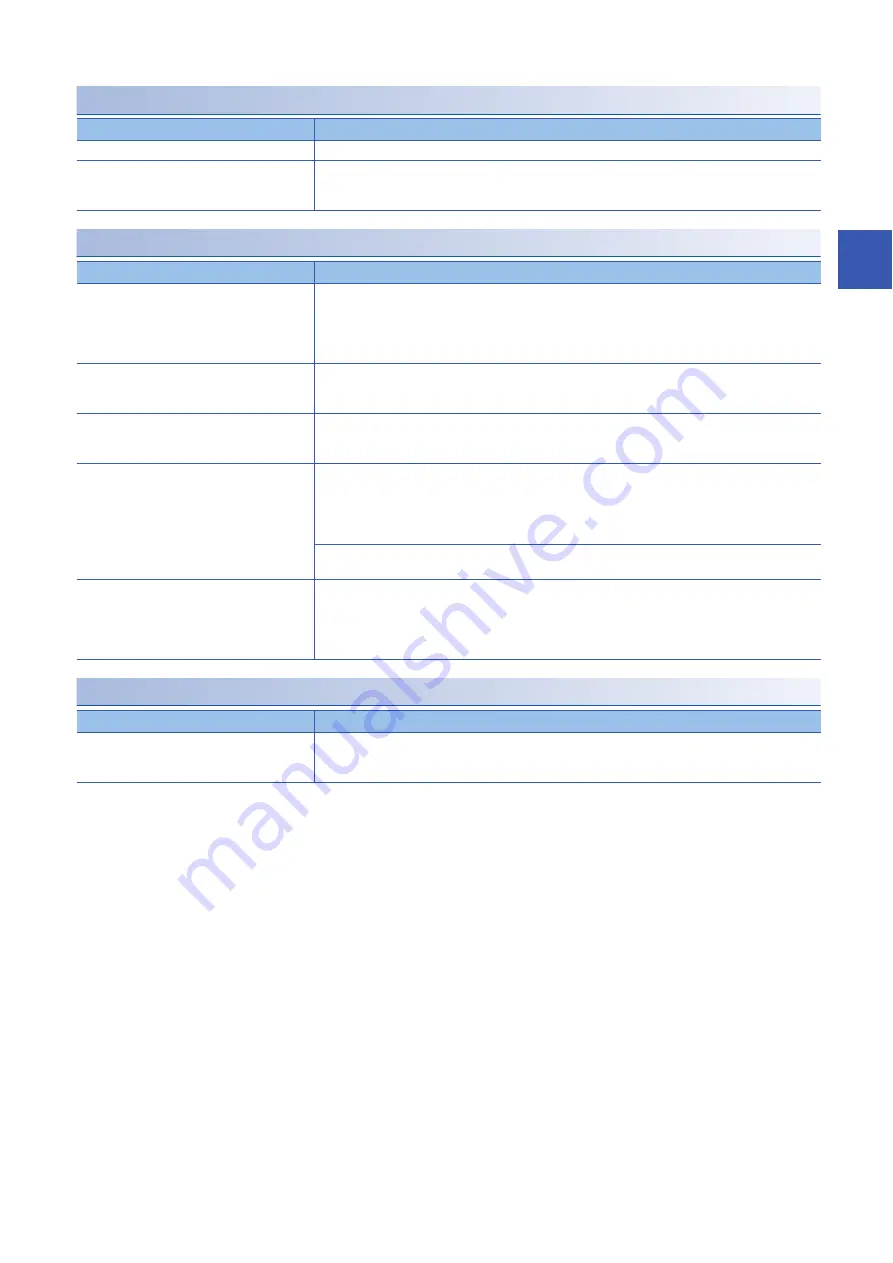
11 TROUBLESHOOTING
11.4 Troubleshooting for Each Phenomenon
123
11
When parameters cannot be read or written
When an IO-Link device cannot be communicated with
When a signal incorrectly inputs data
Check item
Action
Is the version of the engineering tool supported?
Please consult your local Mitsubishi representative.
Do the setting of the network parameter and that
of the CPU module match?
Perform sequencer verification on the network parameter to check those settings. When they are not
matched, match the setting of the network parameter to that of the sequencer and write the module
parameter of the slave station.
Check item
Action
Is the process data size is assigned properly to
each channel?
For the process data size, specify the number of words not less than the process data size of the IO-Link
device used.
(If the IO-Link device controls 3-byte process data, set the process data size to two words (4 bytes) or
more.)
For details, refer to the specifications of the IO-Link device used.
Is device validation configured properly?
If the device is determined to be not compatible or identifiable as a result of device validation, check
whether an intended IO-Link device is connected or review the IO-Link device connection.
Check also if the IO-Link device validation setting on the IO-Link module is correct.
Is the setting of the refresh device correct?
Check the refresh parameter and correct the setting of the refresh device so that it matches with the setting
in the program. For the setting of the refresh parameters, refer to the following.
User's manual for the master/local module used
Is Remote READY (RWr0.b11) on?
To enable reading/writing process data when the module power supply is on, the initial processing must be
executed by using Initial processing request flag (RWr0.b8) and Initial processing completion flag
(RWw0.b8). Execute the initial processing to check that Remote READY (RWr0.b11) is on. For details, refer
to the following.
Page 143 Remote READY (RWr0.b11)
Connect the engineering tool to the master station, and then check that a data link is established in the own
station by using CC IE Field diagnostics. (
User's manual for the master/local module used)
Is any bit of Channel n (CQ/Q) short-circuit
detection flag (RX10 to RX1F) and Channel n
(L+) short-circuit detection flag (RX20 to RX27)
turned on?
If any bit of Channel n (CQ/Q) short-circuit detection flag (RX10 to RX1F) and Channel n (L+) short-circuit
detection flag (RX20 to RX27) is turned on, this means that an error such as short-circuit is detected on the
channel corresponding to the bit.
Check the wiring confirming that the wiring is not disconnected or short-circuited, or the voltage of the
signal is correct.
Check item
Action
Is noise taken as input data?
• To prevent excessive noise, avoid installing power cables together with I/O cables.
• Connect surge absorbers to noise-generating devices such as relays and conductors using the same
power supply or take other noise reduction measures.
Summary of Contents for CC-Link IE Field NZ2GF12A-60IOLH8
Page 1: ...CC Link IE Field Network Waterproof Remote IO Link Module User s Manual NZ2GF12A 60IOLH8 ...
Page 2: ......
Page 30: ...28 3 PROCEDURES BEFORE OPERATION MEMO ...
Page 100: ...98 8 MODULE FUNCTION BLOCKS MEMO ...
Page 109: ...9 PROGRAMMING 9 2 Program Example of Setting Parameters Using a Dedicated Instruction 107 9 ...
Page 116: ...114 9 PROGRAMMING 9 3 Example of Program to Communicate with an IO Link Device ...
Page 118: ...116 10 MAINTENANCE AND INSPECTION MEMO ...
Page 155: ...APPX Appendix 7 Additional or Changed Functions 153 A MEMO ...
Page 157: ...I 155 MEMO ...
Page 161: ......