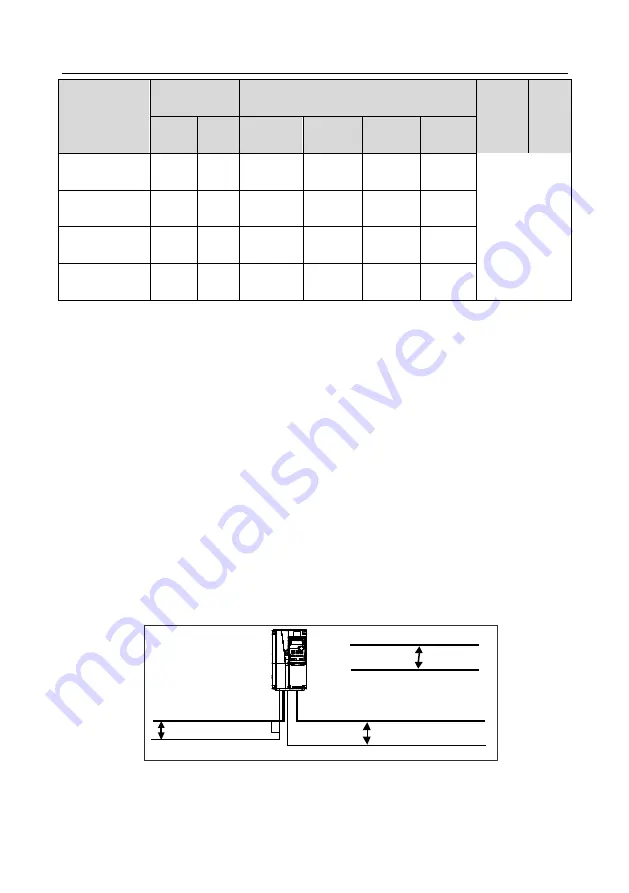
S1 series standard inverter
-218-
Inverter model
Recommended
cable size (mm
2
)
Size of connectable cable (mm
2
)
Terminal
screw
specifica
tion
Tighten
ing
torque
(Nm)
RST
UVW
PE
RST
UVW
P1, (+)
PB, (+), (-)
PE
S1-06000HFEF
95×4P 95×2P
95×4P
–150×4P
95×4P
–150×4P
95×4P
–150×4P
95×2P
–150×2P
Nuts are used as
terminals, so it is
recommended that
you use a wrench
or sleeve.
S1-06500HFEF
95×4P 95×4P
95×4P
–150×4P
95×4P
–150×4P
95×4P
–150×4P
95×2P
–150×2P
S1-07200HFEF
95×4P 95×4P
95×4P
–150×4P
95×4P
–150×4P
95×4P
–150×4P
95×2P
–150×2P
S1-08600HFEF
150×4P 150×2P
95×4P
–150×4P
95×4P
–150×4P
95×4P
–150×4P
95×2P
–150×2P
Note:
1.
Cables of the sizes recommended for the main circuit can be used in scenarios where the
ambient temperature is lower than 40°C, the wiring distance is shorter than 100 m, and the
current is the rated current.
2.
The terminals P1, (+), and (-) are used to connect to DC reactors and brake accessories.
12.4.4 Cable arrangement
Motor cables must be arranged away from other cables. The motor cables of several inverters can be
arranged in parallel. It is recommended that you arrange the motor cables, input power cables, and
control cables separately in different trays. The output dU/dt of the inverters may increase
electromagnetic interference on other cables. Do not arrange other cables and the motor cables in
parallel.
If a control cable and power cable must cross each other, ensure that the angle between them is 90
degrees.
The cable trays must be connected properly and well grounded. Aluminum trays can implement local
equipotential.
The following figure shows the cable arrangement distance requirements.
Input power cable
Min 200mm
Control cable
Motor cable
Min 500mm
Control cable
Motor cable
Power cable
Min 300mm
90°