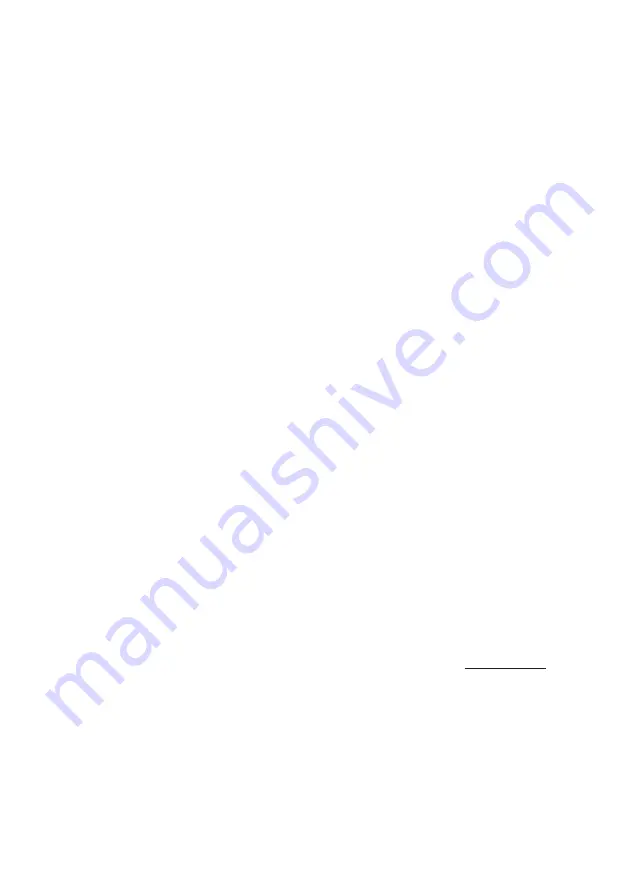
Chapter 7 Appendix • 334
ARTDrive V2 series - Instruction Manual
7.5.3.2 Input/Output
Drive settings: (only those referring to the PID function are described)
Connect to the analog input 1 the Dancer cursor.
Select
PID fbk src
=
An inp 1 output
Connect to the analog input 2 the line speed reference (feed- forward).
Select
PID inp FF src
=
An inp 2 output
Connect to the speed 1 reference the PID output
Select
Speed ref 1 src
=
PID out mon
Set
Ramp out enable
= Disable
Connect to the Digital input 1 the input enabling the PID PI Block
Select
PID PI enab src
=
DI 1 monitor
Connect to the Digital input 2 the input enabling the PID PD Block.
Select
PID PD enab src
=
DI 2 monitor
In case just one contact is needed to enable the PI and PD section, it is
possible to connect also
PID PD enab src
on the digital input 1 as described
below.
Select
PID PD enab src
=
DI 1 monitor
Connect to the Digital input 3 the input enabling the diameter calculation
Block
Select
DiaClc start src
=
DI 3 monitor
Connect to the digital output 0 the signal stating the end of the diameter
calculation
Select
DO 0 src
=
Diacalc active
7.5.3.3 Parameters
Set
Full scale spd
equal to the motor speed corresponding to 100% of the
line speed with a minimum winder diameter (core).
Full scale spd
= 2550 rpm
Calculation of the motor speed according to the above stated conditions:
Vp =
π
x
Φ
min x
ω
x R
where:
Vp = winder peripheral speed = line speed
Φ
min = winder minimum diameter [m]
ω
= motor angular speed [rpm]
R = motor-winder reduction ratio
ω
= Vp /
π
x
Φ
min x R = 400 / (
π
x 0.1 x 0.5) = 2546rpm = about 2550rpm
Connect
Mlt PI sel 0
= Null
Mlt PI sel 1
= Null
With this configuration it is possible to carry out, via a suitable procedure, the
calculation of the starting diameter. Furthermore the last calculated diameter
value is kept into memory both if the machine is stopped and if the
switchboard is switched off.
As previously stated, the procedure determines the theoretic multiplicative
factor (
PI output PID
) of the feed-forward as compared to the calculated
Summary of Contents for ARTDrive Vector V2 400Vac Series
Page 1: ...Instruction Manual ARTDrive ARTDrive Vector AC Drives V2 series 400Vac Class 575Vac Class...
Page 14: ...0 14 Chapter 0 Safety Precautions ARTDrive V2 series Instruction manual...
Page 40: ...40 Chapter 3 Installation Guidelines ARTDrive V2 series Instruction Manual...
Page 92: ...92 Chapter 5 Quick Start Up Guide ARTDrive V2 series Instruction Manual...
Page 358: ...358 Chapter 8 Appendix ARTDrive V2 series Instruction Manual...
Page 376: ...Chapter 9 Pick Lists 376 ARTDrive V2 series Instruction manual...