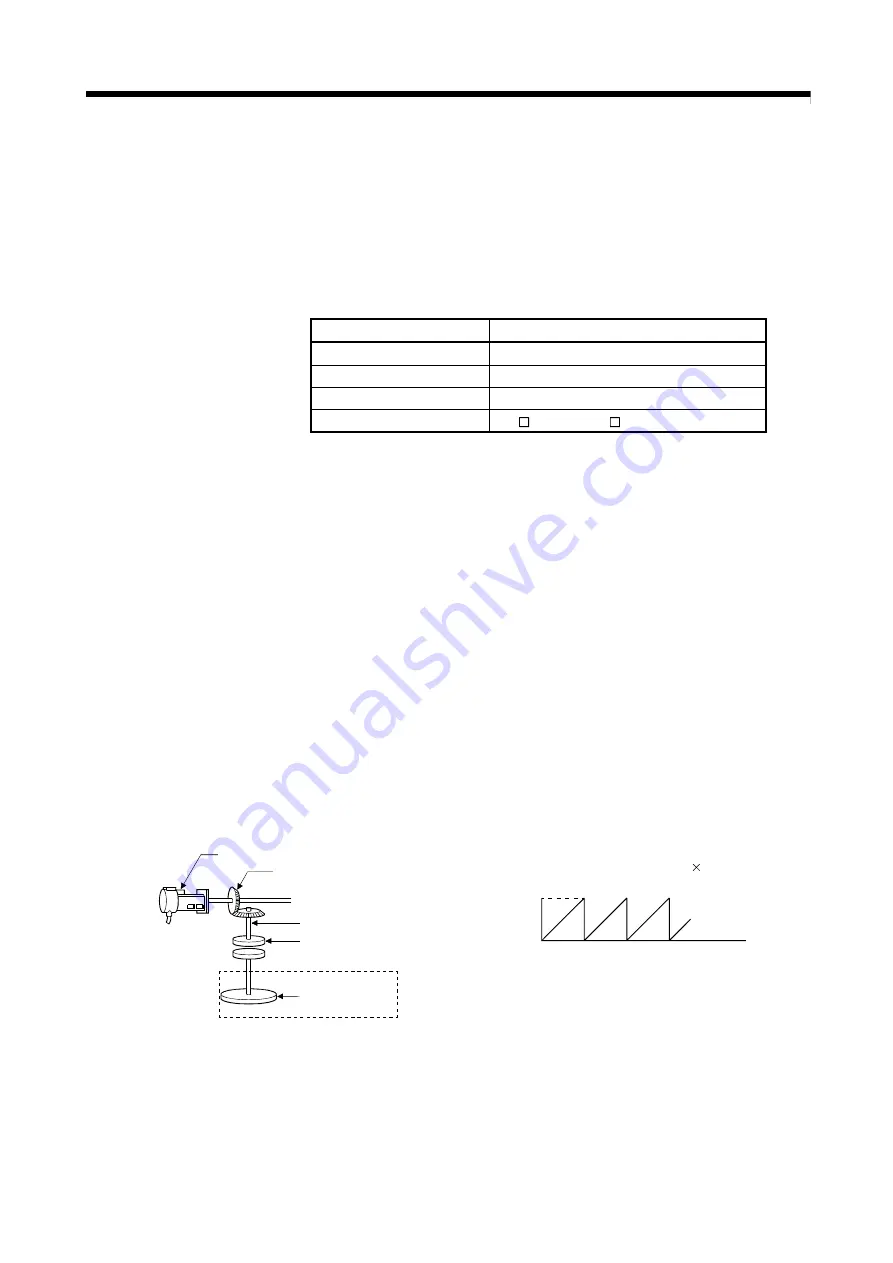
8 - 16
8 OUTPUT MODULE
(5) Torque limit value setting device (1 word)
(a) This device is used to set the torque limit value of rotary table axis.
When the device is set, the torque control is executed with the preset device
value.
In the virtual mode, the torque limit setting is always valid.
If the device is not set, the torque limit is set at 300[%].
(b) The following devices can be set as the torque limit value setting device.
Name Setting
range
Data register
D0 to D8191
(Note-1)
Link register
W0 to W1FFF
Motion register
#0 to #7999
Multiple CPU area device
U \G10000 to U \G(10000+p-1)
(Note-2)
(Note-1): D800 to D1559 are dedicated devices of virtual servomotor axis,
synchronous encoder axis and output module "Cam" in the virtual mode.
Unused areas of virtual servomotor axis and cam axis can be used as a
user device.
(Note-2): "p" indicates the user setting area points of the Multiple CPU high speed
transmission area for each CPU.
(c) The setting range for torque limit value is 1 to 1000[%].
(6) Comment
(a) This device is used to create a comment such as purpose of rotary table
axis.
Made comment can be displayed at monitoring using MT Developer2.
(b) Comments up to 32 characters long can be created.
(7) Current value within 1 virtual axis revolution
storage device
(Main shaft side) (2 words)
This parameter is set when the address mode clutch is set at the rotary table
main shaft side.
0
0
0
0
(N
D
-1)
PLS
Current value within 1 virtual axis revolution
= (Drive module travel value gear) %N
D
(% : Remainder operator)
The reference position (0) for the current value within
1 virtual axis revolution is set with the address clutch
reference setting command (M3213+20n).
Drive module
Current value within 1 virtual
axis revolution
Address mode clutch
Rotary table
Gear(Gear ratio)
(a) The current value within 1 virtual axis revolution of rotary table main shaft
side is stored in the preset device.
Summary of Contents for Q Series
Page 1: ......
Page 19: ...A 18 MEMO ...
Page 129: ...4 90 4 POSITIONING DEDICATED SIGNALS MEMO ...
Page 134: ...5 5 5 MECHANICAL SYSTEM PROGRAM MEMO ...
Page 139: ...5 10 5 MECHANICAL SYSTEM PROGRAM MEMO ...
Page 163: ...6 24 6 DRIVE MODULE MEMO ...
Page 201: ...7 38 7 TRANSMISSION MODULE MEMO ...
Page 257: ...9 12 9 REAL MODE VIRTUAL MODE SWITCHING AND STOP RE START MEMO ...
Page 267: ...10 10 10 AUXILIARY AND APPLIED FUNCTIONS MEMO ...
Page 352: ......