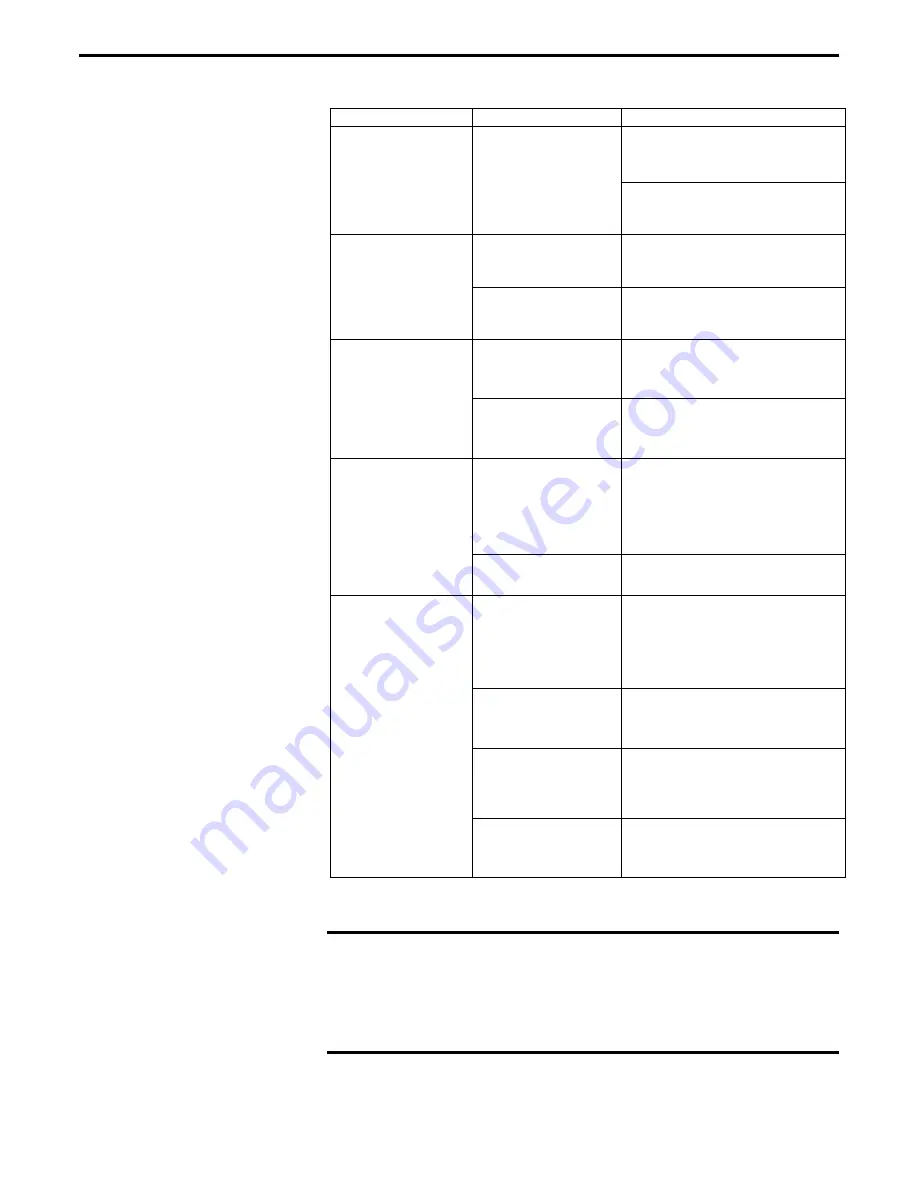
PROBLEM CAUSE CORRECTIVE
ACTION
Verify that all setup parameters
correspond to the actual motion
device installed.
Excessive following
error.
Wrong setup, load
specification
exceeded.
Verify that the load specifications
for the motion device are not
being exceeded.
Incorrect connection.
Verify that the motion device is
connected to the correct driver
card, as specified by the labels.
Axis does not move.
Incorrect parameters.
Verify that the motion device is
connected to the correct driver
card, as specified by the labels.
Incorrect connection.
Verify that the motion device is
connected to the correct driver
card, as specified by the labels.
System performance
below
Incorrect parameters.
Verify that all relevant parameters
(PID, velocity, etc.) are set
properly.
The software limit (See
SL
command) if the specified
direction was reached. If limits
are set correctly, do not try to
move past them.
Software travel limit
Move command not
executed.
Incorrect parameters
Verify that all relevant parameters
(PID, velocity, etc.) are set
Faulty origin or index
signals.
Carefully observe and record the
motion sequence by watching
manual knob rotation, if available.
With the information collected,
call Newport for assistance.
Wrong line
terminator.
Verify that the controller is set to
communicate on the right port,
RS-232 or IEEE488.
Home search not
completed.
Make sure that the computer and
the controller use the same line
terminator.
No remote
communication,
wrong
communication port.
Wrong
communication
parameters.
Verify that all communication
parameters match between the
computer and the controller.
Table B.1: Trouble-Shooting Guide Descriptions (Continued)
NOTE
Many problems are detected by the controller and reported on
the display and/or in the error register. Consult Appendix A,
Error Messages, for a complete list and description.
Appendix B – Trouble-Shooting and Maintenance
B-3
Summary of Contents for ESP300 Series
Page 1: ...ESP300 Motion Controller Driver User s Manual...
Page 4: ...ESP300 1999 EU Declaration of Conformity iv Preface...
Page 29: ...This page is intentionally left blank Section 2 Modes of Operation 1 15...
Page 30: ......
Page 230: ...4 16 Section 4 Advanced Capabilities...
Page 274: ...This page is intentionally left blank 6 6 Section 6 Servo Tuning...
Page 290: ...This page is intentionally left blank B 6 Appendix B Trouble Shooting and Maintenance...