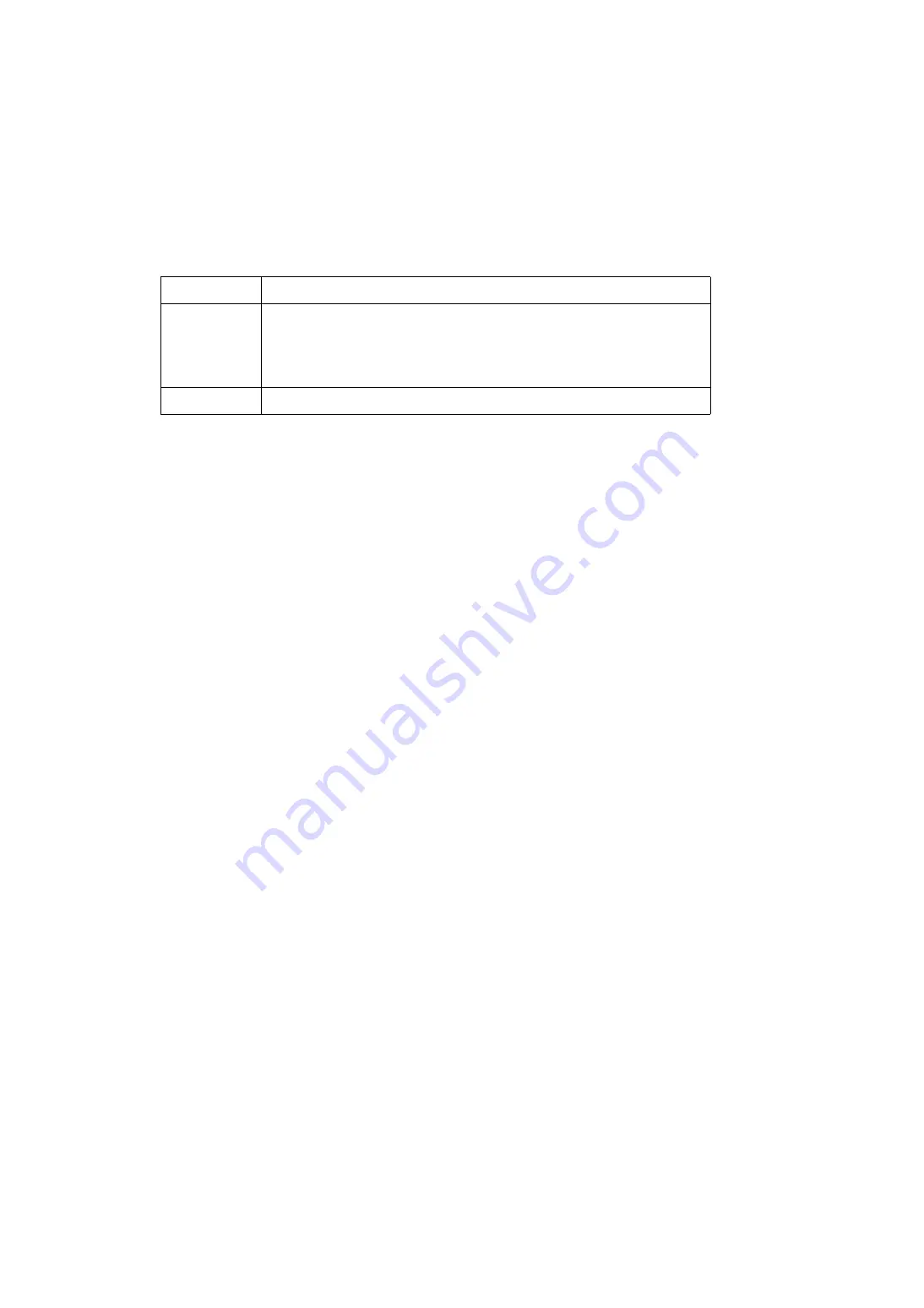
NSS250S/A TYPE CODE
• Throughout this manual, the following abbreviations are used to identify individual model.
CODE
AREA TYPE
ED
EUROPEAN DIRECT SALES
(Austria, Belgium, Bulgaria, Croatia, Czech, Denmark, Finland, Germany,
Greece, Holland, Hungary, Iceland, Israel, Italy, Latvia, Luxembourg,
Macedonia, Norway, Poland, Portugal, Romania, Russia, Slovakia, Slovenia,
Spain, Sweden, Switzerland, Ukraine)
F
France
maxiscooter-club.ru
Summary of Contents for NSS250A Reflex 2001-2007
Page 68: ...MEMO maxiscooter club ru...
Page 114: ...MEMO maxiscooter club ru...
Page 140: ...MEMO maxiscooter club ru...
Page 154: ...MEMO maxiscooter club ru...
Page 280: ...MEMO maxiscooter club ru...
Page 294: ...MEMO maxiscooter club ru...
Page 322: ...CYLINDER PISTON 10 2 CYLINDER PISTON COMPONENT LOCATION maxiscooter club ru...
Page 366: ...MEMO maxiscooter club ru...
Page 418: ...MEMO maxiscooter club ru...
Page 450: ...MEMO maxiscooter club ru...
Page 542: ...MEMO maxiscooter club ru...
Page 554: ...MEMO maxiscooter club ru...
Page 644: ...MEMO maxiscooter club ru...
Page 707: ...25 1 25 25 WIRING DIAGRAMS NSS250S 25 3 NSS250A 25 4 maxiscooter club ru...
Page 715: ...MEMO maxiscooter club ru...