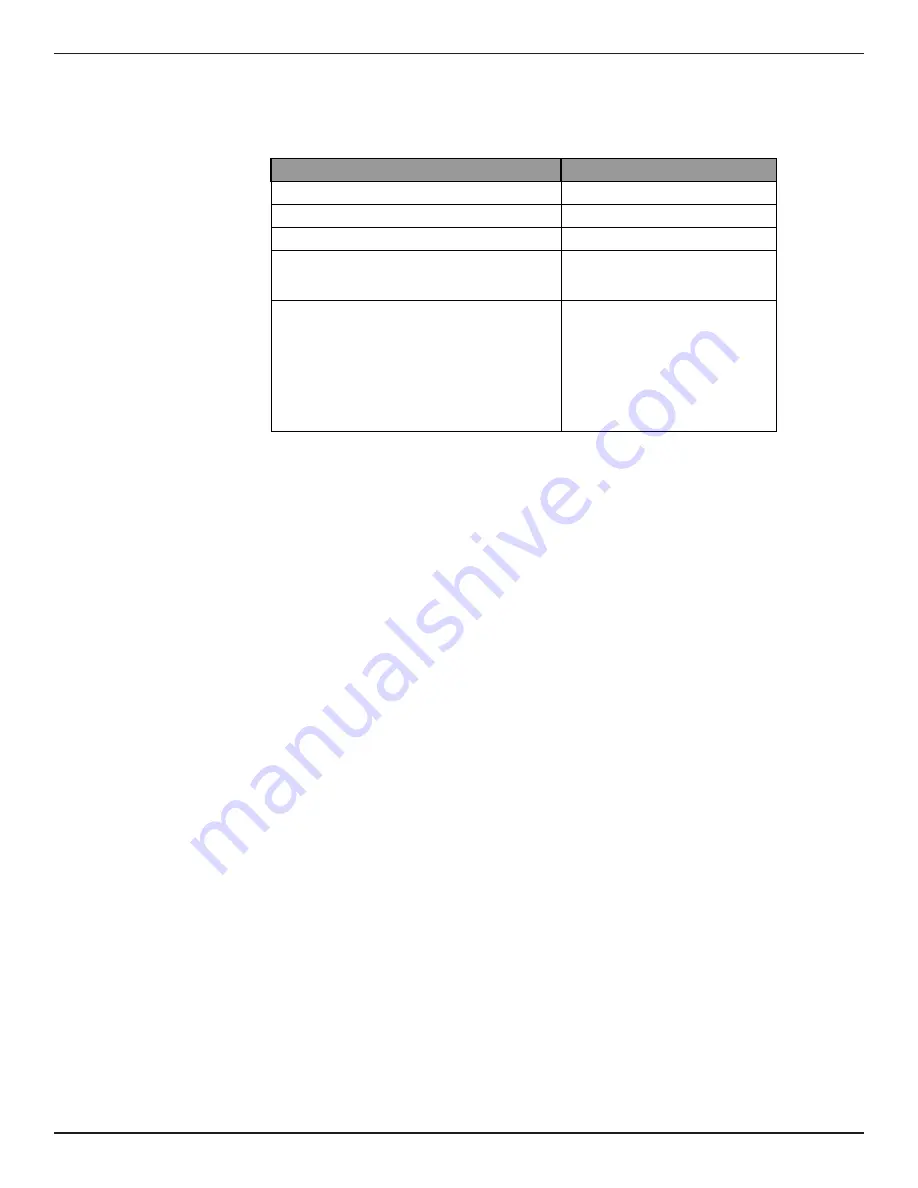
© 2021 Nordson Corporation
5-5
3. Make sure compressed air is being supplied to the feed center at above 5.5 bar
(80 psi) and that air pressures are adjusted properly. See Figure 2-9 for regulator
locations.
Table 5-1 Feed Center Air Pressure Settings
Air Pressure
Typical Setting
Lance Fluidizing (typical)
0.3 bar (5 psi) 0.03 Mpa
Feed Hopper Fluidizing (typical)
0.3 bar (5 psi) 0.03 Mpa
Purge
5.5 bar (80 psi) 0.55 Mpa
Purge Clamp
3.4−4.1 bar (50−60 psi)
0.34−0.41 Mpa
Lance Cylinder:
Up, 2 Lances
Up, 3 Lances
Up, 4 Lances
Down
4.1 bar (60 psi) 0.41 Mpa
4.8 bar (70 psi) 0.48 Mpa
5.5 bar (80 psi) 0.55 Mpa
3.4 bar (50 psi) 0.34 Mpa
4. Move a feed hopper or box into the feed center, and position it below the lance
assembly, adjusting the table stops as necessary. Select Hopper or Box with the
Powder Source Selector switch on the control panel.
5. If using a feed hopper:
a.
Connect the fluidizing tubing to the fitting on the feed hopper plenum.
b.
Fill the hopper 2/3 full of powder. Do not overfill; the powder expands when
fluidizing air is turned on.
c.
Gradually increase the feed hopper fluidizing air pressure until the powder is gently
boiling.
d. Lower the lance assembly into the hopper with the Lance Control switch. The lance
stops automatically above the fluidizing plate.
6. If using a powder box:
a. Turn on the vibratory table.
b. Lower the lance assembly into the box with the Lance Control Selector switch
(left for down) until the fluidizing bars and end of the level sensor are covered by
powder.
c.
Gradually increase the lance fluidizing air pressure until the powder is gently
boiling.
7. Make sure the sieve discharge pan is positioned so that the discharge tube directs the
screened powder into the feed hopper or box. Loosen the deck clamps to rotate the
pan, then re-clamp the deck.
8. If used, make sure the reclaim and virgin powder transfer hoses are connected to the
tubing stubs on the sieve deck. Turn on the reclaim transfer pump and enable the
virgin transfer pump.
9. Turn on the sieve.
10. Turn on the spray guns and start spraying powder. Make sure everything is working
correctly before starting production.
Summary of Contents for Encore XL Powder
Page 8: ...2021 Nordson Corporation 1607027 01 ii Change Record...
Page 12: ...2021 Nordson Corporation 1607027 01 1 4 Safety...
Page 51: ...2021 Nordson Corporation 1607027 01 4 9 Setup 6 5 Figure 4 5 Pneumatic Controls 2 of 2...
Page 60: ...2021 Nordson Corporation 1607027 01 5 8 Operation...
Page 136: ...2021 Nordson Corporation 1607027 01 9 34 Parts...
Page 146: ...2021 Nordson Corporation 1607027 01 10 10Options...
Page 148: ...2021 Nordson Corporation 1607027 01 11 2 Pneumatic and Electrical Diagrams...
Page 149: ......
Page 150: ......
Page 151: ......
Page 152: ......
Page 153: ...ON OFF...
Page 154: ......