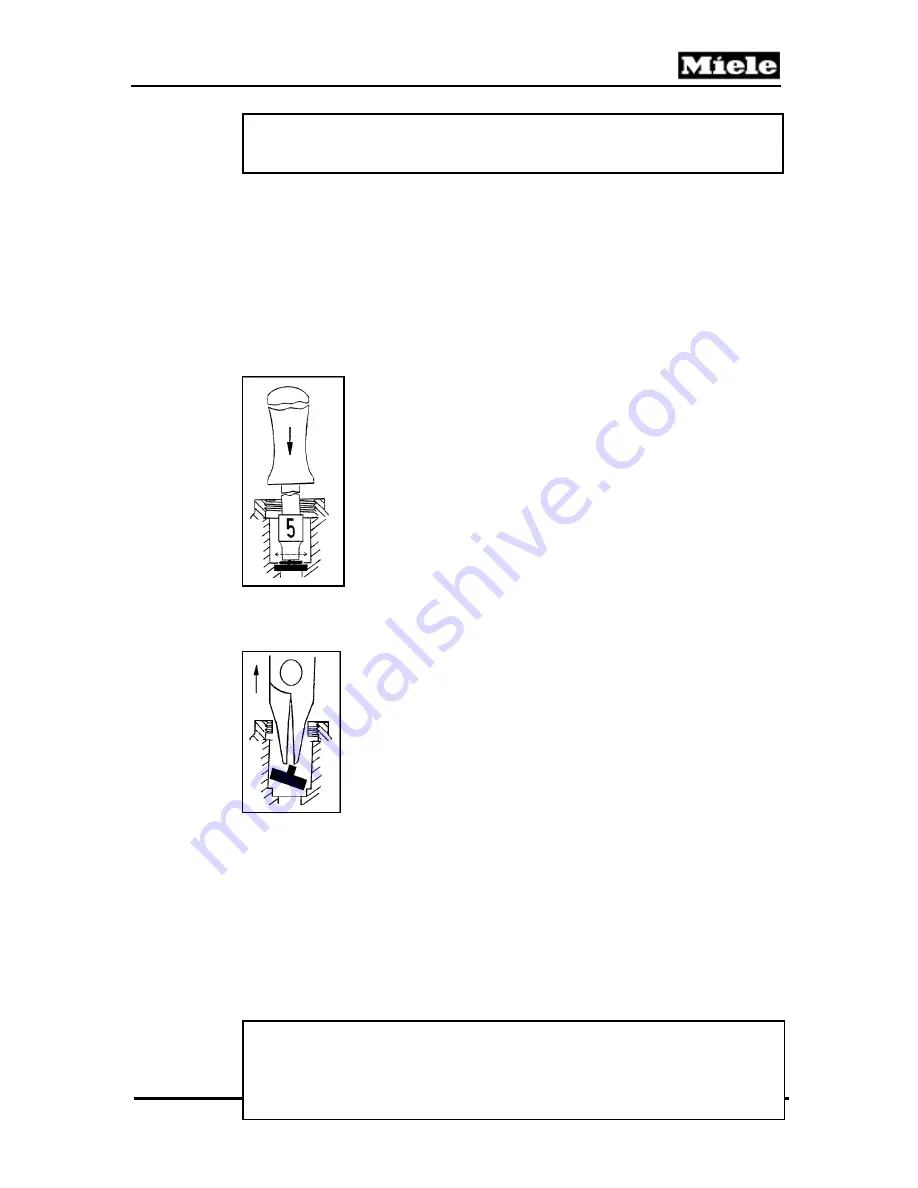
Technical Information
83
G1000 / G2000 Dishwashers
Note
For the G1000 and G2000 series, green restrictors (4.1 l/min) must be
fitted in the WaterProof System valve holder.
1. Shut off the water supply.
2. Disconnect the WPS at the plumbing supply connection.
3. Remove the sealing washer and filter from inside the WPS connection. Using a
5mm nut-driver; press and tilt the restrictor to the side; as shown in Figure 5-26.
4. Remove the Restrictor - Figure 5-27.
5. Install the new restrictor using a suitable 5 mm socket / nutdriver to seat it firmly
and evenly into place. Re-install the filter and sealing washer.
Figure 5-26:
Tilting the Flow Restrictor
Figure 5- 27:
Removing the Flow Restrictor.
5.4.2
WaterProof System (WPS) - Removal
Note
In the event the intake hose or water valves require replacement,
the WPS
must
be replaced as a complete assembly. Individual
replacement of the parts is not possible.