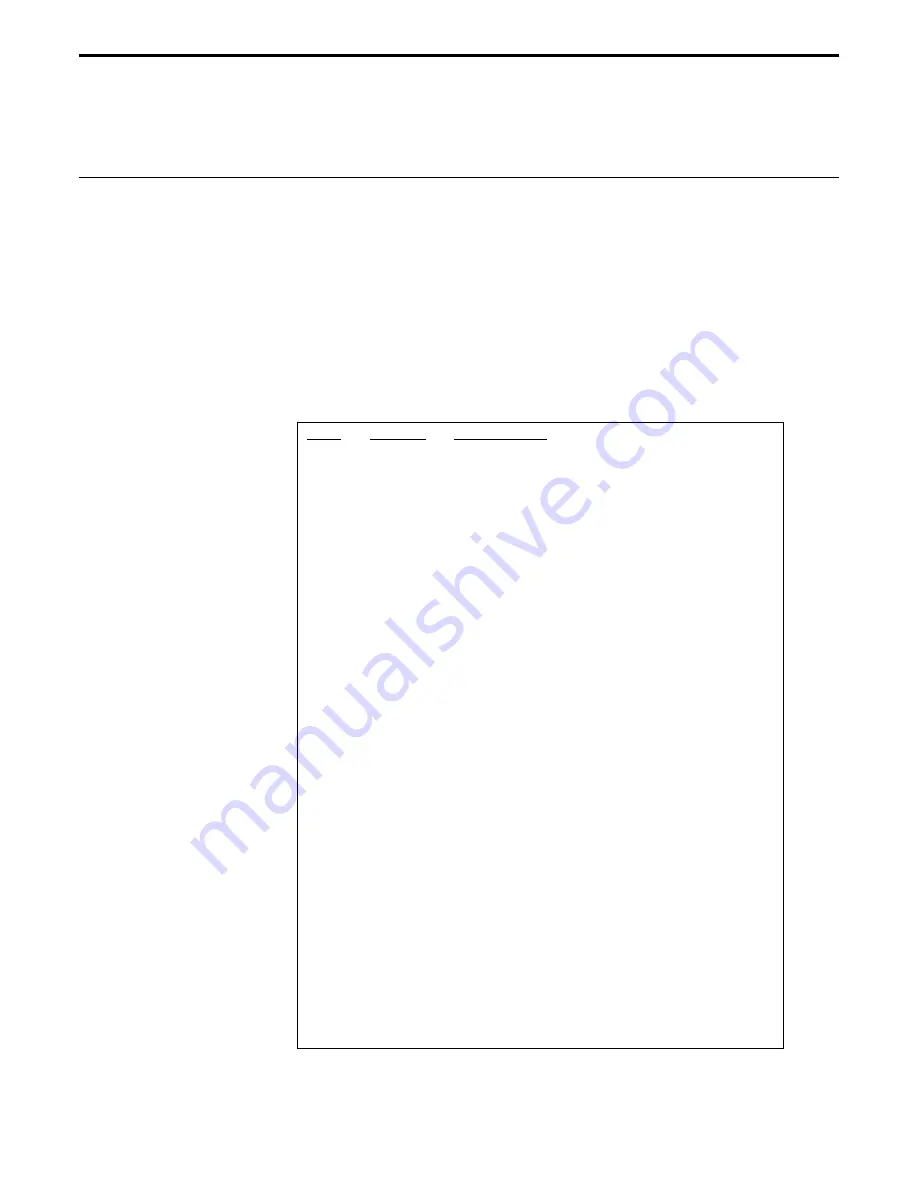
PH
get hardware status
IMM PGM MIP
USAGE
♦
♦
SYNTAX
PH
PARAMETERS
None
DESCRIPTION
This command is used to get general hardware status for all axes.
This routine allows user to observe the various digital input signals as they
appear to the controller.
H
ARDWARE
S
TATUS
R
EGISTER
#1
BIT
#
VALUE DEFINITION
0
0
axis 1 +hardware travel limit low
0
1
axis 1 +hardware travel limit high
1
0
axis 2 +hardware travel limit low
1
1
axis 2 +hardware travel limit high
2
0
axis 3 +hardware travel limit low
2
1
axis 3 +hardware travel limit high
3 0
reserved
3 1
reserved
4 0
reserved
4 1
reserved
5 0
reserved
5 1
reserved
6 0
reserved
6 1
reserved
7 0
reserved
7 1
reserved
8
0
axis 1 –hardware travel limit low
8
1
axis 1 –hardware travel limit high
9
0
axis 2 –hardware travel limit low
9
1
axis 2 –hardware travel limit high
10
0
axis 3 –hardware travel limit low
10
1
axis 3 –hardware travel limit high
11 0
reserved
11 1
reserved
12 0
reserved
12 1
reserved
13 0
reserved
13 1
reserved
14 0
reserved
14 1
reserved
15 0
reserved
15 1
reserved
Section 3 – Remote Mode
3-109
Summary of Contents for ESP300 Series
Page 1: ...ESP300 Motion Controller Driver User s Manual...
Page 4: ...ESP300 1999 EU Declaration of Conformity iv Preface...
Page 29: ...This page is intentionally left blank Section 2 Modes of Operation 1 15...
Page 30: ......
Page 230: ...4 16 Section 4 Advanced Capabilities...
Page 274: ...This page is intentionally left blank 6 6 Section 6 Servo Tuning...
Page 290: ...This page is intentionally left blank B 6 Appendix B Trouble Shooting and Maintenance...