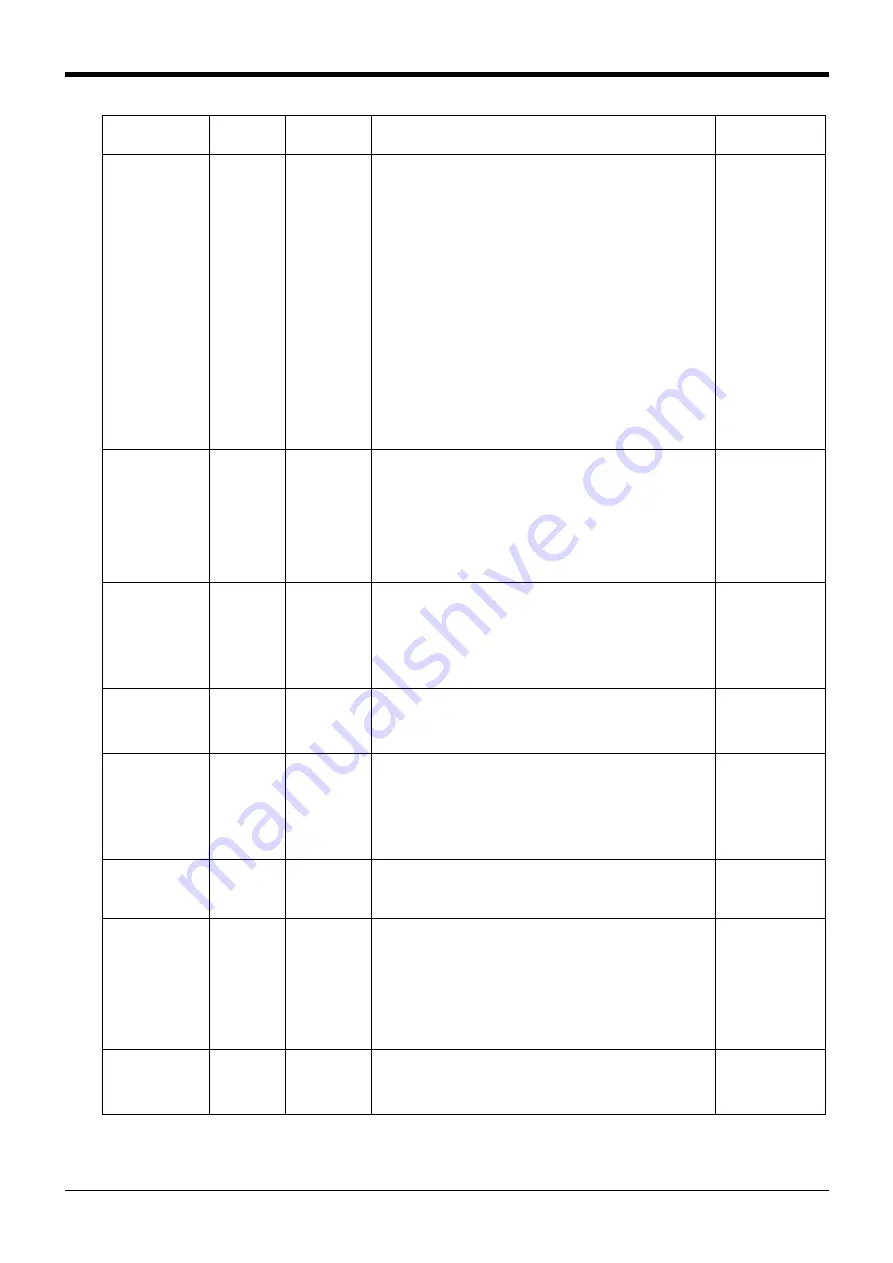
5Functions set with parameters
Movement parameter
5-451
Functional setting
of compliance error
CMPERR
Integer 1
Setting this parameter prevents errors 2710 through 2740 (errors
that occur if the position command generated in compliance
control is abnormal) from occurring.
1: Enable error generation
0: Disable error generation
The contents of applicable errors are as follows:
2710: The displacement from the original position command
is too large.
2720: Exceeded the joint limit of the compliance command
2730: Exceeded the speed of the compliance command
2740: Coordinate conversion error of the compliance
command
If these errors occur, compliance control is not functioning
normally. It is thus necessary to re-examine the teaching position
and the program content to correct the causes of these errors.
Change this parameter value to 0 (disable error generation) only
when you can determine that doing so does not cause any
operational problem even if the current operation is not
suspended by an error.
1 (Enable error
generation)
Current limit level
for Cmp Jnt
CMPJCLL
Integer 1
Change the motor current limit level of each axis in the
compliance mode (Cmp Jnt instruction) of the joint coordinate
system.
Setting range: 1 (High) to 10 (Low).
While operation is performed in the compliance mode of the joint
coordinate system, if the Excessive error 1 (H096n) occurs,
increase the set value of this parameter to suppress the error.
(The set valve after the change will be applied from the next exe-
cution of Cmp Jnt instruction.)
1
Optimization of
overload detection
level
OLTMX
Integer 1
Set the upper limit of the ambient temperature for the robot’s
working environment.
The overload detection level for robot movement is optimized
based on this setting value. (Unit: °C)
Setting range: 0-40
Please refer to
Page 521, "5.22 Optimizing the overload level"
for details of this parameter's function.
RH-3FH/6FH/12FH/
20FH: 40
RV-2F series: 40
RV-4F/7F/13F/20F/
50F series, RH-
3FHR: 30
Motor overheat
warning
MOHW
Specifies whether or not to warn before a motor overheat error
occurs.
0: Disable
1: Enable
1
Occurrence interval
of battery error
ITBATERR
Integer 1
Specifies a time interval at which to generate a battery
exhaustion time error alarm
(in hours)
Setting range: 1 to 336
When a set value is less than 1, "1" is taken as being
specified; when a set value is greater than 336, "336" is taken
as being specified
24
Synchronize time
with PLC
(CR7xx-Q series
only)
TIMESYNC
Integer 1
Choose whether to synchronize time of the robot controller and
the PLC.
(Synchronize/ Not synchronize = 1/0)
0
Definition of the
Wait command
function
*Available soft-
ware versions
S/W Ver.
F-Q series:
R5q or later
F-D series:
S5q or later
PRSPEC
Integer 1
Set the execution method of the Wait command.
0: Conditional command (two or more conditional expressions
can be written.)
1: Operation command (only one conditional expression can
be written.)
1
WthIf command
function
WTHFUNC
Integer 1
Specifies a stop type of WthIf command.
0: stop type 1
1: stop type 2
Refer to a explanation of Def Act command about the stop type.
0
Parameter
Parameter
name
No. of arrays
No. of characters
Details explanation
Factory setting