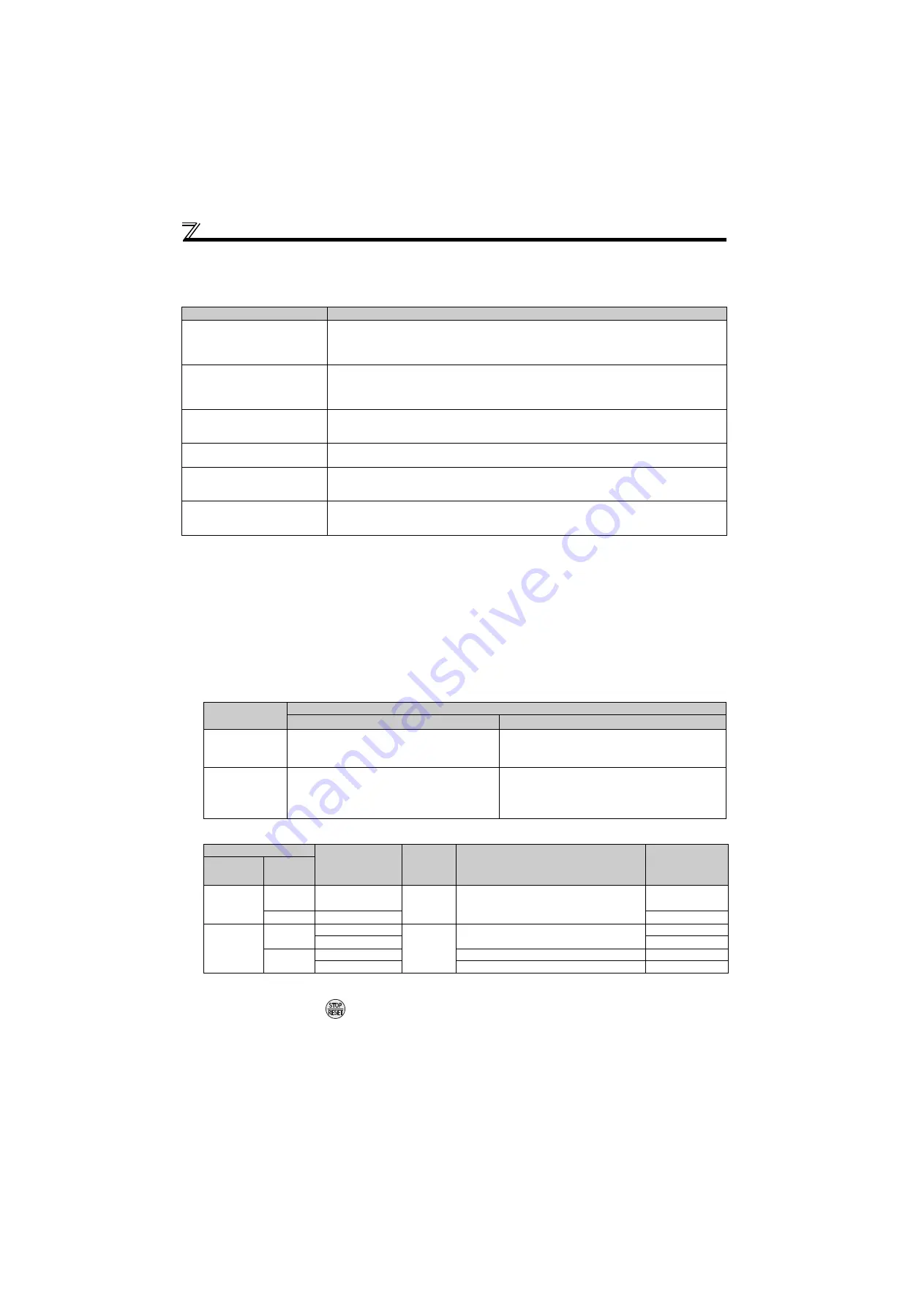
200
Selection of operation mode and operation location
(8) Switch-over mode
(setting "6")
While continuing operation, you can switch between the PU operation, external operation and network operation (when
RS-485 communication with the PU connector or communication option is used).
(9) PU operation interlock
(setting "7")
The PU operation interlock function is designed to forcibly change the operation mode to the External operation mode
when the PU operation interlock signal (X12) input turns OFF.
This function prevents the inverter from being inoperative by the external command if the mode is accidentally left
unswitched from PU operation mode.
Set "7" (PU operation interlock) in
Pr. 79
.
For the terminal used for X12 signal (PU operation interlock signal) input, set "12" to any of
Pr. 178 to Pr. 184 (input terminal
function selection)
to assign the function. (
for
Pr.178 to Pr.184
.)
When the X12 signal is not assigned, function of the MRS signal switches from MRS (output stop) to PU operation
interlock signal.
<
Function/operation changed by switching ON-OFF the X12 (MRS) signal
>
Operation Mode Switching
Switching Operation/Operating Status
External operation PU operation
Select the PU operation mode with the operation panel or parameter unit.
Rotation direction is the same as that of External operation.
The frequency set with the potentiometer (frequency command) or like is used unchanged. (Note
that the setting will disappear when power is switched OFF or the inverter is reset.)
External operation NET operation
Send the mode change command to the Network operation mode through communication.
Rotation direction is the same as that of External operation.
The value set with the setting potentiometer (frequency command) or like is used unchanged.
(Note that the setting will disappear when power is switched OFF or the inverter is reset.)
PU operation External operation
Press the external operation key of the operation panel or parameter unit.
The rotation direction is determined by the input signal of the External operation.
The set frequency is determined by the external frequency command signal.
PU operation NET operation
Send the mode change command to the Network operation mode through communication.
Rotation direction and set frequency are the same as those of PU operation.
NET operation External operation
Command to change to External mode is transmitted by communication.
Rotation direction is determined by the external operation input signal.
The set frequency is determined by the external frequency command signal.
NET operation PU operation
Select the PU operation mode with the operation panel or parameter unit.
The rotation direction and frequency command in the Network operation mode are used
unchanged.
X12 (MRS)
Signal
Function/Operation
Operation mode
Parameter write
ON
Operation mode (External, PU, NET) switching
enabled
Output stop during External operation
Parameter write enabled (depending on
Pr. 77 Parameter
write selection
and each parameter write conditions (
for the parameter list))
OFF
Forcibly switched to External operation mode
External operation allowed
Switching between the PU and NET operation mode
is enabled
Parameter write disabled with exception of
Pr. 79
Operating Condition
X12 (MRS) Signal
Operation
Mode
Operating Status
Switching to PU,
NET Operation
Mode
Operation
mode
Status
PU/NET
During
stop
ON OFF
∗1
External
∗2
If external operation frequency setting and
start signal are entered, operation is
performed in that status.
Disallowed
Running
ON OFF
∗1
Disallowed
External
During
stop
OFF ON
External
∗2
During stop
Allowed
ON OFF
Disallowed
Running
OFF ON
During operation output stop
Disallowed
ON OFF
Output stop operation
Disallowed
∗1
The operation mode switches to the External operation mode independently of whether the start signal (STF, STR) is ON or OFF. Therefore, the
motor is run in External operation mode when the X12 (MRS) signal is turned OFF with either of STF and STR ON.
∗2
At fault occurrence, pressing
of the operation panel resets the inverter.
Summary of Contents for FR-E710W-0.1K
Page 49: ...40 MEMO ...
Page 65: ...56 MEMO ...
Page 288: ...288 MEMO ...
Page 310: ...310 MEMO ...
Page 334: ...334 MEMO ...
Page 348: ...4 4 BCN C22005 679 MEMO BCN C22005 679 fm 4 ページ 2014年11月7日 金曜日 午前11時58分 ...