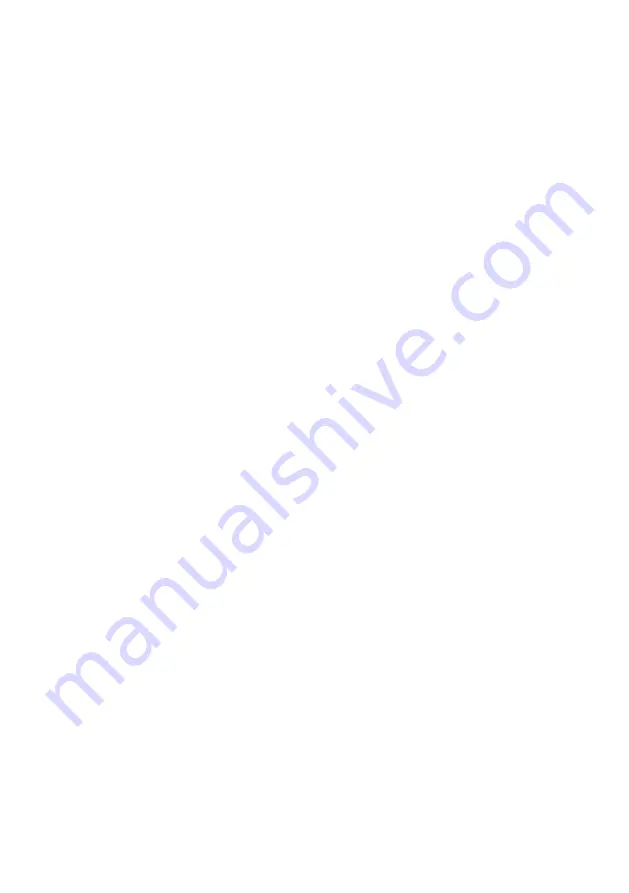
ARTDrive V2 series - Instruction Manual
Chapter 7 Appendix • 329
7.5.1.2 Input/Output
Drive settings: (only those referring to the PID function are described)
Connect to the analog input 1 the dancer cursor.
Select
PID fbk src
=
An inp 1 output
Connect to the analog input 2 the line speed reference (feed- forward).
Select
PID inp FF src
=
An inp 2 output
Connect to the Digital input 1 the input enabling the PID PI Block
Select
PID PI enab src
=
DI 1 monitor
Connect to the Digital input 2 the input enabling the PID PD Block
Select
PID PD enab src
=
DI 2 monitor
In case just one contact is required to enable the PI and PD section, it is
possible to connect also PID PD enab src on the digital input 1 as described
below.
Select
PID PD enab src
=
DI 1 monitor
Connect to the speed 1 reference the PID output
Select
Speed ref 1 src
=
PID out mon
Set
Ramp out enable
= Disable
7.5.1.3 Parameters
Set
Full scale spd
equal to the motor speed corresponding to 100% of the
line speed.
Full scale spd
= 2550 rpm
Connect
Mlt PI sel 0
= Null
Mlt PI sel 1
= One
The selection of the PID Mlt PI sel 1 multiplier is therefore active.
Set
PID Mlt PI sel 1
= 1
The starting value is 1
In case the regulator PI Block has performed no correction, the line speed
reference (Feed-Forward) has to be multiplied by 1 and sent directly to the
Drive regulator speed.
With this application, the regulator usually carries out a proportional control.
The correction is stated as a percentage of the line speed, from 0 to the
maximum value.
Set
PI clamp top
and
PI clamp bot
so that, with a maximum mechanical
sealing of the dancer (maximum value of the analog input 1 connected to the
dancer reaction), and by setting the proportional gain of the PI block to 15%,
a corresponding proportional correction of the feed-forward is obtained.
Set therefore:
PI clamp top
= 10
PI clamp bot
= 0.1
Set
PI P1 gain %
= 15% 1 or 3 see error during test
Set
PI I1 gain %
= 0%
Summary of Contents for ARTDrive Vector V2 400Vac Series
Page 1: ...Instruction Manual ARTDrive ARTDrive Vector AC Drives V2 series 400Vac Class 575Vac Class...
Page 14: ...0 14 Chapter 0 Safety Precautions ARTDrive V2 series Instruction manual...
Page 40: ...40 Chapter 3 Installation Guidelines ARTDrive V2 series Instruction Manual...
Page 92: ...92 Chapter 5 Quick Start Up Guide ARTDrive V2 series Instruction Manual...
Page 358: ...358 Chapter 8 Appendix ARTDrive V2 series Instruction Manual...
Page 376: ...Chapter 9 Pick Lists 376 ARTDrive V2 series Instruction manual...