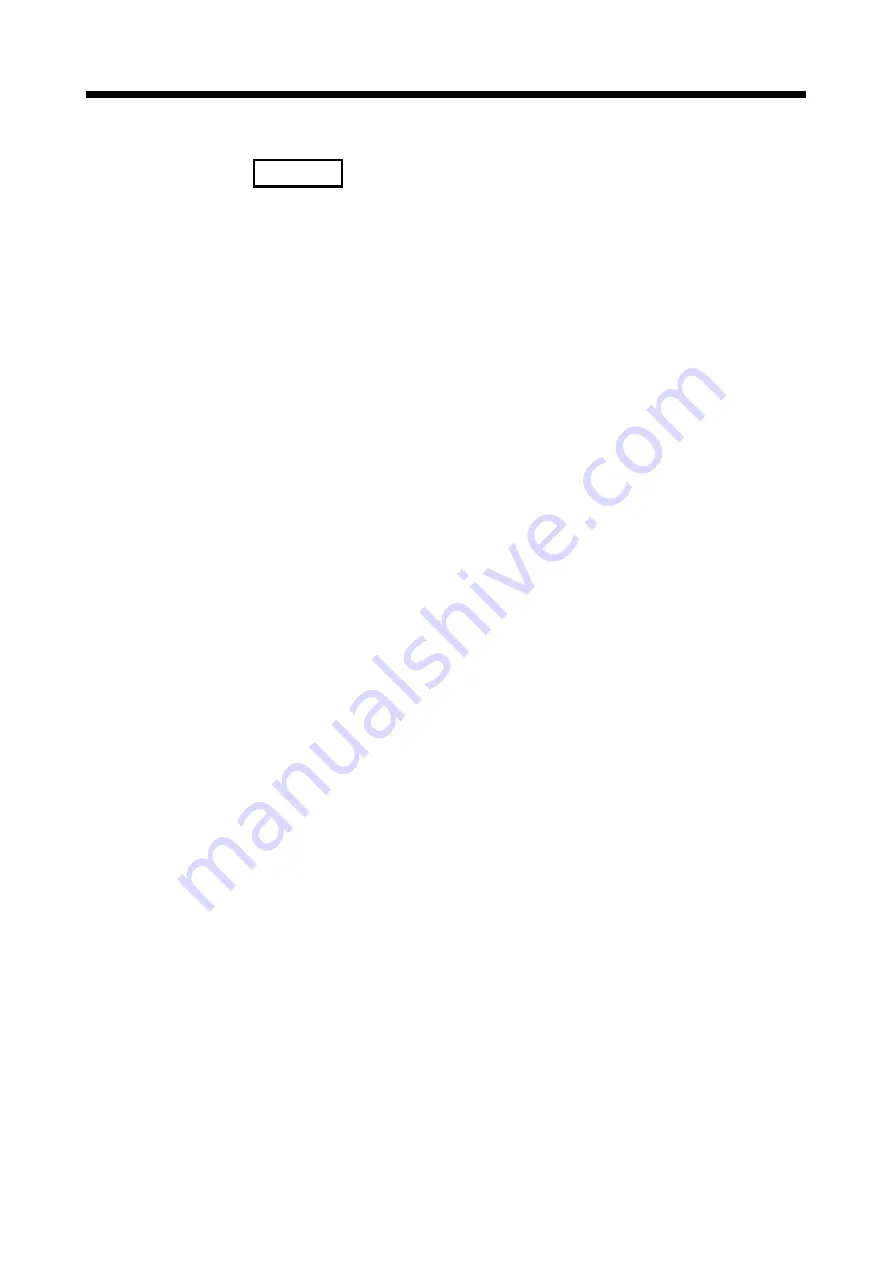
6 - 17
6 DRIVE MODULE
REMARK
(Note-1): Refer to Section 4.1.7 (9) (10) for details of the real mode/virtual mode
switching request flag and real mode/virtual mode switching status flag.
Refer to Chapter 9 for switching from real mode to virtual mode.
(Note-2): The synchronous encoder input start signal is inputted to the Q173DPX
"TREN" terminal.
Refer to the "Q173D(S)CPU/Q172D(S)CPU Motion controller User's
Manual" for details of the Q173DPX "TREN" terminal.
(Note-3): Refer to Section 7.2.1 for details of the clutch control mode.
(Note-4): The input pulse is always input after Multiple CPU system's power supply
ON in the real mode for the version (Refer to Section 1.4) that supports
"synchronous encoder current value monitor in real mode".
Refer to the "Q173D(S)CPU/Q172D(S)CPU Motion controller
(SV13/SV22) Programming Manual (REAL MODE)" for details.
(f) Error-time operation mode
The processings are shown below when major errors occurred with the
output modules per 1 system.
The following control is executed based on the parameter settings (Refer to
Table 6.2) of the synchronous encoder connected to the virtual main shaft.
1) Continuation
Even if a major error occurs with the output module, the output module
continues operation. At this time, the error detection signal
(M2407+20n) turns on, and the applicable error code is stored in the
major error code storage register.
Use the Motion SFC program for continue/stop of the system and the
output module operation at the major error occurrence.
2) Clutch OFF
If a major error occurs with the output module, the clutch within 1 system
turns off and stops connected output modules.
At this time, the clutch ON/OFF command device does not turn off.
However, the clutch status storage device turns off regardless of the
clutch ON/OFF command device's ON/OFF status.
Operation continues at axes where no clutch is connected.
Use the Motion SFC program to stop the drive module.
Eliminate the error cause, then turn the clutch ON/OFF command device
off to on to resume the operation.
Summary of Contents for Q Series
Page 1: ......
Page 19: ...A 18 MEMO ...
Page 129: ...4 90 4 POSITIONING DEDICATED SIGNALS MEMO ...
Page 134: ...5 5 5 MECHANICAL SYSTEM PROGRAM MEMO ...
Page 139: ...5 10 5 MECHANICAL SYSTEM PROGRAM MEMO ...
Page 163: ...6 24 6 DRIVE MODULE MEMO ...
Page 201: ...7 38 7 TRANSMISSION MODULE MEMO ...
Page 257: ...9 12 9 REAL MODE VIRTUAL MODE SWITCHING AND STOP RE START MEMO ...
Page 267: ...10 10 10 AUXILIARY AND APPLIED FUNCTIONS MEMO ...
Page 352: ......