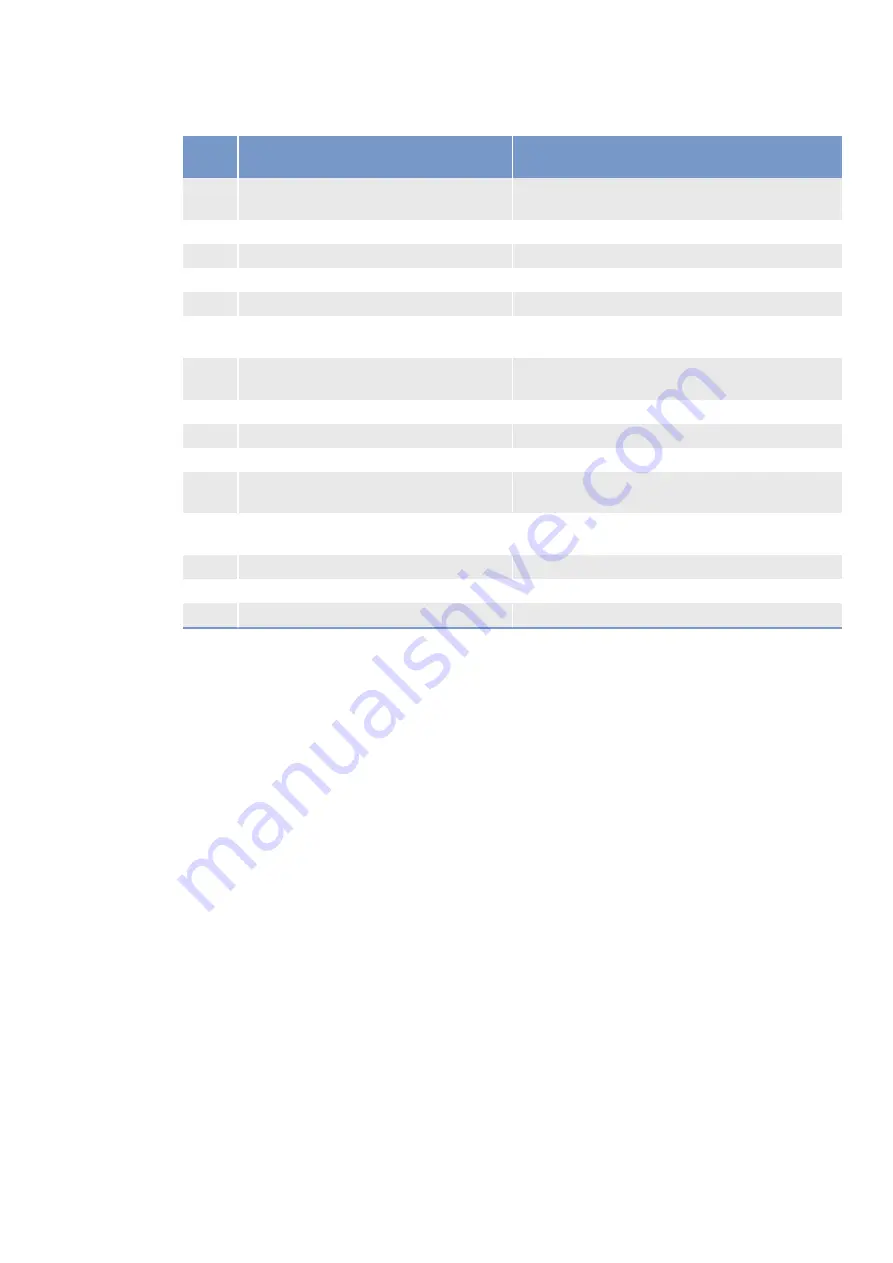
Abbre-
viation
Meaning
Explanation
TEN
Technical Evolution Network
Technical sales documentation, engine data, techni-
cal data
TS
Transfer Switch
—
T-xyz
Temperature-xyz
Temperature measuring point xyz
U
Symbol for electric voltage
UDP
User Datagram Protocol
Network protocol for communication via Ethernet
UL
Underwriters Laboratories
Global non-profit-making organization for product
safety testing and certification
Ultra-
Caps
UltraCaps modules
Starting system capacitors
UPS
Uninterruptible Power Supply
—
USV
Unterbrechungsfreie Stromversorgung
Uninterruptible Power Supply
UT
Unterer Totpunkt
Bottom Dead Center
VAwS
Verordnung über Anlagen zum Umgang mit
wassergefährdenden Stoffen
German rulebook on water pollution control
VDE
Verband der Elektrotechnik Elektronik In-
formationstechnik e.V.
Previously: Verband Deutscher Elektrotechniker;
German association of technology and science
VE
Versorgungseinheit
Supply unit
VFM
Vorfördermodul
Pre-feed module
WZK
Werkzeugkatalog
Tool Catalog
MS15065/01E 2019-01
| Appendix A | 329
TIM-ID: 0000056069 - 004